HEIDENHAIN iTNC 530 (34049x-08) Cycle programming User Manual
Page 348
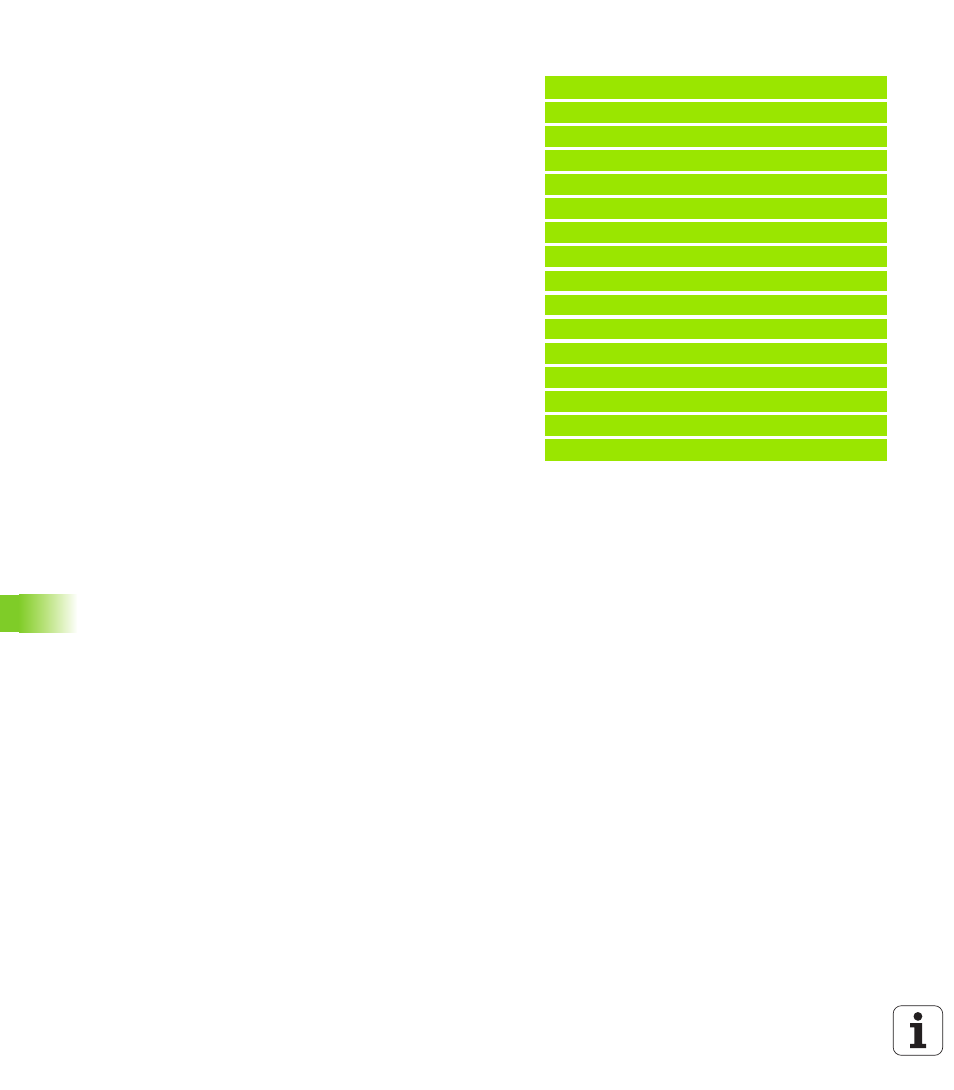
348
Touch probe cycles: automatic measurement of workpiece misalignment
14.5 BA
SIC R
O
TA
TION compensation via r
o
tary axis (Cy
cle 403,
DIN/ISO:
G403)
Clearance height
Q260 (absolute): Coordinate in the
touch probe axis at which no collision between touch
probe and workpiece (fixtures) can occur. Input range
-99999.9999 to 99999.9999, alternatively PREDEF
Traversing to clearance height
Q301: Definition of
how the touch probe is to move between the
measuring points:
0
: Move at measuring height between measuring
points
1
: Move at clearance height between measuring
points
Axis for compensation motion
Q312: Assignment of
the rotary axis in which the TNC is to compensate the
measured misalignment. Recommendation: Use the
automatic mode 0:
0
: Automatic mode; the TNC automatically
determines the axis for the compensation movement
from the positions of the active rotary and probing
axes.
4
: Compensate misalignment with rotary axis A
5
: Compensate misalignment with rotary axis B
6
: Compensate misalignment with rotary axis C
Set to zero after alignment
Q337: Definition of
whether the TNC should set the display of the aligned
rotary axis to zero:
0
: Do not reset the display of the rotary axis to 0 after
alignment
1
: Reset the display of the rotary axis to 0 after
alignment
Number in table
Q305: Enter the number in the
preset table/datum table in which the TNC is to set
the rotary axis to zero. Only effective if Q337 is set to
1. Input range 0 to 2999
Measured-value transfer (0, 1)
Q303: Specify
whether the determined angle is to be saved in the
datum table or in the preset table:
0:
Write the measured angle as a datum shift in the
active datum table. The reference system is the
active workpiece coordinate system.
1
: Write the measured angle in the preset table. The
reference system is the machine coordinate system
(REF system).
Reference angle? (0=ref. axis)
Q380: Angle with
which the TNC is to align the probed straight line.
Only effective if the rotary axis C is selected
(Q312=6). Input range -360.000 to 360.000
Example: NC blocks
5 TCH PROBE 403 ROT IN C-AXIS
Q263=+25
;1ST POINT 1ST AXIS
Q264=+10
;1ST POINT 2ND AXIS
Q265=+40
;2ND POINT 1ST AXIS
Q266=+17
;2ND POINT 2ND AXIS
Q272=2
;MEASURING AXIS
Q267=+1
;TRAVERSE DIRECTION
Q261=-5
;MEASURING HEIGHT
Q320=0
;SET-UP CLEARANCE
Q260=+20
;CLEARANCE HEIGHT
Q301=0
;MOVE TO CLEARANCE
Q312=6
;COMPENSATION AXIS
Q337=0
;SET TO ZERO
Q305=1
;NO. IN TABLE
Q303=+1
;MEAS. VALUE TRANSFER
Q380=+0
;REFERENCE ANGLE