Efficient Networks Siemens Sinamics S120 User Manual
Page 337
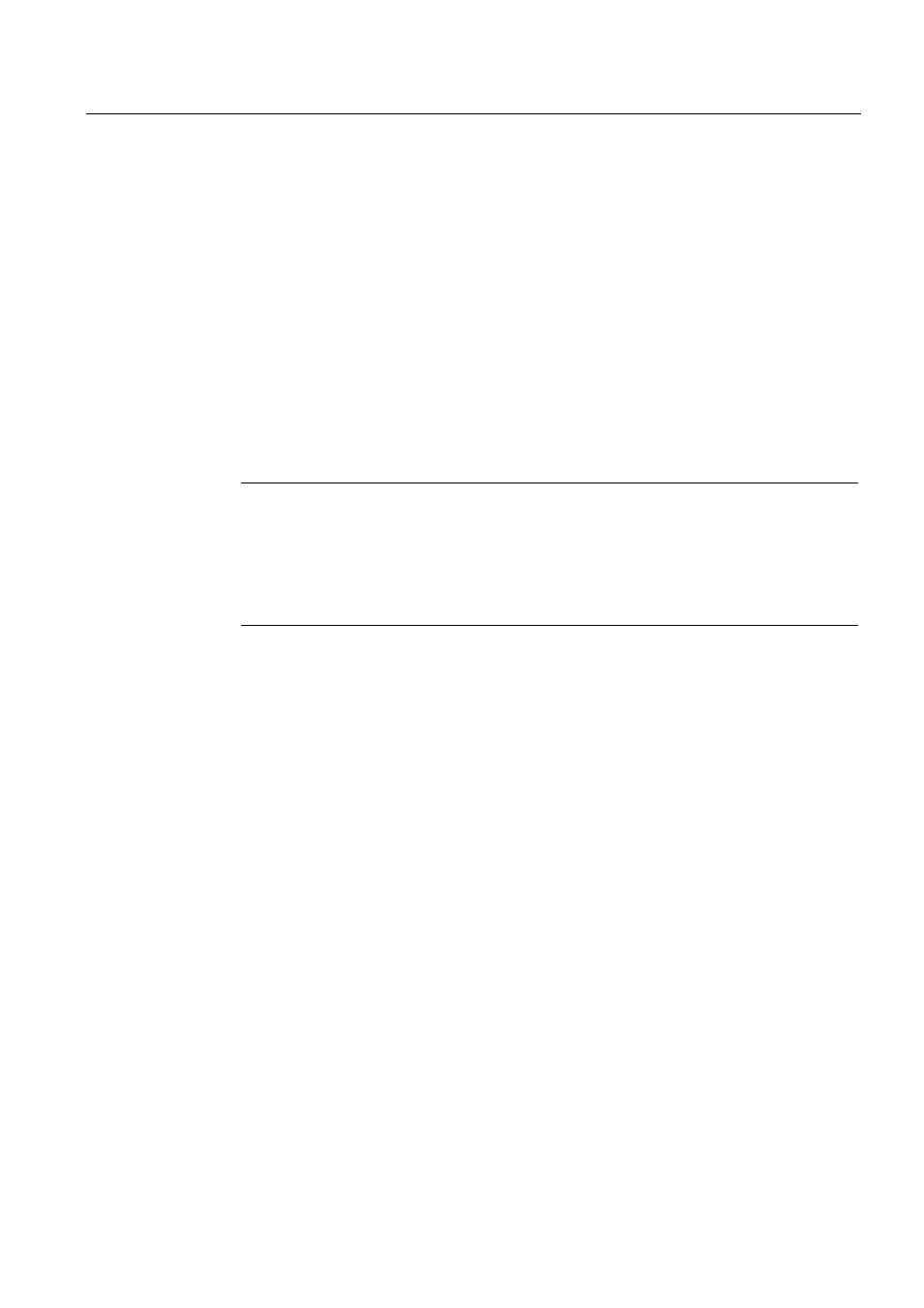
Safety Integrated basic functions
9.9 Application examples
Drive Functions
Function Manual, (FH1), 07/2007 Edition, 6SL3097-2AB00-0BP4
337
Behavior when the protective door is opened
To issue a request to open the protective door, press the S2 button ("OFF"). The drive is
brought to a standstill in accordance with stop category 1 of EN 60204-1.
● Resetting the PLC output DO 2 will trigger an SS1 at terminal X122.2 on the CU (DI 1)
and at the EP terminals of the Motor Modules. The drives are immediately braked via the
speed ramp (p1135). The speed ramp is not monitored for SS1. The pulses are safely
canceled after the safe SS1 delay time (p9852, p9652) has elapsed.
● When all drives have executed the safe pulse cancelation, the feedback "STO in group
active" (DO 10) is issued from the CU to the PLC. In addition, a request is made via the
PLC (PLC: DI 7 and DI 8) if the drives have fallen below the preset speed threshold (D0 8
and DO 9: |n| Only when these conditions are met, solenoid Y1 (PLC output DO 4) is energized and the lock of the protective door opened. ● When the protective doors are opened, the protective door safety circuit is interrupted and safety combination A2 opens its safety circuits. Note causes the lock of the protective door to open, an SS1 is initiated via S6 at terminal X122.2 (DI 1) of the Control Unit and at the EP terminals of the Motor Modules. The drives are immediately braked via the speed ramp (p1135), and the pulses canceled after the SS1 delay time has elapsed. When the protective door is opened, the "Safe Stop 1" function is safely selected. Switching on the drives The drives can be started when the protective door is shut and emergency STOP pushbutton S3 is released. The emergency STOP pushbutton S3 must be unlocked before pushbutton S1 ("ON") is actuated. With the safety combination, the ON circuit Y33, Y34 is checked for a short-circuit when terminals Y43 , Y44 are open (i.e. if Y33 and Y34 are closed before emergency stop pushbutton S3 is closed, this is identified as a fault). The Line Module must be switched on via PLC output DO 5 on the PLC by means of an edge from "0" to "1". operation". When PLC output DO 4 is reset, the coil of tumbler Y1 is no longer energized and the protective door is locked. Safety combination A2 is also ready for operation. ● By setting the PLC output DO 2, the SS1 and STO safety function is de-selected on two channels via terminal DI 1 X122.2 on the Control Unit and terminals X21.3 (EP +24 V) and X21.4 (EP M) on the Motor Modules. ● Due to a rising edge at PLC output DO1, the drives can be switched back to "operation" mode via terminal X122.1 (DI 0: OFF1).
The position of the protective door interlock is monitored by S6! If a fault on the PLC
● Once you have pressed button S1 ("ON"), safety combination A1 switches to "ready for