Shunt calibration – Measurement Computing DBK Part 2 User Manual
Page 58
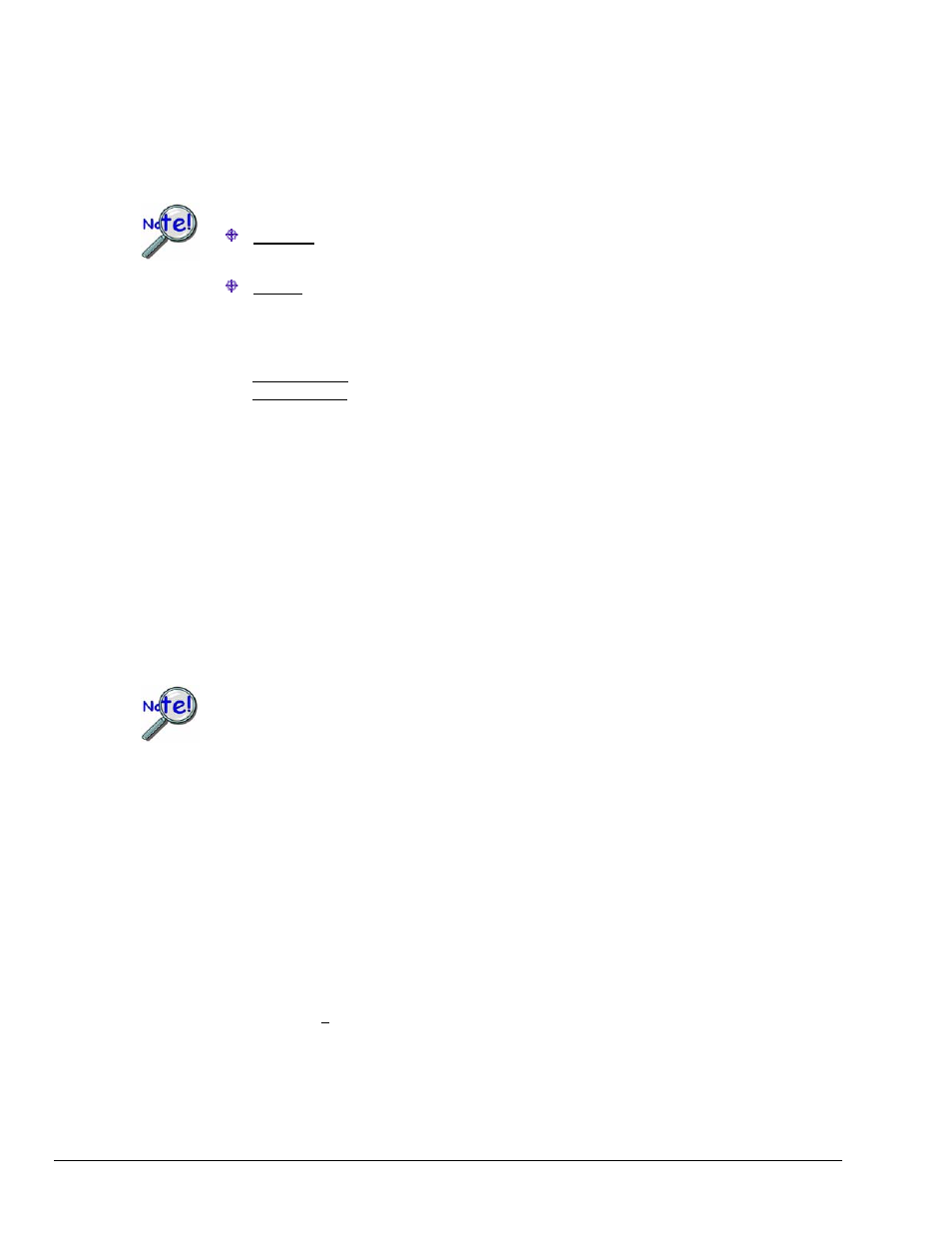
DBK43A & DBK43B, pg. 38
899892
DBK Option Cards and Modules
Shunt Calibration
Shunt calibration is virtually identical to the 2-Point method just discussed, except that the second point is
simulated. The simulated load is achieved by shunting one leg of the bridge with a shunt resistor. Shunt
calibration is the preferred calibration method when applying a real load (of a value approximating the
maximum expected load) is not practical. To adjust the channel gain, the shunt must be applied to the
bridge.
Calculate and install the necessary shunt resistor before continuing.
DBK43A has direct support for shunt calibration, accommodating the
resistor in its enclosure and allowing the software to apply it when requested.
DBK16 does not have direct support, so the shunt resistor must be applied
externally and switched in manually.
Adjust the Offset
1. DBK43A users: Verify that the unit’s physical switch is in the NORM position.
DBK43B users: Verify that the unit’s physical CAL1 and CAL2 switches are both in the
RUN position.
2. In the Param1 column, select all of the DBK43A [or DBK43B] channels that are to be
adjusted.
3. Select Mode = Bridge from the drop down list above the grid. This selection commands the
calibration multiplexer to route the transducer voltage through the analog path.
4. Turn off all the channels in the system except for those DBK43A [or DBK43B] channels that
are to be adjusted.
5. Click the Download button to send the current configuration to the LogBook.
6. Select Indicators \ Enable Input Reading Column from the menu bar to display the offset
values for each channel.
7. For the associated channel, apply the first calibrated load to each gage (typically no-load) and
set the voltage to 0.0V for each transducer by adjusting the trimpot labeled OFFSET.
If the first point is an actual calibrated load, you must move the load to each gage, one at a
time, to adjust its associated offset.
Adjust the Input and Scale Amplifier Gain
For the best results, a gain should be selected so that the bridge’s maximum output equals 90% of the
A/D’s input range.
1. Use the following equation to calculate the desired shunt voltage (V
D
).
V
D
= (L
s
/L
M
) * V
I
* 90%
Where:
V
D
= Desired voltage from the after amplification when the shunt is applied
L
s
= Simulated load produced by shunt
L
M
= Maximum load expected during usage
V
I
= Input voltage range
Example:
The simulated load produced by the shunt 100lbs. The maximum expected load during
usage is 150 lbs. The programmable input range of the data acquisition system is set
for +5V. The desired output voltage of the strain gage signal conditioning electronics
is:
V
D
= (100/150) * 5 * 0.90 = 3V
In this example, we would adjust the GAIN and SCALE trimpots until a value of 3V
is measured. If 150lbs is applied to the gage, a voltage of 4.5V will be measured.
V
D
= (150/150) * 5 * 0.90 = 4.5V