2 p a ra met e rs – HEIDENHAIN MANUALplus 4110 User Manual
Page 436
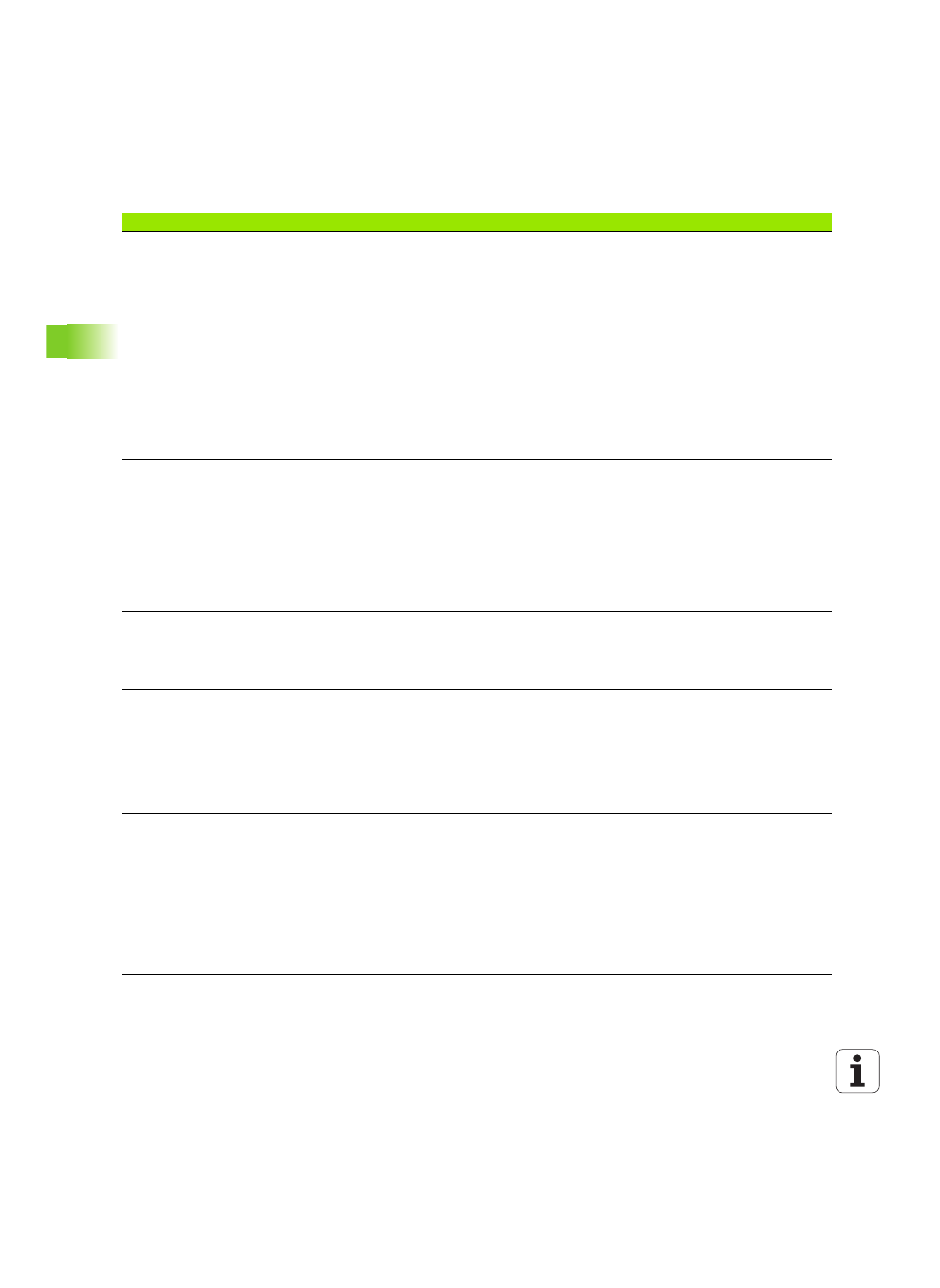
436
8 Organization Mode of Operation
8.2 P
a
ra
met
e
rs
Display setting [MP 17]
The data is displayed in the "Actual value display" fields (machine
window).
Actual display type—the numbers have the following meaning:
0: Actual value
1: Following error
2: Distance of traverse
3: Tool tip—referenced to machine zero point
4: Slide position
5: Distance between reference cams / reference pulse
6: Nominal position
7: Difference between tool tip / slide position
8: Nominal IPO position
Control configuration [MP 18]
PLC is to perform counting of workpieces:
0 = not active
1 = active
M0/M1 for all NC channels—configuration parameter
Interpreter stop during tool change
0 = not active
1 = active—look-ahead block interpretation is interrupted and
only resumed after execution of the G14 function.
Option code 1—configuration parameter
Feed rates [MP 204]
Rapid traverse contouring speed for manual control
Feed rate contouring speed for manual control (usually set with
"Set T, S, F")
Feed per revolution for manual control
Thread cutting [MP 208]
The coupling/decoupling path is used if the corresponding
parameters are not programmed in the DIN program.
Coupling path [mm]
Acceleration path at the beginning of a threading cut in order to
synchronize the feed axis with the rotary axis.
Decoupling path [mm]
Deceleration path at the end of the threading cut.
Position of the touch probe or optical gauge
[MP 211]
To define the position of the probe, enter its external coordinates.
To define the position of the optical measuring system, enter the
position of the cross hairs.
Reference: Machine zero point
Position of touch probe/optical gauge in +X
Position of touch probe in –X
Position of touch probe/optical gauge in +Z
Position of touch probe in –Z
Machine parameters (MP)