NORD Drivesystems BU0200 User Manual
Page 203
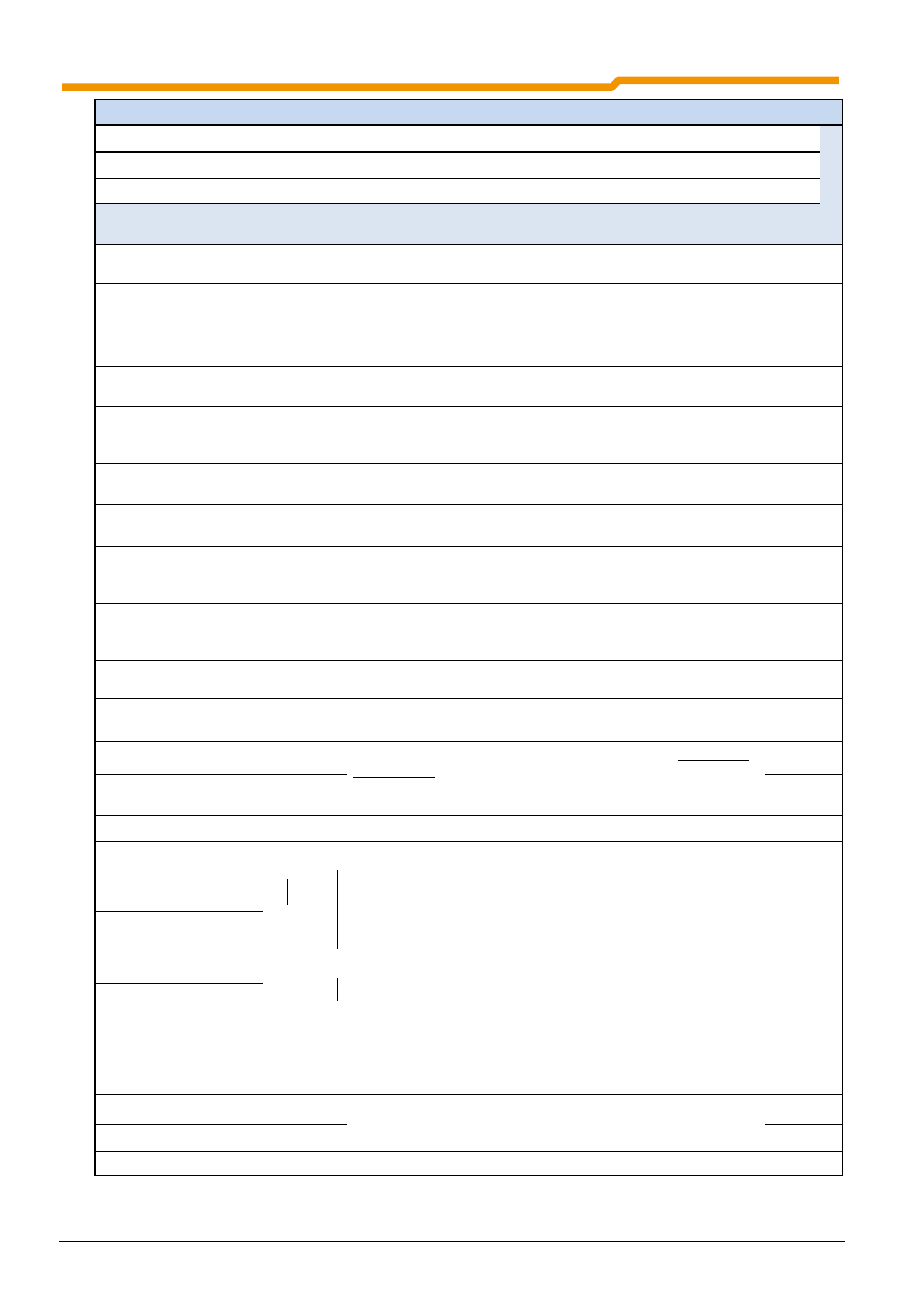
SK 200E Manual for frequency inverters
202
Subject to technical alterations
BU 0200 GB-4411
Value Function
Description
Signal
05
1
Fixed frequency 2
The frequency from P465 [02] is added to the actual setpoint value.
