Cross cutter, Features of the "cross cutter" prepared solution – Lenze EVS93xx CrossCutter User Manual
Page 30
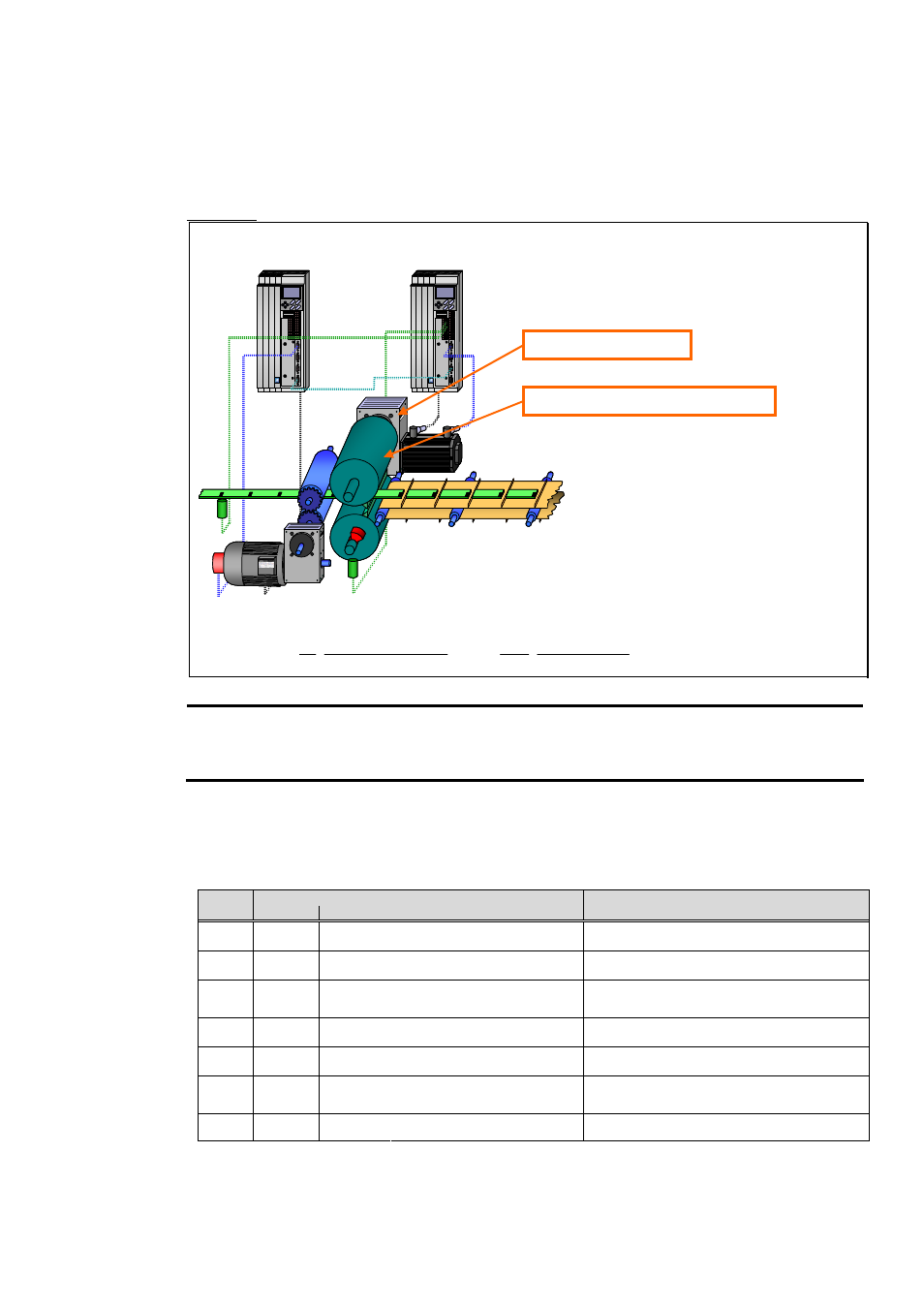
Cross Cutter
Features of the "Cross Cutter" prepared solution
Prepared Solution Servo PLC / ECSxA 1.1 EN
2-16
Example:
A position s[units] = 165° needs to be converted into an incremental value. For this example, the
characteristics of the mechanical system are as follows:
L
L
L
L
L
L
[incr.]
438640
]
/
[
360
]
/
.
[
65536
189
2760
]
[
165
]
/
[
]
/
.
[
65536
]
[
.]
[
nt
FeedConsta
=
°
⋅
⋅
°
=
⋅
⋅
=
rev
rev
incr
rev
units
m
rev
incr
N
Z
units
s
incr
s
i
i
TIP!
If you are using the parameterisable variant of the Cross Cutter prepared solution, values in
application units will be converted into incremental values automatically.
The machine parameters can be read from the following display codes using a parameter
setting tool (e.g. GDC or DDS). The machine parameters are set using the
CamManager/CamDesigner software tool (see Chapter 3.4.2). The values displayed in the
codes are read from the profile data associated with the relevant controller (LC9 file):
Possible settings:
Code
Default
Selection
Comments
C3303
-
0 …
{1}
... 65535 Display code: Gearbox ratio in master value phase
(numerator)
C3304
-
0 …
{1}
... 65535 Display code: Gearbox ratio in master value phase
(denominator)
C3305
- 0.0000...
{0.0001
[m_units]/r
ev}
... 214748.0000 Display code: Feed constant in master value phase in
application units per gearbox revolution
C3306
-
0 …
{1}
... 65535 Display code: Gearbox ratio in cross-cutter train
(numerator)
C3307
-
0 …
{1}
... 65535 Display code: Gearbox ratio in cross-cutter train
(denominator)
C3308
- 0.0000...
{0.0001
[m_units]/r
ev}
... 214748.0000 Display code: Feed constant in cross-cutter train in
application units per gearbox revolution
0:
Direct
C3636
0
1:
Inverted
Possible setting for motor mounting position
Feed constant = 360°/rev
Gearbox i = 2760 : 189