Control methods, Retransmitting a process value or set point, Cool output curve – Watlow EZ-ZONE RMC User Manual
Page 161: Output configuration, Auto (closed loop) and manual (open loop) control
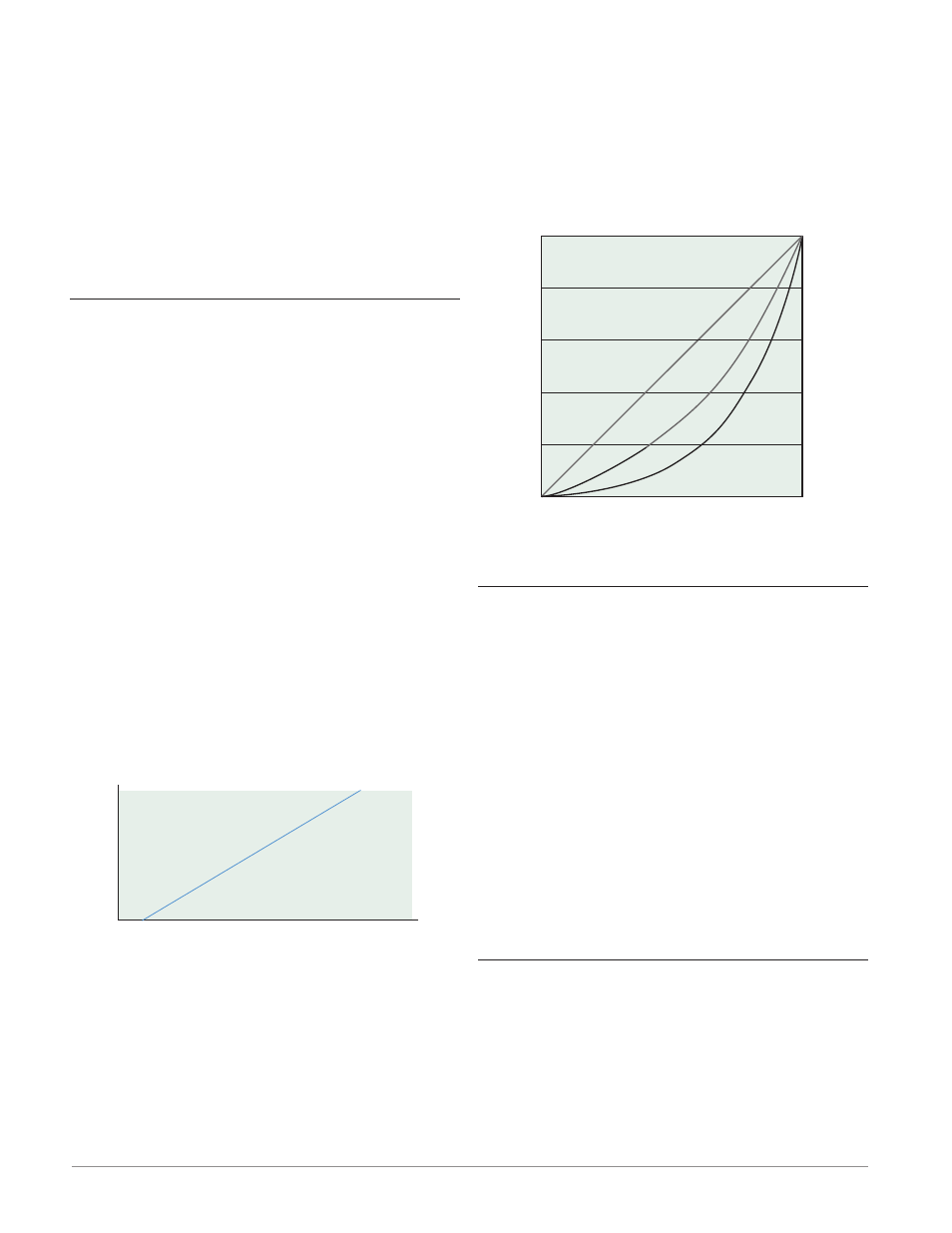
Watlow EZ-ZONE
®
RMC Module
•
158
•
Chapter 7 Features
• DC loads with hybrid relays. The triacs used for
arc suppression will turn off only with ac line
voltage;
• Hybrid switches to drive any inductive loads,
such as relay coils, transformers or solenoids;
• Cycle times less than five seconds on hybrid
switches;
• On loads that exceed 264V ac through relay;
• On loads that exceed 15 amperes load;
• On loads less than 100 mA;
• NO-ARC relays in series with other BO-ARC re-
lays.
Retransmitting a Process Value or Set Point
The retransmit feature allows a process output to
provide an analog signal that represents the set point
or process value. The signal may serve as a remote
set point for another controller or as an input for a
chart recorder documenting system performance over
time.
In choosing the type of retransmit signal the op-
erator must take into account the input impedance
of the device to be retransmitted to and the required
signal type, either voltage or milliamperes.
Typically, applications might use the retransmit
option to record one of the variables with a chart re-
corder or to generate a set point for other controls in
a multi-zone application.
Outputs 1, 3, 5 and 7 can be ordered as process
outputs. Assign an analog source to Output Func-
tion to accomplish retransmit of a process or set point
value.
Note:
The active set point is not retransmitted, only the
user requested closed loop set point which may not be
the closed loop set point in control. Retransmitting a
profiling closed loop set point is not allowed.
Retransmit
Retransmit Source
Output Scale
Range High
Range Low
Scale High
Scale Low
Set the range of the process output with Scale
Low [`S;Lo] and Scale High [`S;hi]. Scale the re-
transmit source to the process output with Range
Low [`r;Lo] and Range High [`r;hi].
When the retransmit source is at the Range Low
value, the retransmit output will be at its Scale Low
value. When the retransmit source is at the Range
High value, the retransmit output will be at its Scale
High value.
Cool Output Curve
A nonlinear output curve may improve performance
when the response of the output device is nonlinear.
If a cool output uses one of the nonlinear curves a
PID calculation yields a lower actual output level
than a linear output would provide.
These output curves are used in plastics extruder
applications: curve 1 for oil-cooled extruders and
curve 2 for water-cooled extruders.
A
ctual Output P
ow
er
0
20
40
60
80
100
PID Calculation
Linear
Linear
Curve 1
Curve 2
Select a nonlinear cool output curve with Cool Out-
put Curve [`C;Cr] (Setup Menu, Loop Menu).
Control Methods
Output Configuration
Controller outputs can be configured as a heat out-
put, a cool output, an alarm output or deactivated
and driven by any available control loop. No depen-
dency limitations have been placed on the available
combinations. The outputs can be configured in any
combination. For instance, all three could be set to
cool.
Heat and cool outputs use the set point and Oper-
ations parameters to determine the output value. All
heat and cool outputs use the same set point value.
Heat and cool each have their own set of control pa-
rameters. All heat outputs use the same set of heat
control parameters and all cool outputs use the same
set of cool output parameters. Each alarm output
has its own set of configuration parameters and set
points, allowing independent operation.
Auto (closed loop) and Manual (open loop) Control
The controller has two basic modes of operation, auto
mode and manual mode. Auto mode allows the con-
troller to decide whether to perform closed-loop con-
trol or to follow the settings of Input Error Failure
[FAiL]
(Setup Page, Loop Menu). The manual mode
only allows open-loop control. The RMC module is
normally used in the auto mode. The manual mode
is usually only used for specialty applications or for
troubleshooting. Manual mode is open-loop control