Find stud in c face g782, 6 sear c h cy cles – HEIDENHAIN SW 548328-05 DIN Programming User Manual
Page 462
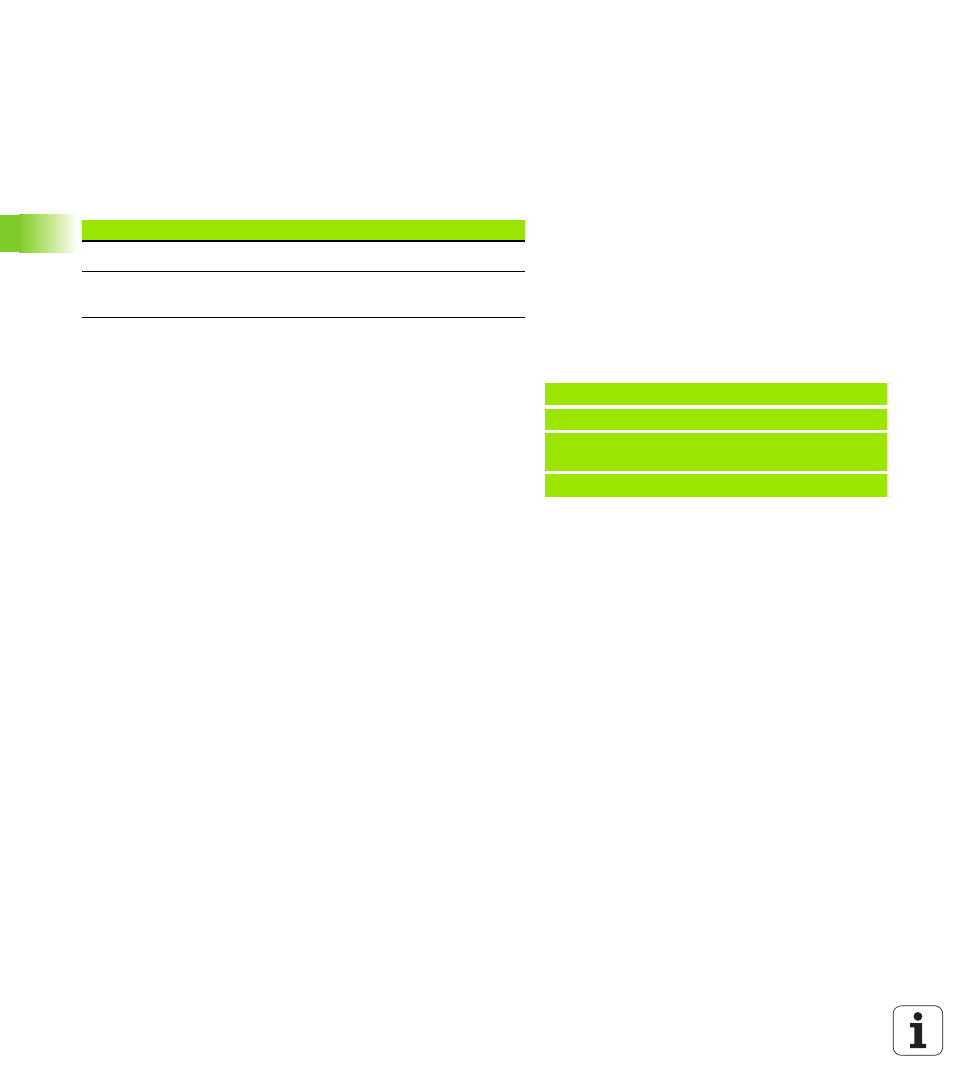
462
Touch probe cycles
5.6 Sear
c
h
cy
cles
Find stud in C face G782
Cycle G782 probes the workpiece face several times with the Z axis.
Prior to each probing, the C axis is rotated by a distance defined in the
cycle until a stud is found. Optionally, the cycle determines the mean
value by two probing operations on the stud diameter.
If the tolerance value defined in the cycle is exceeded, the cycle saves
the measured deviation as zero point shift. The result of the
measurement is saved additionally in the variable #i99.
Cycle run
From the current position the touch probe moves along the measuring
axis X toward the measuring point. When the stylus touches the
workpiece, the measured value is saved and the touch probe is
positioned back to the starting point. Then the cycle rotates the C axis
by the angle defined in the Search Grid parameter RC and probes again
with the X axis. This process is repeated until a stud is found. The
cycle performs two probing operations on the stud diameter with the
C axis, calculates the center of the hole and places the zero point in
the C axis.
The control outputs an error message if the touch probe does not
reach any touch point within the defined measuring path. If a
maximum deviation WE was programmed, the measuring point is
approached twice and the mean value is saved as result. If the
difference of the measurements is greater than the maximum
deviation WE, the program run is interrupted and an error message is
displayed.
Example: G782 Find stud in C face
. . .
MACHINING
N3 G782 R1 D1 K2 C0 RC10 IC20 AC0 BD0.2 Q0
P0 H0
. . .
Result #i99
Meaning
< 999997
Result of first measurement
999999
Deviation of probing operations was higher than
programmed in Maximum Deviation parameter WE.
Parameters
R
Type of zero point shift:
1: Activate table and G152 zero point shift and additionally
save in zero point table. The zero-point shift also remains
active after the program run.
2: Activate zero point shift with G152 for the further program
run. Zero point shift no longer active after program run.
D
Result:
1: Position: Set zero point without determining the stud
center. The stud diameter is not probed.
2: Object center: Before the zero point is set, determine stud
center in two probing operations with the C axis.
K
Incremental measuring path X (signed): Maximum measuring
path for probing. The algebraic sign determines the probing
direction.
C
Starting position C: Position of the C axis for the first probing
operation
RC Search grid Ci: Stepping angle of the C axis for the subsequent
probing operations