Introduction, Standard features and benefits – Watlow EZ-ZONE RMC User Manual
Page 8
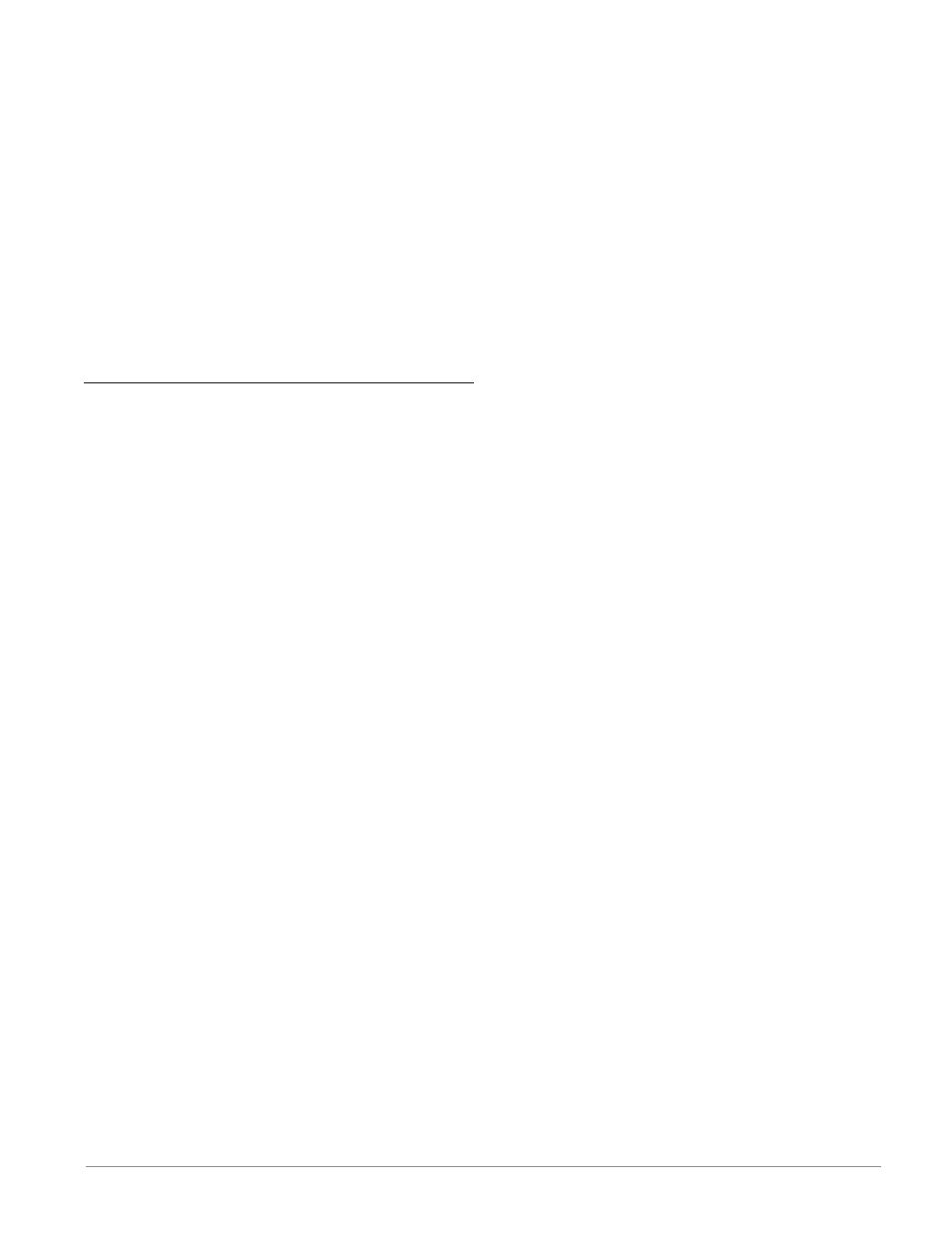
Watlow EZ-ZONE
®
RMC Module
•
5
•
Chapter 1 Overview
Introduction
The EZ-ZONE
®
Rail Mount Control module (RMC)
takes the pain out of solving your thermal loop re-
quirements whether it be for a single loop, multi-loop,
stand-alone or distributed control applications.
It just got a whole lot easier to solve the thermal
requirements of your system. The RMC module is
provided in a space-saving, rail-mount package and
is highly scalable where you only pay for what you
need. For those applications that require the ability
to configure/monitor the control over a network, Mod-
bus RTU communications is an option. Other commu-
nications protocols are also available (e.g., EtherNet/
IP, DeviceNet, Modbus TCP and Profibus DP) when
used in conjunction with an RM Access (RMA) mod-
ule or when using a Remote User Interface/ Gateway
(RUI/GTW).
Standard Features and Benefits
Integrated PID and over/under safety limit con-
troller in one package
• Provides two mounting options (DIN rail, chassis
mount)
• Reduces wiring time and termination complexity
compared to connecting discrete products
• Reduces panel space and installation cost
• Increases user and equipment safety for over/under
temperature conditions
Integrated power controller output
• Includes the patented NO-ARC, which drives up to
15 amp resistive loads directly
• Reduces component count and cost of ownership
• Saves panel space and simplifies wiring
Current monitoring (traditional or algorithm)
• Detects heater current flow and provides alarm
indication of a failed output device or heater load
• For use in single phase loads
Communication Capabilities
• Supports network connectivity to a PC or PLC
• Watlow Standard Bus or Modbus
®
RTU
• Provides plug and play capabilities with Remote
User Interface (RUI’s) and RMA module
• Free standard bus communications port and free
PC software (EZ-ZONE Configurator)
Additional Control Integration Options
• Provides a sequencer function
• Includes programmable timer functions
• Includes programmable counter functions
• Allows for simple math and logic programming op-
tions
Advanced PID Control Algorithm
• Offers TRU-TUNE
®
+ adaptive control to provide
tighter control for demanding applications
• Provides auto-tune for fast, efficient startup
Integrated Thermal Loop Diagnostics
• Users can easily tell that the entire thermal sys-
tem is functioning properly
• Provides complete system diagnostics that are far
superior to simple discrete level diagnostics
• Allows for flexible synergistic use of hardware,
such as using one loop's sensor as a backup to an-
other loop in the event of sensor failure.
• Helps prevent load loss or allow for maintenance to
be scheduled when more convenient.
• Provides notification of system problems to help
reduce maintenance and service costs
Off-the-Shelf Designed System Solution
• Improves system reliability with a factory integrat-
ed solution that minimizes inter-module connec-
tions and potential problems at screw termination
points.
• Reduces installation cost
• Eliminates compatibility headaches often encoun-
tered with using many different components and
brands
Controller Handles High Ambient Tempera-
tures
• Operates in an unprecedented temperature range
of -18 to 65°C (0 to 149°F) for cabinets and panel
enclosures with elevated temperature levels
Memory for Saving and Restoring User-Defined
Parameter Default Settings
• Allows customers to save and restore their own de-
fined defaults for machine parameter settings
• Reduces service calls and downtime due to inad-
vertent end user parameter adjustments
RMC Modules Allow for Greater Design Flex-
ibility
• Allows PID loops to be added in increments of one.
• Saves money because you do not pay for any more
than you need and don’t settle for any less func-
tionality than you need
Synergistic Module Control (SMC)
• Allows outputs selected for control (heat/cool),
alarms or events to be located in any physical mod-
ule, regardless of which module is connected to the
input sensor