Wcc ii operator’s guide, System overview – WattMaster WCC II User Manual
Page 9
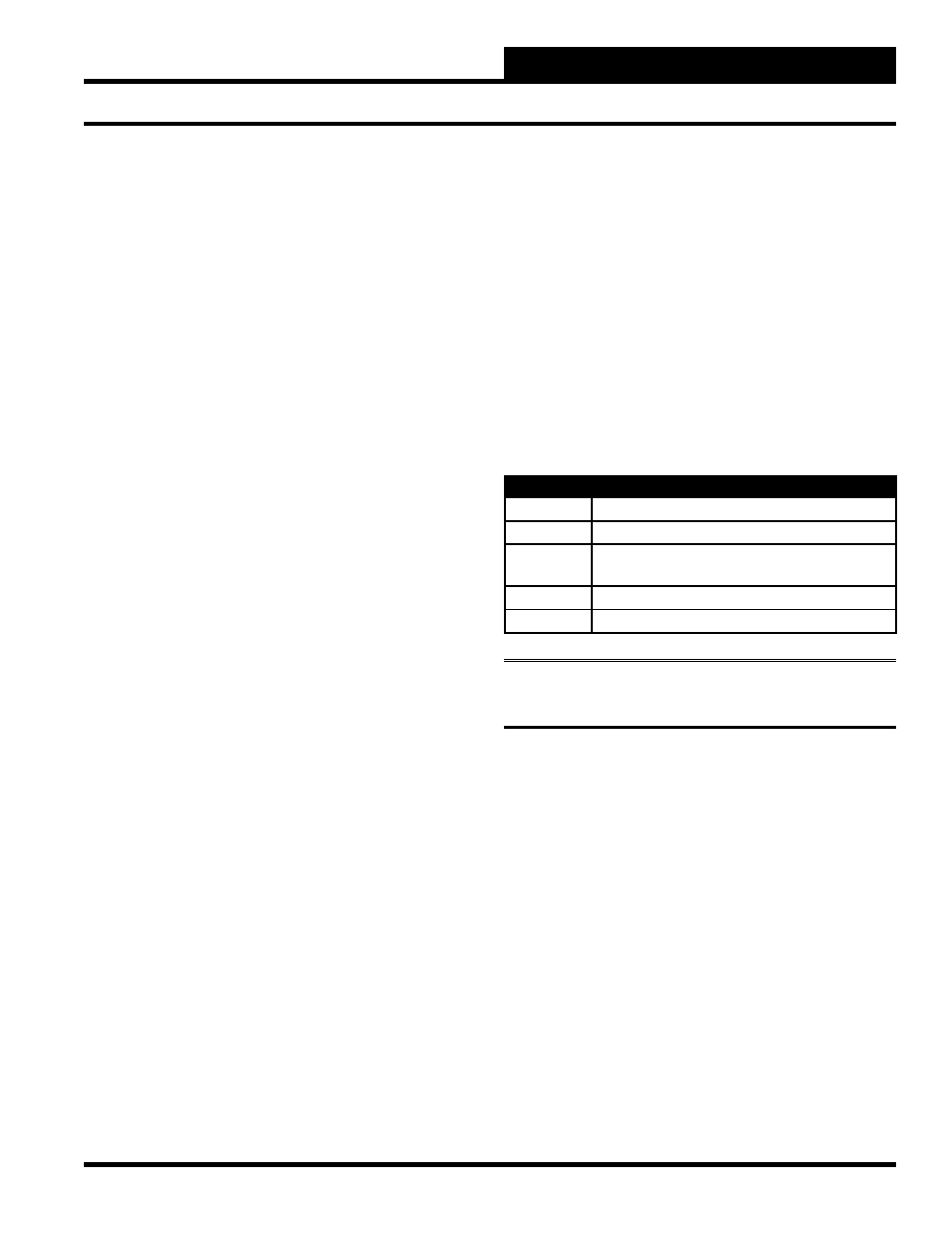
WCC II Operator’s Guide
Operator Interfaces
I-3
System Overview
SAT II
Sensors and relays etc. are wired to the SAT II controller to allow
it to monitor and control loads directly. Each SAT II controller can
handle the following number of inputs and outputs:
8 analog or binary inputs
16 additional binary inputs
- 1 binary input board receives 8 binary inputs
- 2 binary input boards may be used with one
SAT II
8 analog outputs (0-15 VDC maximum range)
- 1 DAC module enables 4 analog outputs
- 2 DAC modules may be installed in SAT II
- Any or all of the 8 analog outputs may be
converted to binary outputs using 1 V-Out
to Binary board
- 1 chip switch is required for each binary
output
16 binary outputs
- 1 chip switch is required for each binary
output
SAT II-A
The SAT II-A is a version of the satellite controller that allows the
ECC/WCC II front end computer to communicate with remote
mounted Terminal Unit Controllers.
