HEIDENHAIN TNC 426B (280 472) ISO programming User Manual
Page 153
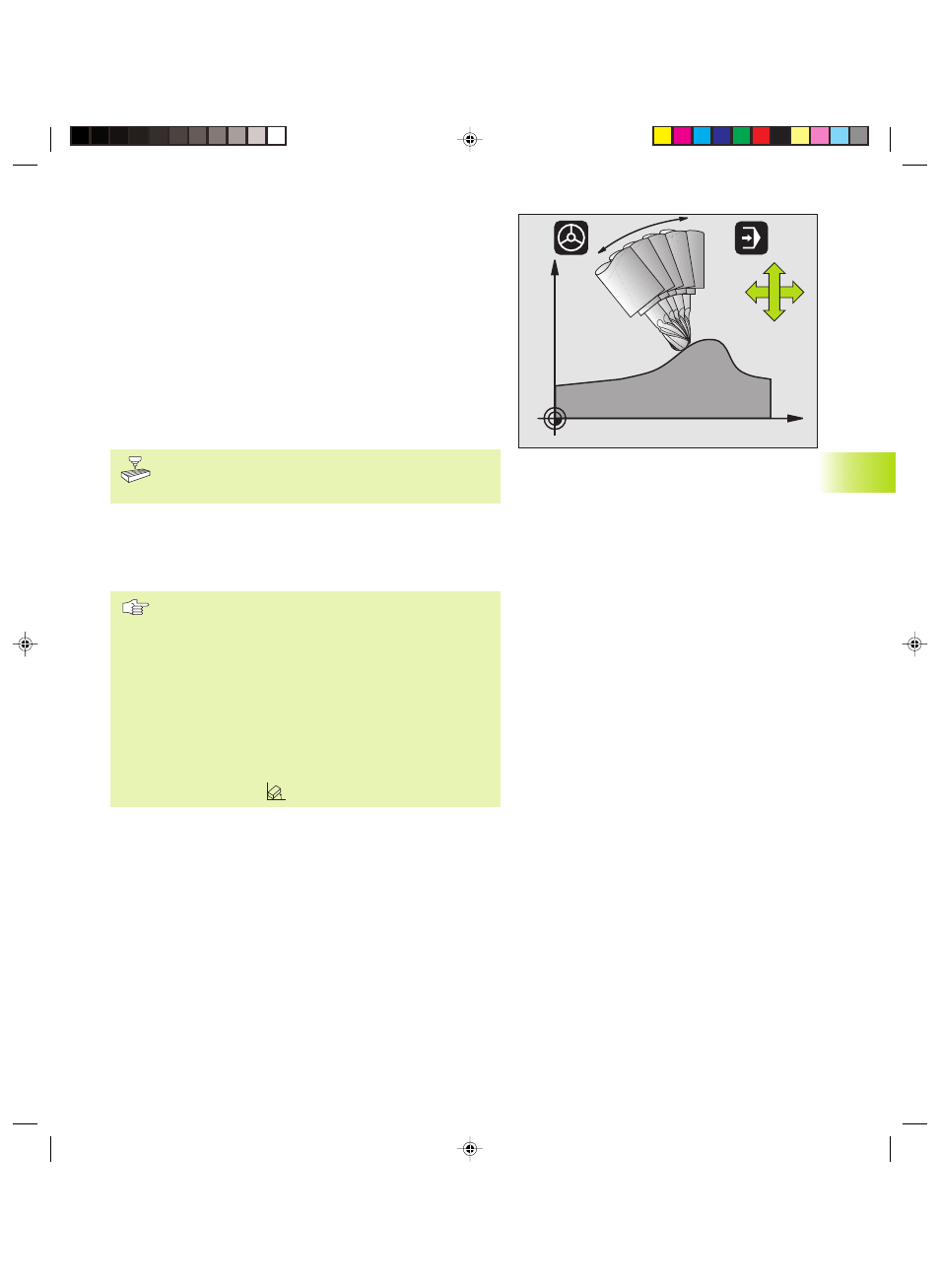
137
HEIDENHAIN TNC 410, TNC 426, TNC 430
Maintaining the position of the tool tip when
positioning with tilted axes (TCPM*): M128
Standard behavior
The TNC moves the tool to the positions given in the part program.
If the position of a tilted axis changes in the program, the resulting
offset in the linear axes must be calculated and traversed in a
positioning block (see figure on the left with M114).
Behavior with M128
If the position of a controlled tilted axis changes in the program, the
position of the tool tip to the workpiece remains the same.
If you wish to use the handwheel to change the position of the
tilted axis during program run, use M118 in conjunction with M128.
Handwheel positioning in a machine-based coordinate is possible
when M128 is active.
For tilted axes with Hirth coupling: Do not change the
position of the tilted axis after retracting the tool.
Otherwise you might damage the contour.
After M128 you can program another feed rate, at which the TNC
will carry out the compensation movements in the linear axes. If
you program no feed rate here, or if you program a larger feed rate
than is defined in machine parameters 7471, the feed rate from
machine parameter 7471 will be effective.
Reset M128 before positioning with M91 or M92 and
before a T block.
To avoid contour gouging you must use only spherical
cutters with M128.
The tool length must refer to the spherical center of the
tool tip.
The TNC does not adjust the active radius compensation
in accordance with the new position of the tilted axis.
The result is an error which is dependent on the angular
position of the rotary axis.
If M128 is active, the TNC shows in the status display the
following symbol:
an
*) TCPM = Tool Center Point Management
X
Z
B
Z
X
7.5 Miscellaneous F
unctions f
o
r
Rotary A
x
e
s
Hkap7.pm6
29.06.2006, 08:06
137