Measurement Computing DBK Part 2 User Manual
Page 36
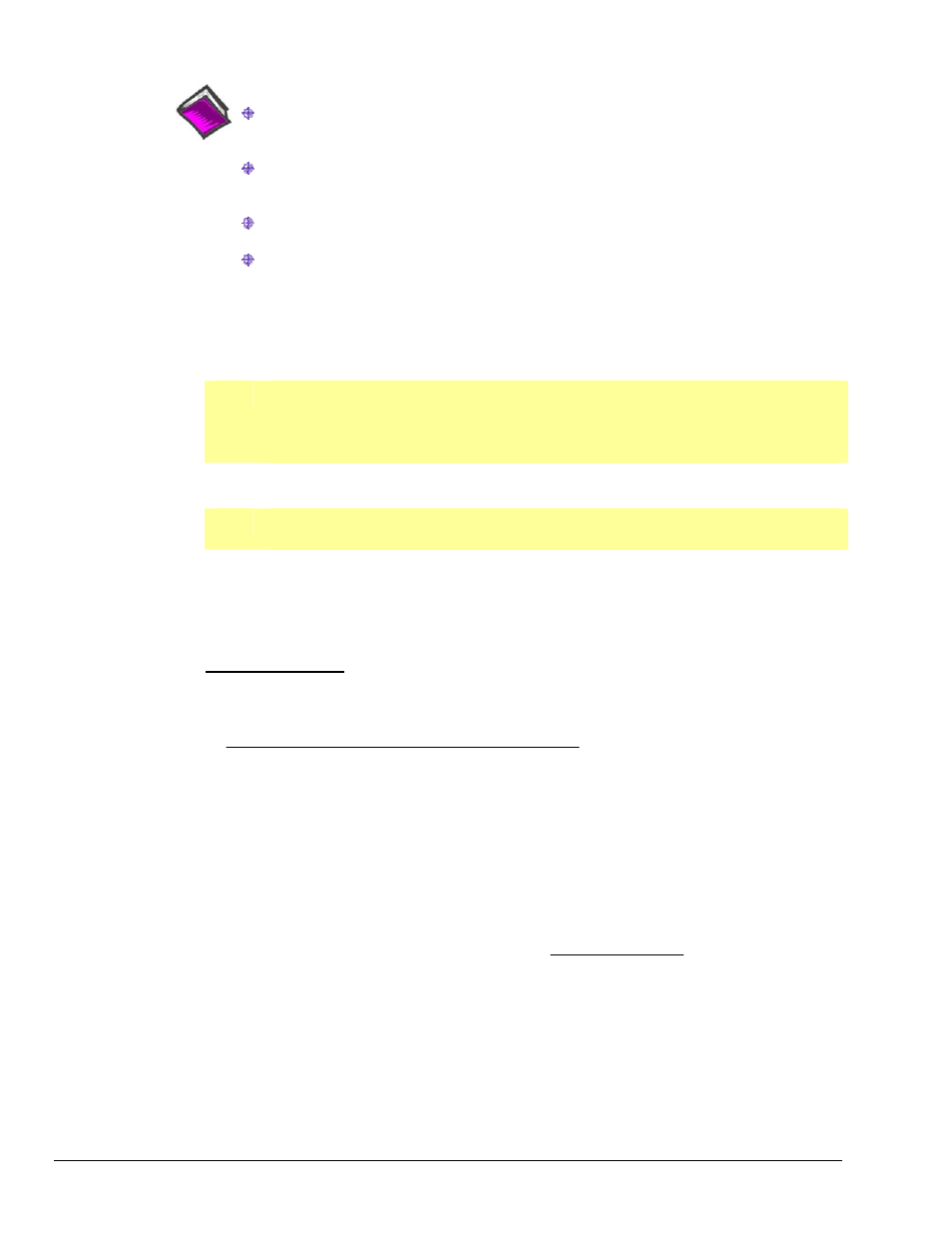
DBK43A & DBK43B, pg. 16
899892
DBK Option Cards and Modules
A Typical Setup Procedure, with Embedded Examples
Reference Notes:
Prior to using DBK43A or DBK43B with DaqView, you must select the module from
DaqView’s Configure Hardware Settings screen. If needed, refer to Chapter 3, DBK
Setup in DaqView.
Prior to using DBK43A or DBK43B with LogView, you must select the module from
LogView’s Hardware Configuration screen. If needed, refer to Chapter 4, DBK Setup in
LogView.
The board layouts in this DBK section can be referred to for jumper locations, jumper
setting orientations, and trimpot locations.
For Calibration – DaqView users should refer to the GageCal segment beginning on page
21 of this section. LogView users should refer to the section titled Calibrating DBK16,
DBK43A, and DBK43B for LogBook Applications, beginning on page 25.
1. Verify that the low-pass filters are set to BYPASS. The filters are set via jumpers JPn04 where n is
the channel number (1 through 8); for example, JP104 sets the filter for channel 1, and JP804 sets the
filter for channel 8.
Note: If you plan to use filters during your acquisition, you should still select BYPASS at this
point. Enabling the filters comes into play later in the procedure. However, if you do plan
to enable filters, note the gain in the filter stage (default ×2, or ×1 with resistor removed)
and allow for it in your setup.
2. Coupling is set via jumpers JPn03 where n is the channel number (1 through 8). Verify that the
“Coupling” jumpers are installed. When installed, the channels are set for DC coupling.
Note: If you plan to use AC Coupling during your acquisition, you should still select DC
Coupling at this point. Selecting AC Coupling comes into play later in the procedure.
3. Determine the excitation for the transducer. This is based on the transducer specifications and from
the current limitations of the DBK43 module’s excitation regulator.
4. Determine the maximum voltage that can result from the transducer for a strain gage or for a load
cell. The values can be calculated as follows:
Strain Gage Example
Most strain gages come with Gage Factors (GF). To calculate the approximate output of the bridge
circuit with a typical strain value, use the formula:
(
)
Excitation Voltage)(Gage Factor)(Strain in strain units
*Bridge circuit output voltage
4
=
In this strain gage example, lets assume the following:
• We have a 120 ohm strain gage.
• The gage factor is 2.1.
• The excitation voltage is 5 V. This is due to the current limitation of the excitation regulator
on the DBK43 module [note that the excitation voltage must be less than 6 V]
• We are measuring 4000 micro-strain
By applying these values to the preceding equation we find that the bridge output voltage is 10.5 mV.
Bridge output voltage for 4000 microstrain =
(5)(2.1)(4000 10 )
4
10.5 mV
-6
×
=
*linear estimate (some strain gages are not linear); refer to strain-gage theory for more information.