Commissioning – Lenze ECSCPxxx User Manual
Page 224
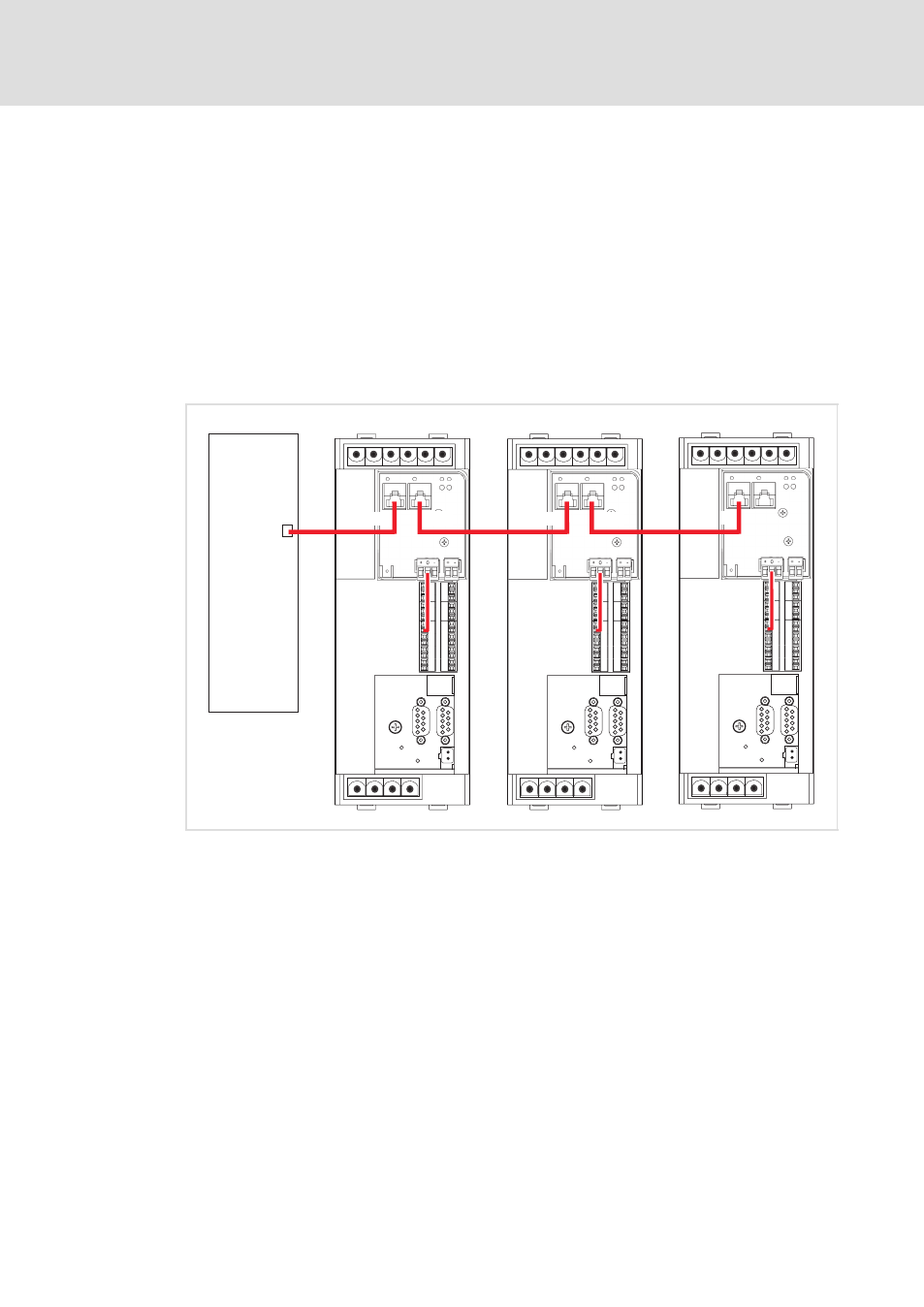
Commissioning
Configuring the electrical shaft ("E−Shaft")
Electrical shaft via EtherCAT with PLC as electrical shaft master
l
224
EDBCSXP064 EN 8.0
6.18.5
Electrical shaft via EtherCAT with PLC as electrical shaft master
The following special features apply for the master value transmission via EtherCAT
between master and slave(s):
ƒ
The master control (PLC) undertakes the function of the E−shaft master as digital
master value source as well as the control of the slave drives (start / stop of the
positioning profile).
ƒ
Control information and master value are comprised in a telegram and individually
transmitted to each E−shaft slave.
ƒ
The slave drives follow the master value (angle) cyclically specified by the E−shaft
master as speed and position controlled path followers.
Slave n
Slave 2
Slave 1
PLC
X
S
OUT
OUT
IN
IN
IN
EMF2192IB
EMF2192IB
EMF2192IB
X6/DI1
(Sync)
X6/DI1
(Sync)
X6/DI1
(Sync)
ECSXA090
Fig. 6−55
Electrical shaft via EtherCAT with master control as E−Shaft−Master
PLC
Higher−level control (PLC) as electrical shaft master and for control of the drive
system
Slave 1 ... 3
Slave drives (ECSxP axis modules )
The data exchange between the master control (PLC) and the slave drives is made via the
EMF2191IB EtherCAT communication module at the AIF interface X1.
Each slave drive receives an individual process data telegram from the master within a
fixed cycle time. This contains the "Ctrl1" control word with the control bits from the
master to the slaves and the master value for the electrical shaft function. The slave drives
then transmit a status telegram back to the master.
A sync signal is cyclically transmitted via the digital input terminal X6/DI1 at the axis
module and the sync terminal at the EMF2192IB communication module.
Commissioning steps for a mimimum configuration
The codes can be found in the GDC in the "Positioning/E−shaft" menu item.