ElmoMC SimplIQ Digital Servo Drives-Bell Command Reference User Manual
Page 36
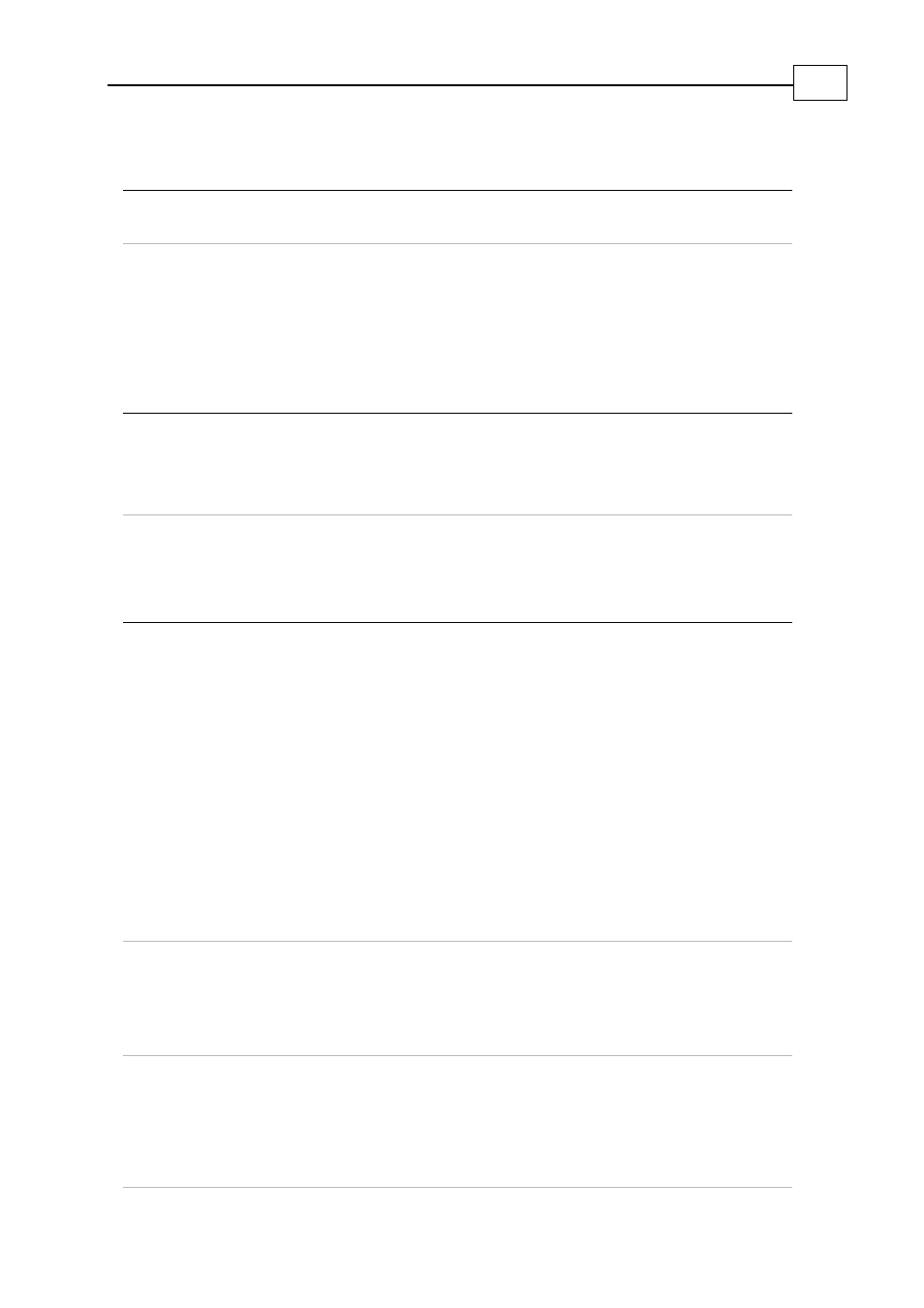
Command Description
8: Every Hall sensor transition: the exact electrical angle is locked and
commutation continues by position sensor increments.
CA[18]
Feedback bits (“counts”) per revolution, after resolution is multiplied
by 4, in the range [6…530,000,000].
For Analog Encoders, the resolution for commutation is always taken
as x2
16
, regardless of CA[31].
For Analog Hall sensors always use CA[18]=65536
For systems with Halls only, CA[18] is calculated as CA[19] * 6
CA[19]
The number of feedback counts per electrical revolution is
CA[18]/CA[19].
For brushless motors, this is the number of pole pairs.
For steppers, this is one quarter of the steps count.
Table 3-5: CA Vector - Feedback Setup Parameters
The parameters in the tables that follow are required for commutation setup.
Command Description
CA[20]
Digital Hall sensors present:
0: No digital Hall sensors are connected. If the commutation angle is
not
yet known, then at motor on a commutation search will be made.
No
digital Hall input consistency checks will be made.
1: Digital Hall sensors are connected. Upon motor on, commutation
will
be performed according to the digital Hall sensors. Continuous
encoder-based commutation will begin when the first Hall edge is
identified. The drive performs commutation checks by
continuously
comparing the encoder-derived commutation angle with the Hall
sensor recorded status.
CA[21]
Position sensor present:
0: Ignore the position sensor inputs. Commutation will be based on
the
digital Hall sensors only.
1: The position sensor will be used for commutation.
CA[22]
Main feedback type:
0-1: Reserved.
2: Quadrature incremental encoder signals.
3: Analog encoder with 1v p-p sine\cosine signal.
4: Reserved
5: Reserved
SimplIQ for Steppers Command Reference Manual
Alphabetical Listing
MAN-STECR (Ver. 1.1)
28