HEIDENHAIN iTNC 530 (34049x-08) Cycle programming User Manual
Page 380
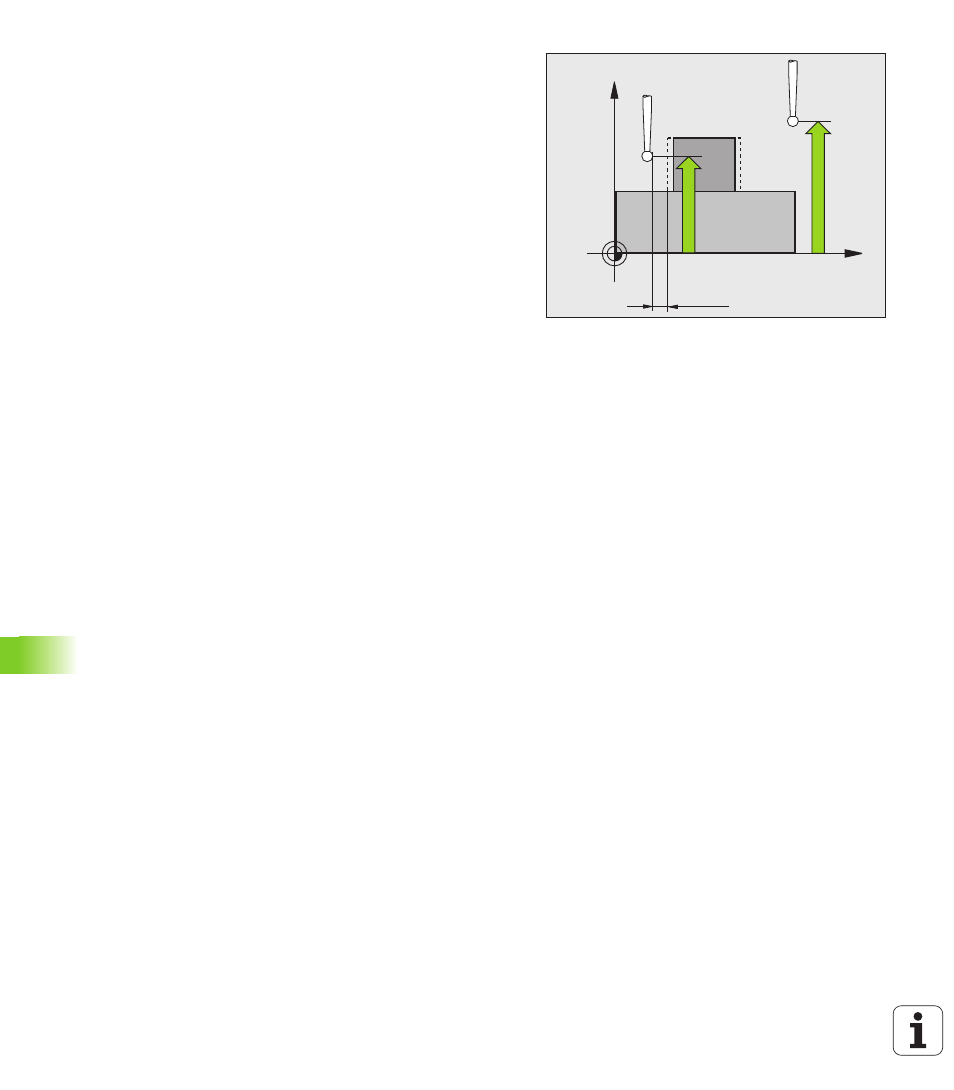
380
Touch probe cycles: automatic datum setting
15.7
D
A
TUM
FR
OM
OUTSIDE
OF
CIR
C
LE
(Cy
cle
413,
DIN/ISO:
G413)
Measuring height in the touch probe axis
Q261
(absolute): Coordinate of the ball tip center (= touch
point) in the touch probe axis in which the
measurement is to be made. Input range
-99999.9999 to 99999.9999
Set-up clearance
Q320 (incremental): Additional
distance between measuring point and ball tip. Q320
is added to MP6140. Input range 0 to 99999.9999,
alternatively PREDEF
Clearance height
Q260 (absolute): Coordinate in the
touch probe axis at which no collision between touch
probe and workpiece (fixtures) can occur. Input range
-99999.9999 to 99999.9999, alternatively PREDEF
Traversing to clearance height
Q301: Definition of
how the touch probe is to move between the
measuring points:
0
: Move at measuring height between measuring
points
1
: Move at clearance height between measuring
points
Alternatively PREDEF
Datum number in table
Q305: Enter the number in the
datum/preset table in which the TNC is to save the
coordinates of the stud center. If you enter Q305=0,
the TNC automatically sets the display so that the
new datum is on the stud center. Input range 0 to
2999
New datum for reference axis
Q331 (absolute):
Coordinate in the reference axis at which the TNC
should set the stud center. Default setting = 0 input
range -99999.9999 to 99999.9999
New datum for minor axis
Q332 (absolute):
Coordinate in the minor axis at which the TNC should
set the stud center. Default setting = 0 input range
-99999.9999 to 99999.9999
Measured-value transfer (0, 1)
Q303: Specify
whether the determined datum is to be saved in the
datum table or in the preset table:
–1
: Do not use. Is entered by the TNC when old
programs are read in (see "Saving the calculated
datum" on page 358).
0
: Write determined datum in the active datum table.
The reference system is the active workpiece
coordinate system.
1
: Write determined datum in the preset table. The
reference system is the machine coordinate system
(REF system).
X
Z
Q261
Q260
MP6140
+
Q320