IAI America MSCON User Manual
Page 300
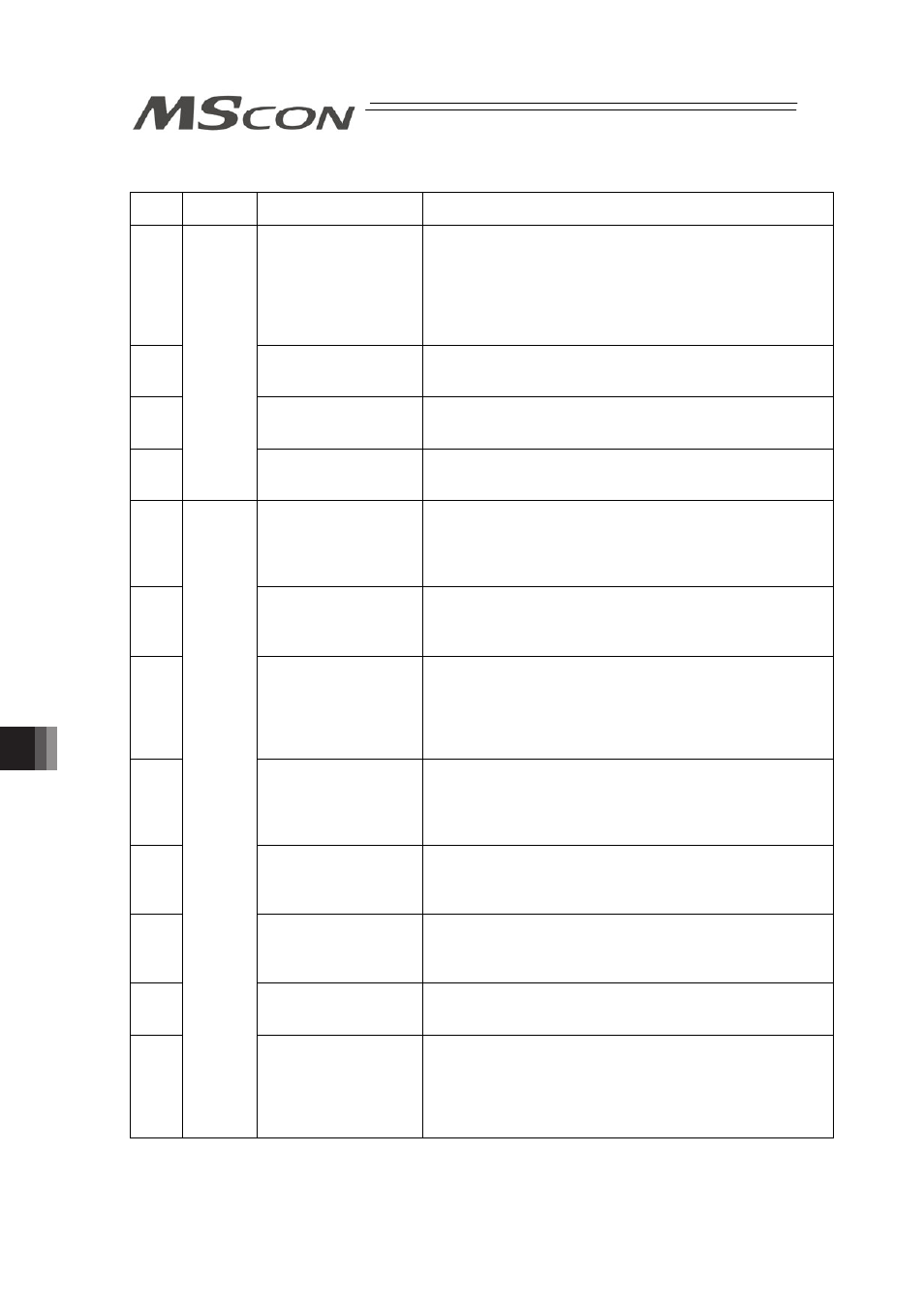
Chapter 8
Troubleshooting
292
[3] Alarm List
Alarm
Code
Alarm
Level
Alarm Name
Cause/Treatment
048
Driver overload alarm
Cause
: The load current exceeded the value set in
Parameter No.143 “Overload Level Ratio”.
This alarm is kept alarm condition until reset is
made. This alarm turns ON when the load current
exceeds the setting from a value below the setting.
Treatment : Lower the setting of acceleration/deceleration. Also,
increase the frequency of pause.
04E
Exceeded movement
count threshold
Cause
: The total number of the operation times exceeded
the value set in Parameter No.147 “Total Movement
Count Threshold”.
04F
Exceeded operated
distance threshold
Cause
: The total number of the operation distance
exceeded the value set in Parameter No.148 “Total
Operated Distance Threshold”.
06B
Message
Maintenance
information data error
Cause
: The maintenance information (total movement
count, total operated distance) is lost.
Treatment : Please contact IAI.
080
Move command in servo
OFF
Cause
: A move command was issued when the servo is
OFF.
Treatment : Issue a movement command after confirming the
servo is ON (servo ON signal SV or position
complete signal PEND is ON).
082
Position Command in
incomplete home return
Cause
: A position move command was issued before home
return was completed.
Treatment : Issue a command after confirming that home return
has been completed HEND is ON.
083
Numerical command in
incomplete home return
Cause
: An absolute position command was issued by
numerical specification before home return was
completed (direct command from Field Network).
Treatment : Issue a numeric specification after performing home
return operation and confirming the complete signal
HEND.
084
Movement command
during home return
operation
Cause
: A move command was issued when home return
was still in progress.
Treatment : Issue a movement command after performing home
return operation and confirming the complete signal
HEND.
085
Position No. error during
movement
Cause
: A non-existing (invalid) position number was
specified in the positioner mode.
Treatment : Check the position table again and indicate an
effective position number.
090
Software reset during
servo ON
Cause
: A software reset command was issued when the
servo was ON.
Treatment : Issue a software reset command after confirming
that the servo is OFF (SV signal is 0).
091
Position No. error in
teaching
Cause
: The position number out of the available range was
selected in the teaching.
Treatment : Select the position number from 63 or smaller.
092
Operation
release
PWRT signal detection
during movement
Cause
: The current position write signal PWRT was input in
the teaching mode of PIO pattern 1 while the
actuator was jogging.
Treatment : Input the PWRT signal after confirming that the job
button is not pressed and the actuator is stopped
(MOVE output signal is OFF).