Please note while programming – HEIDENHAIN iTNC 530 (34049x-08) Cycle programming User Manual
Page 321
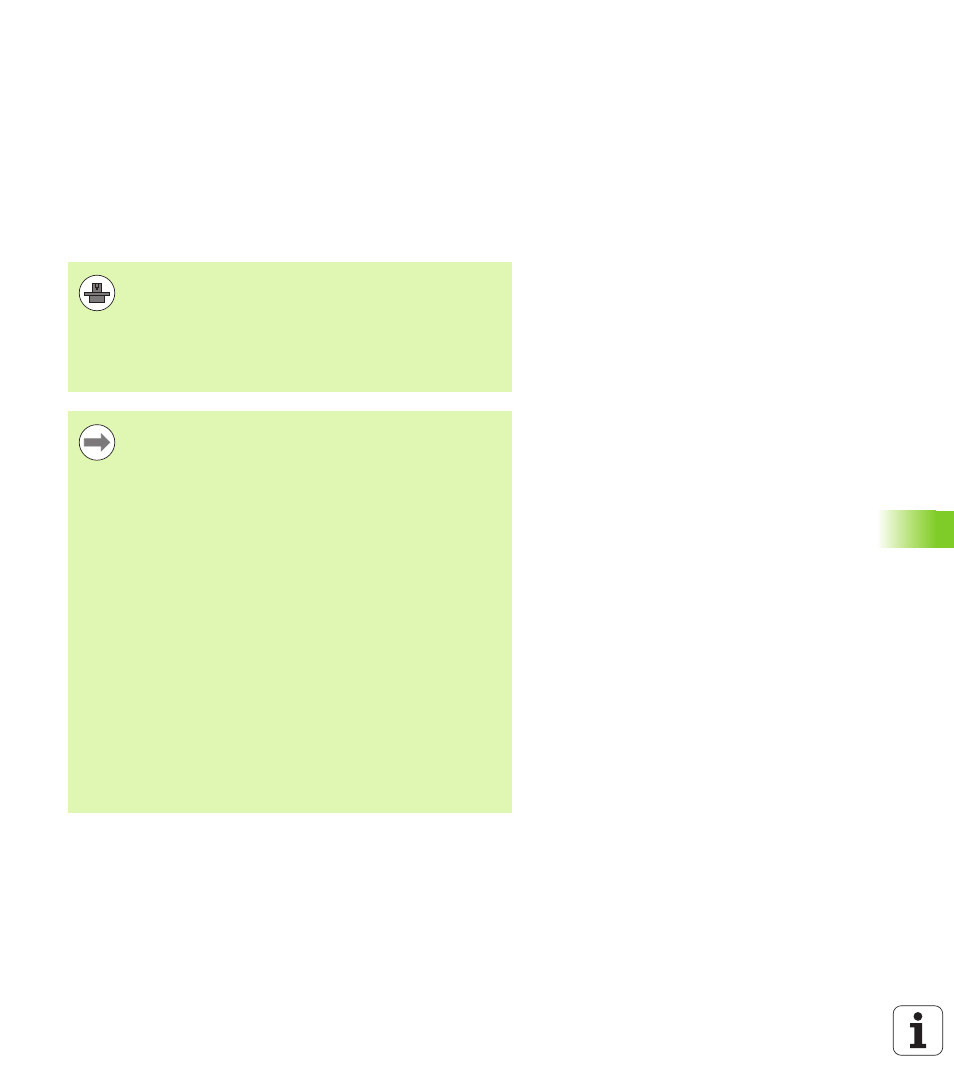
HEIDENHAIN iTNC 530
321
12.7
INTERPOLA
T
ION
TURNING
(sof
tw
ar
e
option,
Cy
cle
290,
DIN/ISO:
G290)
Please note while programming:
You can use a turning tool or a milling tool (Q444=0) for this cycle. The
geometry data of this tool are defined in the TOOL.T tool table as
follows:
Column L (DL for compensation values):
Length of the tool (bottommost point of the tool cutting edge)
Column R (DR for compensation values):
Effective radius of the tool (outermost point of the tool cutting edge)
Column R2 (DR2 for compensation values):
Cutting-edge radius of the tool
Machine and TNC must be specially prepared by the
machine tool builder for use of this cycle. Refer to your
machine manual.
This cycle is effective only for machines with servo-
controlled spindle (exception: Q444=0).
Software option 96 must be enabled.
Roughing operations with multiple passes are not possible
in this cycle.
The center of interpolation is the tool position at the time
the cycle is called.
The TNC extends the first surface to be machined by the
safety clearance.
You can use the values DL and DR of the TOOL CALL block
to realize oversizes. DR2 entries in the TOOL CALL block are
not taken into account by the TNC.
Before cycle call, define a large tolerance with Cycle 32 for
your machine to attain high contour speeds.
Program a cutting speed that can just be reached at the
contour speed of the machine axes. This ensures
optimum geometry resolution and a constant machining
speed.
The TNC does not monitor for possible damage to the
contour, which might be caused by unsuitable tool
geometry.
Note the machining variants: See "Machining variants" on