5 commissioning with starter – Efficient Networks Siemens Sinamics S120 User Manual
Page 244
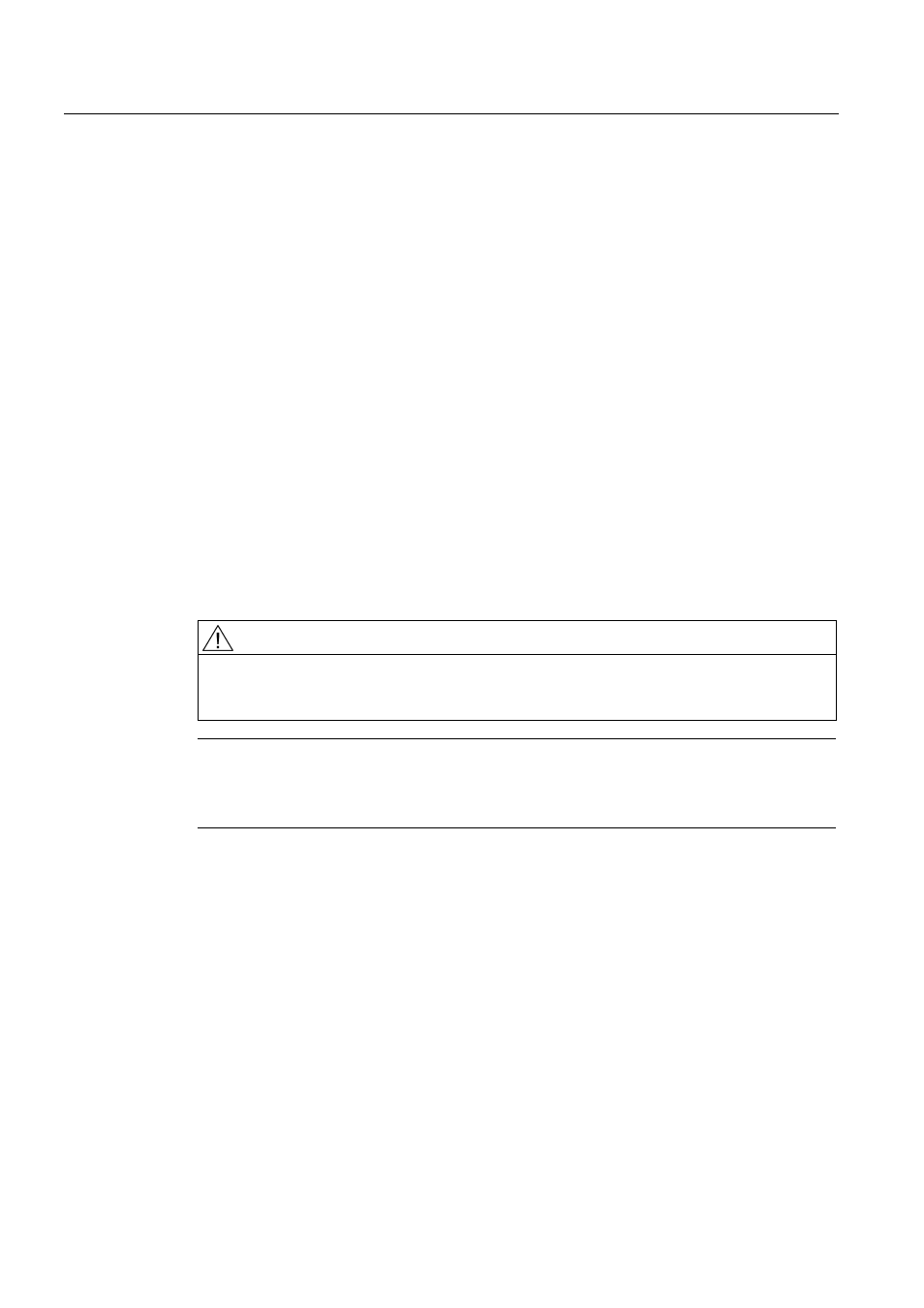
Function modules
7.8 Closed-loop position control
Drive Functions
244
Function Manual, (FH1), 07/2007 Edition, 6SL3097-2AB00-0BP4
Virtual multiturn encoder (p2721)
With a rotary absolute encoder (p0404.1 = 1) with activated position tracking (p2720.0 = 1),
p2721 can be used to enter a virtual multiturn resolution. This enables you to generate a
virtual multiturn encoder value (r2723) from a singleturn encoder. It must be possible to
display the virtual encoder range via r2723.
For rotary axes with modulo offset, the virtual multiturn resolution (p2721) is preset as p0421
and can be changed.
For linear axes, the virtual multiturn resolution (p2721) is preset with p0421 and extended by
6 bits for multiturn information (max. overflows 31 positive/negative)
If, as a result of extension of the multiturn information, the displayable area of r2723 (2
32
bit)
is exceeded, the fine resolution (p0419) must be reduced accordingly.
Tolerance window (p2722)
After switching on, the difference between the stored position and the actual position is
ascertained and, depending on the result, the following is triggered:
Difference within the tolerance window -> the position is reproduced based on the current
actual encoder value.
Difference outside the tolerance window -> an appropriate message (F07449) is output.
The tolerance window is preset to quarter of the encoder range and can be changed.
CAUTION
The position can only be reproduced if, in the powered-down state, if the encoder was
moved through less than half of the range that it can represent. For the standard EQN1325
encoder, this is 2048 revolutions or half a revolution for singleturn encoders.
Note
The ratio stamped on the gearbox type plate is often just a rounded-off value (e.g.1:7.34). If,
for a rotary axis, it is not permissible to have any long-term drift, then the actual ratio of the
gearbox teeth must be requested from the gearbox manufacturer.
Prerequisites
● CU320 with Order No. 6SL3040- ....- 0AA1 and Version C or higher or CU310
● Firmware release from FW2.5
● Absolute encoder
7.8.2.5
Commissioning with STARTER
The "position control" function module can be activated via the commissioning Wizard or the
drive configuration (configure DDS).
When the "basic positioner" function module (r0108.4 = 1) is activated, then the function
module "position control" (r0108.3) is automatically activated.