Gasboy Atlas Start-up User Manual
Page 176
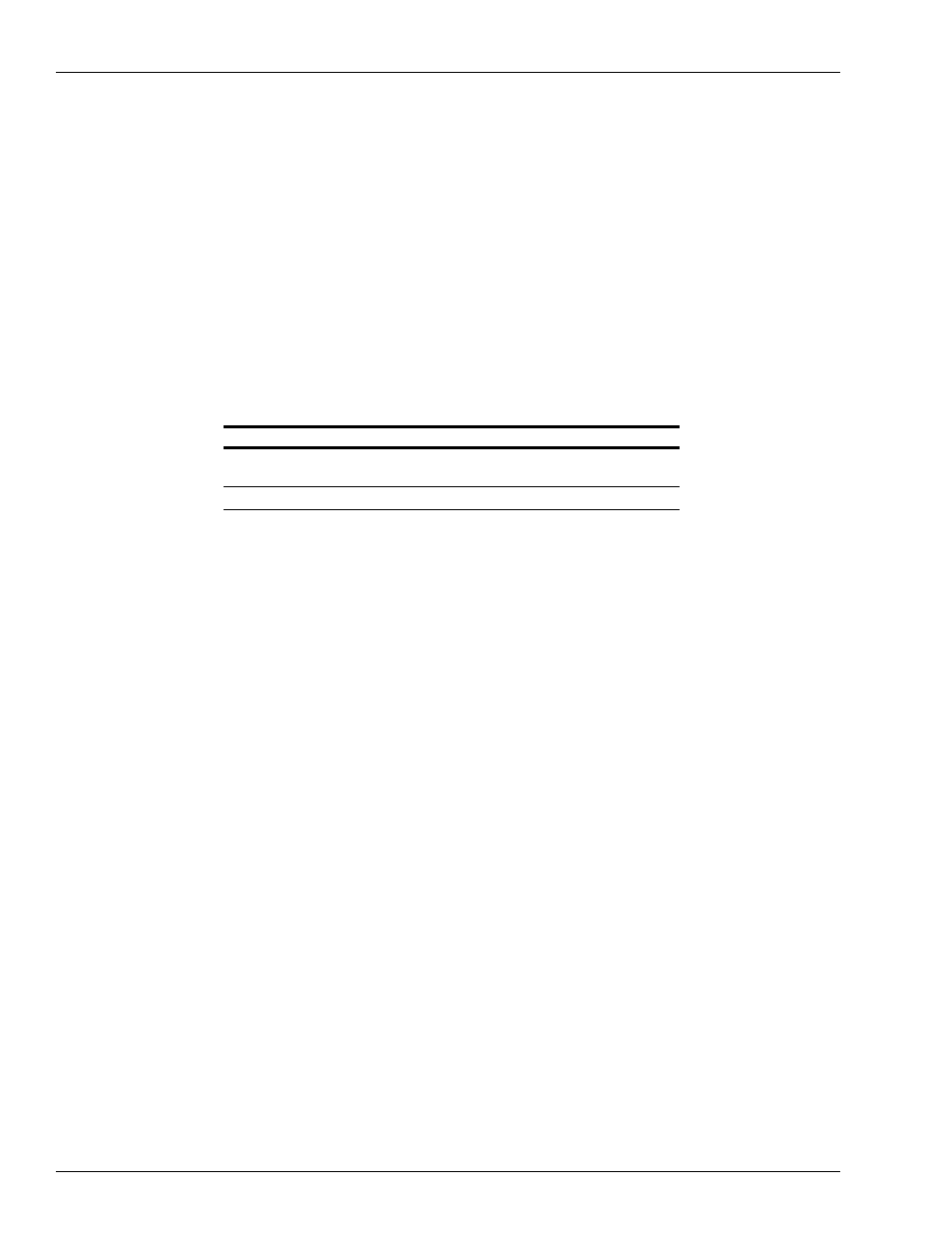
Page 6-56
MDE-4334D Atlas™ Start-up and Service Manual · July 2013
Hydraulic/Mechanical Components
Pumping Unit
Service Tips
• Adjustment of pressure in the PRV is not recommended normally. A lower adjustment can
result in low flow rates. A higher adjustment can result in premature motor failure.
• While inspecting or installing PRVs, avoid introducing contamination into the unit.
• PRVs normally fail only from excessive wear, especially at the seat or in the valve bore
area, or sticking from defective parts or contamination. Low flow, high pressure (motor
failures and so on), overheating, or noise can result in PRV failure.
• Replace the external seals while inspecting or servicing the valve, if the seals are more
than six months old or appear degraded.
• Units that are idle for excessive time with the motor running and no fuel being dispensed
may overheat resulting in vapor lock and so on. Use pump time-outs (Electronic units) or
lower pressures to reduce this possibility.
• When the pumping unit is operating at full speed, the discharge pressure must not exceed
50 psi (3.5 bar) with any discharge restriction (fully open to fully close discharge). If the
pressure exceeds 50 psi (3.5 bar), refer to the following table:
Cause
Solution
Bypass/Pressure relief valve is stuck
operating at full open position.
Replace the valve.
Excessive voltage to the motor.
Measure proper input voltage to the motor.
Optimizing Adjustment on Pump Bypass Preload
It is not recommended to alter the bypass adjustment from the factory setting. However, if the
flow rate is low, and other means of increasing flow rate, such as cleaning filters have been
performed, adjustments can be made if the motor amperage is low.
1
Connect an amp probe to a power leg of the motor.
2
Operate the unit at full flow and in bypass, and record the amperage.
3
If the amperage is found to be substantially below the rated amperage, bypass adjustment can
be made using the following procedure.
Note: Before making adjustments, ensure that the motor has been switched off.
To optimize the bypass preload, proceed as follows:
1
Remove the adjustment cap on the pumping unit.
2
If the amperage from the initial test is low, turn the adjustment screw clockwise and increase
the preload (and the flow rate and motor load).
Note: If the initial bypass voltage is below 205 V for a 220 V system, or below 100 V for a
110 V system, then the wiring is insufficient to handle full motor loads. In such a case,
the maximum amperage must be set to a maximum of 4.9 A on a 220 V system and 9.5 A
on a 110 V system.
3
Run the unit and check the amperage at full flow and at bypass (both must be checked to verify
proper loading on the motor).
4
Adjust the screw to obtain amperage just below the maximum setting noted on the motor
faceplate.
5
Replace the adjustment cap. Disconnect the amp probe and replace the J-box cover.