Symptom cause remedy – INFICON STC-2000A Thin Film Deposition Controller Operating Manual User Manual
Page 274
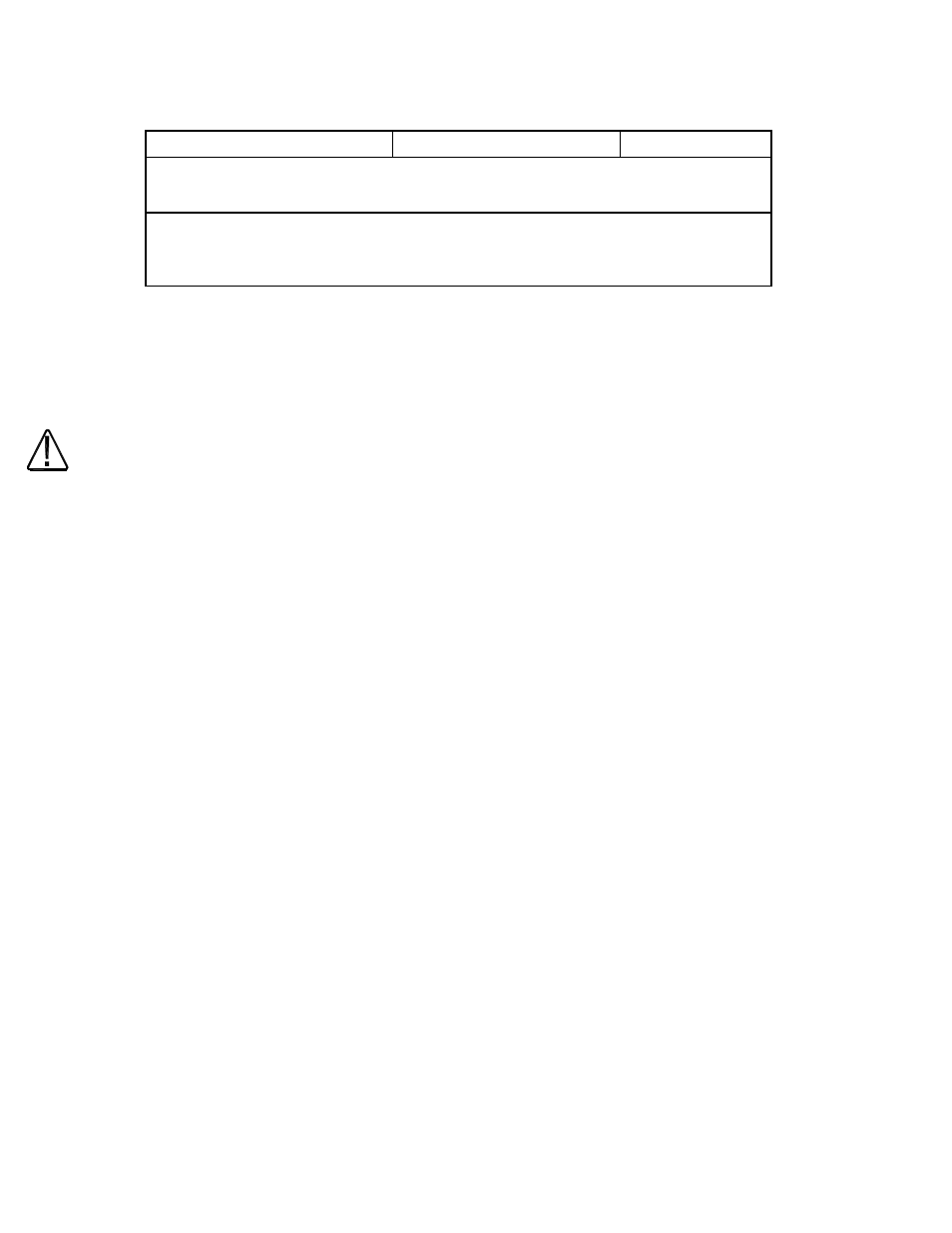
p
STC-2000A DEPOSITION CONTROLLER
y
SYMPTOM CAUSE REMEDY
6. Poor thickness reproducibility
a. Poor source emission pattern
Move sensor.
Check source.
b. Material adhesion to sensor poor New crystal.
7. Computer interface failure
a. Baud rate wrong
Correct configure.
b. Format wrong
Correct configure.
c. Device address wrong
Correct configure.
d. Cable connection bad
Check wiring.
SECTION 8.1
Replacing A Sensor Crystal
The procedure for replacing the 6 MHz sensor crystal is the same for any type sensor head. Use
caution in handling the crystals as they are very fragile. Chipped, cracked, dirty or stained crystals should
not be used.
CAUTION
Crystals should never be handled with bare hands! Always use clean lab gloves
and plastic tweezers to handle a crystal. This will avoid surface contamination of the crystal that
might lead to poor electrical surface contact and possible poor film adhesion.
Dielectric films sometimes do not adhere strongly to the crystal surface and can cause erratic
readings. Some dielectric will peel off the crystal when it is exposed to air. This is caused by gas absorption
greatly changing the film stress characteristics. If peeling is observed, change to a new clean crystal.
Follow the procedures outlined below to change a sensor crystal.
1.
Grip the sensor cap with a gloved hand and pull to unsnap the cap. The sensor crystal is captured
in the cap. Place the sensor cap on a flat surface with the front face up and pop the crystal out by
pressing gently down on the coated crystal surface with clean plastic tweezers or a similar type
instrument. The crystal should come out easily. Take care not to damage the cap aperture opening
to the crystal. Turn the cap over and place a new crystal with the fully coated surface towards the
aperture opening (this side receives the evaporate stream) in the sensor cap. Use plastic tweezers
to handle the new crystal.
2.
Gently press the crystal into the finger spring holders using the plastic tweezers. This operation
does not require much force. The crystal movement to become held by the finger springs is only
about 25 thousandths of an inch. The sensor cap now holds the sensor crystal firmly in place. The
cap may now be snapped into the sensor body.
3.
Verify that the newly installed crystal is operating by looking at the STC-2000A "XTAL x
XX%" indicator legend in the upper left of the LCD display. The XTAL x XX% should report
some percentage of crystal life. If the "XTAL x BAD" legend is present check for damaged
cables, a cracked or broken crystal, or dirty contact surfaces in the sensor cap.
SECTION 8.2
Persistent Crystal Fail Indication
If you have replaced the sensing crystal and the XTAL x BAD indication persists, the problem can
either be in the electronics of the STC-2000A or in the sensing head or the cabling and connections to the
sensing head. Historically most problems have been found to be somewhere in the electrical connection
path. Many mechanical electrical connections exist between the sensing crystal and the oscillator unit and
it is therefore sometimes difficult to locate this problem. Remote oscillators have a test feature to help
isolate this type of problem, refer to Figure 8.3. A test push-button is provided on the oscillator. This
button connects an internal test crystal located inside the remote oscillator in place of the normal sensing
head. (By pressing this switch, the electrical path to the sensor from the oscillator is broken and a fixed
5.500MHz crystal inside of the OSC-100 is substituted.) If the STC-2000A and remote oscillator are
functioning correctly the bad crystal indication will go away and the crystal life indication on the STC-
SECTION 8.XX
page 274 of 292