The Terminal Unit Controller (TUC) is a microprocessor based
device which can be used to control terminal units such as pressure
dependent variable air volume (VAV) boxes, pressure dependent
fan power boxes, fan coil units, heat pumps etc. The TUC can be
used as a stand-alone controller, or the TUC can be used with the
ECC/WCC II system.
The TUC accepts an input from a room temperature sensor to allow
it to monitor the space temperature and when used with the SA
(Stepper Actuator) actuator, provides pressure dependent control
of the primary air damper on terminal units such as variable air
volume boxes, constant fan power induction units, and intermittent
fan power induction units. The SA Actuator is not an integral
part of the TUC and must be ordered and purchased separately.
The TUC can also have three relay outputs to provide control of
the fan and fi rst and second stages of heat on fan terminal units,
or to control the fan, compressor, and reversing valve on a heat
pump. The TUC can also provide an output to control two 24 VDC
solenoid air valves to obtain “feed” and “bleed” type control of
pneumatic controlled devices. The TUC is generally mounted at
the terminal unit (i.e. VAV box, heat pump, etc.).
•
•
•
•
When the TUC’s are to be used with the ECC/WCC II system,
a type SAT II-A satellite controller is required as the interface
between the Central Processing Unit (CPU) and the Terminal Unit
Controller (TUC). The SAT II-A is a special version of the satellite
controller, and its only purpose is to interface with the TUC’s. Up
to 32 TUC’s can be connected to one SAT II-A using a 3-wire,
shielded cable. The TUC’s are wired to the SAT II-A in a “daisy
chain” arrangement. That is to say, the 3-wire cable does not have
to be run from each TUC back to the SAT II-A. The 3-wire cable
is run from the SAT II-1 to the nearest TUC and the 3-wire cable is
extended from that TUC to the next.
TUC Input/Output Features
The fi ve versions of the pressure dependent TUC are shown in the
table that follows:
Model
TUC Description
TUC-R
3 Relays with 2 amp, 24 Volt SPDT Contacts
TUC-A
Stepper Motor Actuator Output
TUC-AR
Stepper Motor Actuator Output & 3-24 Volt
SPDT Relays
TUC-P
Pneumatic Output
TUC-PR
Pneumatic Output & 3-24 Volt SPDT Relays
Note:
The SA actuator and solenoid air valves must be
ordered and purchased separately.
SAT II-B
The SAT II-B is similar to the SAT II-A, only the SAT II-B
communicates with up to 32 TUC-VR’s.
The TUC-VR is a velocity resetting (pressure independent)
controller for use with variable air volume (VAV) terminal units.
The TUC-VR mounts on the VAV box and communicates with
the front end ECC/WCC II through a SAT II-B. The TUC-VR
provides precise direct digital control of the following types of
VAV terminal units:
1-Cooling Only
2-Cooling/Staged Electric Reheat
3-Cooling/Time Proportioning Electric Reheat
4-Cooling Proportional Reheat Valve
5-Parallel Fan Powered/No Reheat
6-Parallel Fan Powered/Staged Electric Reheat