Cycle parameters, 3 drilling (cy cle 20 0) – HEIDENHAIN iTNC 530 (34049x-08) Cycle programming User Manual
Page 80
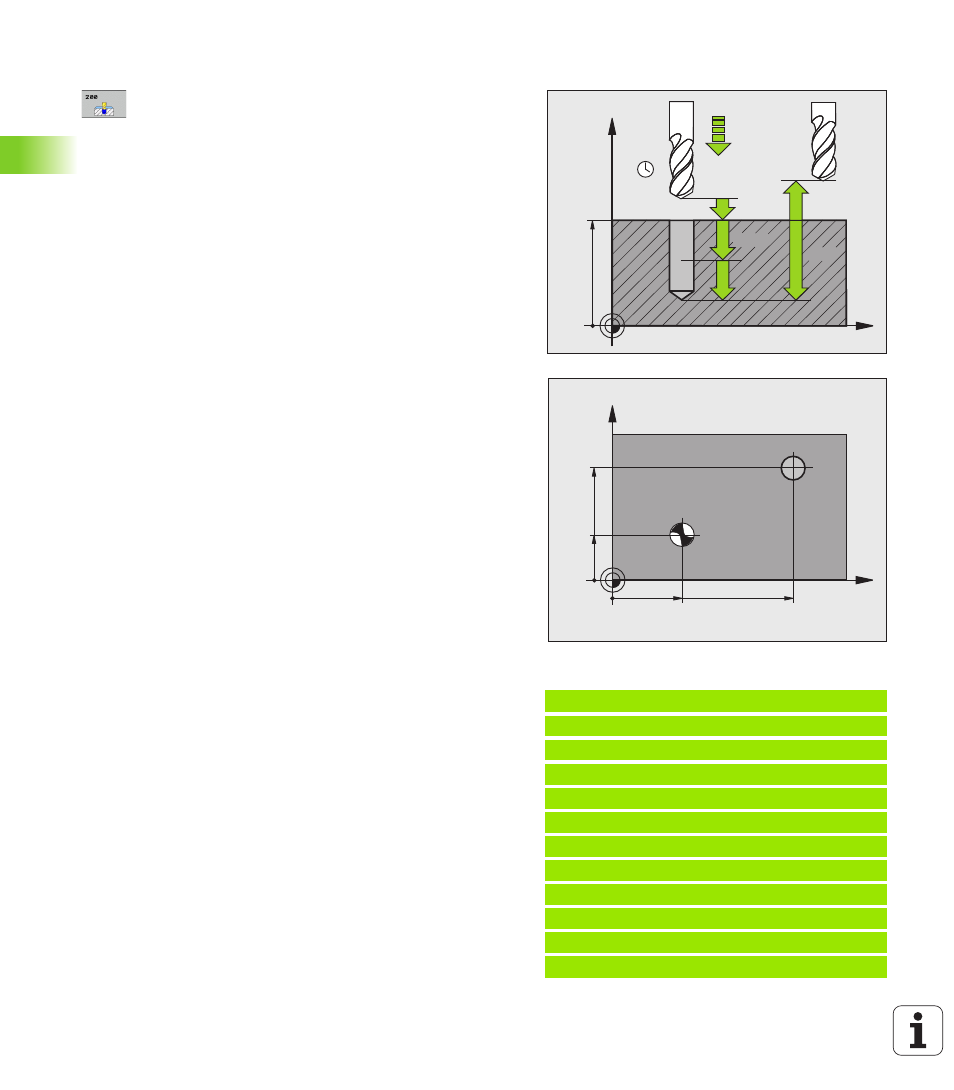
80
Fixed cycles: drilling
3.3
DRILLING
(Cy
cle
20
0)
Cycle parameters
Set-up clearance
Q200 (incremental): Distance
between tool tip and workpiece surface. Enter a
positive value. Input range 0 to 99999.9999;
alternatively PREDEF
Depth
Q201 (incremental): Distance between
workpiece surface and bottom of hole (tip of drill
taper). Input range -99999.9999 to 99999.9999
Feed rate for plunging
Q206: Traversing speed of
the tool during drilling in mm/min. Input range 0 to
99999.999; alternatively FAUTO, FU
Plunging depth
Q202 (incremental): Infeed per cut.
Input range 0 to 99999.9999. The depth does not
have to be a multiple of the plunging depth. The TNC
will go to depth in one movement if
the plunging depth is equal to the depth
the plunging depth is greater than the depth
Dwell time at top
Q210: Time in seconds that the
tool remains at set-up clearance after having been
retracted from the hole for chip removal. Input range
0 to 3600.0000; alternatively PREDEF
Workpiece surface coordinate
Q203 (absolute):
Coordinate of the workpiece surface. Input range
-99999.9999 to 99999.9999
2nd set-up clearance
Q204 (incremental): Coordinate
in the spindle axis at which no collision between tool
and workpiece (fixtures) can occur. Input range 0 to
99999.9999; alternatively PREDEF
Dwell time at depth
Q211: Time in seconds that the
tool remains at the hole bottom. Input range 0 to
3600.0000; alternatively PREDEF
Example: NC blocks
11 CYCL DEF 200 DRILLING
Q200=2
;SET-UP CLEARANCE
Q201=-15
;DEPTH
Q206=250
;FEED RATE FOR PLNGNG
Q202=5
;PLUNGING DEPTH
Q210=0
;DWELL TIME AT TOP
Q203=+20
;SURFACE COORDINATE
Q204=100
;2ND SET-UP CLEARANCE
Q211=0.1
;DWELL TIME AT DEPTH
12 L X+30 Y+20 FMAX M3
13 CYCL CALL
14 L X+80 Y+50 FMAX M99
X
Z
Q200
Q201
Q206
Q202
Q210
Q203
Q204
30
X
Y
20
80
50