K i j ω – ElmoMC SimplIQ Digital Servo Drives-Bell Command Reference User Manual
Page 216
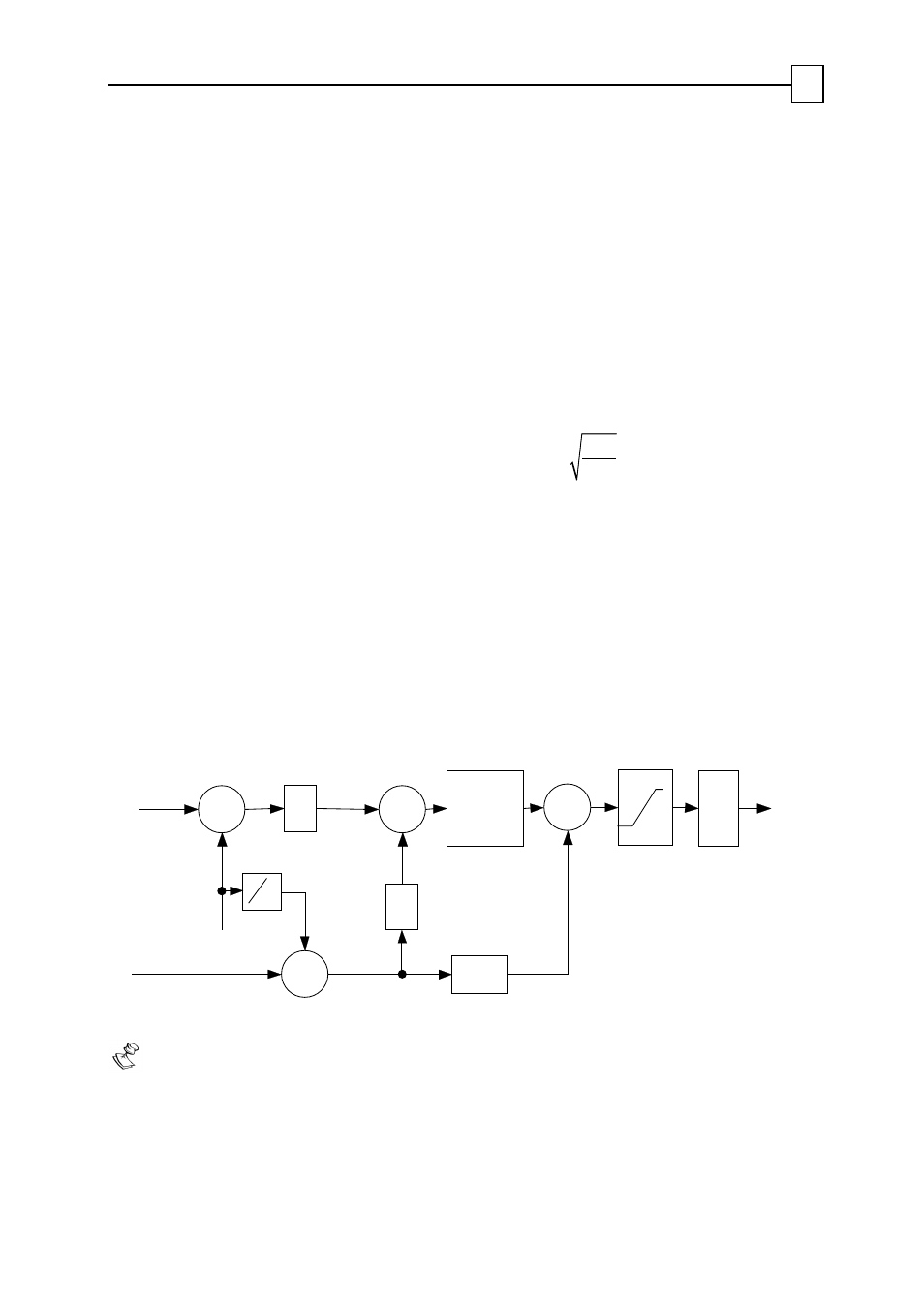
- It does not require any commutation sensor – there is no need to tune the
commutation, and there may even be flexibility or a play between the position
sensor and the motor shaft.
- The position static error is reduced to zero.
- It provides smooth motion at low speed.
Its main drawbacks are:
- Low efficiency, since the holding current exists regardless of the mechanical
output torque.
- Tendency to oscillate if the closed loop controller is tuned to low bandwidth. The
stepper torque is proportional to the position error, so that it generates a
harmonic oscillator with the natural frequency of
T
r
K I
J
ω =
. Here
T
K
is the
motor torque sensitivity, I is the current, J is the motor and load inertia, reflected
to the motor. When tuned to high bandwidth (this requires a good quality
position sensor and no play), the stepper’s natural resonance is almost completely
eliminated.
- When the acceleration limits are not set correctly (PF[29]), the stepper stalls. This
means that it no longer generates DC torque or power – it simply vibrates in
place.
The position controller structure is depicted below.
ˆ
P
K
ˆ
I
K
Σ
Position
command
[counts]
Position
feedback
Σ
Speed
command
[counts/sec]
d
dt
-
-
Σ
High
order
filter
Σ
FF(2)
Speed &
Acceleration
limit PF[29]
K1
Electrical
angle, rev.
• The parameter KF[29] tunes the acceleration limiter, which prevents the controller from
demanding too great accelerations, as too great accelerations may cause a stepper to
stall. This parameter sets the ratio between the current level in [A] and the permitted
drive acceleration in encoder counts/sec
2
.
SimplIQ for Steppers Application Note
Unit Modes
MAN-STECR (Ver. 1.1)
17