High
06
1
Fixed frequency 3
The frequency from P465 [03] is added to the actual setpoint value.
High
07
1
Fixed frequency 4
The frequency from P465 [04] is added to the actual setpoint value.
High
If several fixed frequencies are actuated simultaneously, then they are added with the correct sign. In addition,
the analog setpoint (P400) and if required, the minimum frequency (P104) are added.
08
Param set switching
"Parameter set switchover 1"
Selection of the active parameter set 1…4 (P100)
High
09
Maintain the freq
"Maintain the frequency"
During the acceleration or deceleration phase, a Low level will
cause the actual output frequency to be "held". A High level allows
the ramp to proceed.
Low
10
2
Voltage disable
The FI output voltage is switched off; the motor runs down freely.
Low
11
2
Quick stop
The FI reduces the frequency according to the programmed quick
stop time (P426).
Low
12
2
Fault acknowledgem
"Fault acknowledgement"
Error acknowledgement with an external signal. If this function is
not programmed, a fault can also be acknowledged by a low
enable setting (P506).
0
1
Flank
13
2
PTC resistor input
Only with the use of a temperature monitor (bimetal switching
contact). Switch-off delay = 2sec, warning after 1 sec.
High
14
2
Remote control
With bus system control, low level switches the control to control
via control terminals.
High
15
Jog frequency
1
The fixed frequency value can be adjusted using the
HIGHER/LOWER and OK keys (P113), if control is via the
SimpleBox or ParameterBox.
High
16
Motor potentiometer
As in setting 09, however, the frequency is not maintained below
the minimum frequency P104 and above the maximum frequency
P105.
Low
17
ParaSetSwitching 2
"Parameter set switchover 2"
Selection of the active parameter set 1…4 (P100)
High
18
2
Watchdog
Input must see a high flank cyclically (P460), otherwise error E012
will cause a shutdown. Function starts with the 1st High flank.
0
1
Flank
19
Setpoint 1 on/off
Analog input switch-on and switch-off 1/2 (high = ON) of the first
I/O extension. The low signal sets the analog input to 0% which
does not lead to shutdown when the minimum frequency (P104) >
than the absolute minimum frequency (P505).
High
20
Setpoint 2 on/off
High
21
...25 reserved for Posicon
26
Analog function
Dig2+3
("0-10V")
Th
e
s
e
f
u
n
c
ti
o
n
s
c
a
n
o
n
ly
be
u
s
e
d
f
o
r t
h
e
d
ig
it
a
l
in
p
u
ts
2
(P4
2
0
[
-0
2
])
a
n
d
3
(P4
2
0
[
-0
3
])
and
n
o
t
wit
h
SK
2
x
0
E
S 4
!
Via DIN 2 and DIN 3impulses which are proportional to an analog
signal can be evaluated with this setting. The function of this
signal is determined in parameter P400
[-06] or [-07].
The conversion 0-10V to impulses can be carried out via the
Customer Unit SK CU/TU4-24V-... This module includes an
analog input and an impulse output (ADC).
In setting { 28 } a reversal of the direction of rotation takes place
with an analog value <5V.
An application example is described in Section 3.4.2.
Impulses
≈ 1.6-
16kHz
27
Analog function
2-10V Dig2+3
28
Analog function
5-10V Dig2+3
30
Inhibit PID
Switching the PID controller / process controller function on and
off (High = ON)
High
31
2
Inhibit turn right
Blocks the >Enable right/left< via a digital input or Bus control.
Does not depend on the actual direction of rotation of the motor
(e.g. following negated setpoint).
Low
32
2
Inhibit turn left
Low
33
... 44 reserved
...continued on the next page