2 features of the ecsxp p axis module, Features of the ecsxp axis module, Preface and general information – Lenze ECSCPxxx User Manual
Page 15
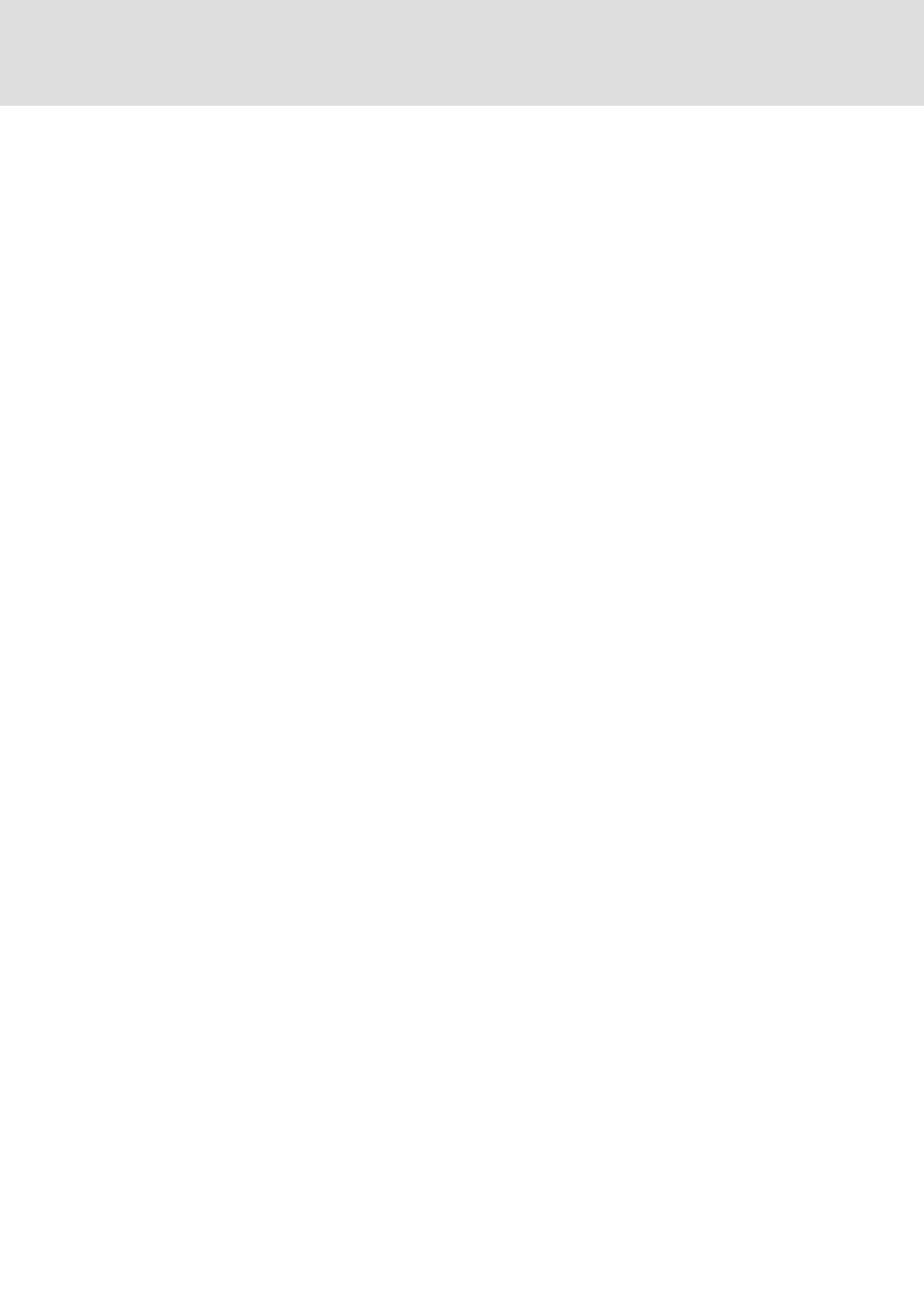
Preface and general information
Features of the ECSxP
l
15
EDBCSXP064 EN 8.0
1.2
Features of the ECSxP axis module
ƒ
Safety function "safe torque off" (formerly "safe standstill")
ƒ
15 separate positioning profile can be stored:
– Positioning in a finite travel range (absolute measuring system)
– Continuous positioning in one direction (incremental dimensioning system), e.g.
for cut−to−length cutters
– Touch probe positioning (mark sensor)
– "Electrical shaft" with classic digital frequency coupling or via CAN
ƒ
Additional profile functions:
– Speed override via analog input or per process data communication (PDO) via CAN
or fieldbus module at the automation interface (AIF)
– Stretch factor for the "electrical shaft" function
– Torque limitation after positioning
– Profile continuation after profile stop
– Immediate profile change during positioning(direct change)
ƒ
Homing, 14 different modes
ƒ
Manual jog
ƒ
Brake logic activatable
ƒ
Software based monitoring of the travel range and of the hardware limit switch
ƒ
Process coordination by higher−level host system (PLC)
ƒ
Double CAN ON BORD
– MotionBus (CAN):
Interface X4 "CAN" (PDO1, Sync−based) for communicating with a higher−level
host system (PLC) or further controllers.
– System bus (CAN):
Interface X14 "CAN−AUX" for parameter setting and diagnostics
ƒ
Selectable control interfaces (via code C4010):
– MotionBus (CAN)
– System bus (CAN−AUX)
– Fieldbus via the automation interface (AIF)
– Via codes per parameter data channel
ƒ
Supported feedback systems:
– Resolver with and without position storage
– Encoder (incremental encoder (TTL encoder), sin/cos encoder)
ƒ
Commissioning, parameter setting and diagnostics with the Lenze parameter
setting and operating program "Global Drive Control" (GDC) or the XT EMZ9371BC
keypad