26 milling cy cles – HEIDENHAIN SW 548328-05 DIN Programming User Manual
Page 360
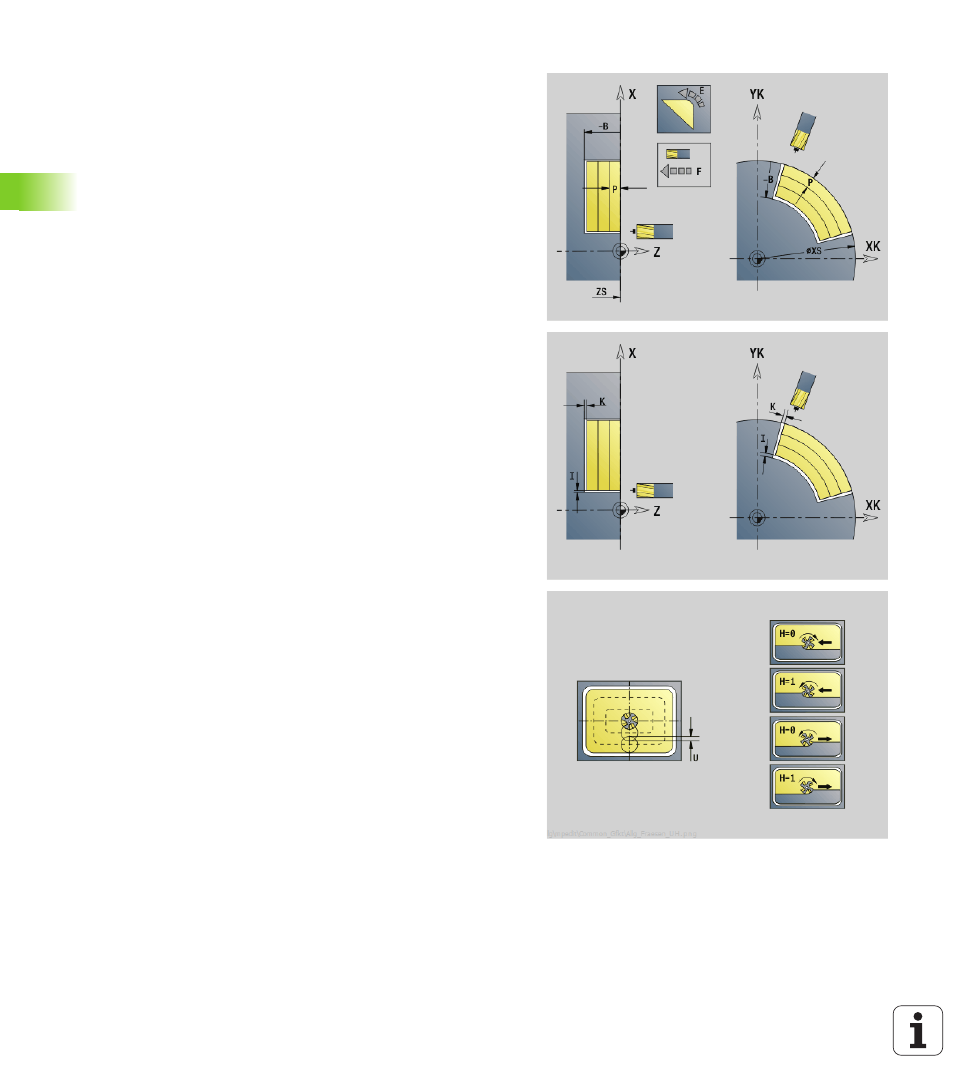
360
DIN programming
4.26 Milling cy
cles
G845—Milling
You can change the cutting direction with the cutting direction H,
the machining direction Q and the direction of tool rotation (see
following table). Program only the parameters given in the following
table.
See also:
G845—Fundamentals: Page 358
G845—Calculating hole positions: Page 359
Parameters—Milling
ID
Milling contour—name of the contour to be milled
NS
Starting block no. of contour
Figures: Block number of the figure
Free closed contour: A contour element (not starting point)
B
Milling depth (default: depth from the contour description)
P
(Maximum) infeed (default: milling in one infeed)
XS
Milling top edge—lateral surface (replaces the reference plane
from the contour definition)
ZS
Milling top edge—face (replaces the reference plane from the
contour definition)
I
Oversize in X direction (radius)
K
Oversize in Z direction
U
(Minimum) overlap factor. Defines the overlap of milling paths
(default: 0.5).
Overlap = U*milling diameter
V
Overrun factor (no effect with C-axis machining)
H
Cutting direction (default: 0)
0: Up-cut milling
1: Climb milling
F
Feed rate for infeed (default: active feed rate)
E
Reduced feed rate for circular elements (default: current feed
rate)
RB
Retraction plane (default: back to starting position)
Front or read face: Return position in Z direction
Lateral surface: Return position in X direction (diameter)
Q
Machining direction (default: 0)
0: From the inside out (from the inside towards the outside)
1: From the outside in (from the outside towards the inside)