Auto tune velocity and position loops, To tune the system using auto tune – Rockwell Automation 1398-PDM-xxx IQ Master Version 3.2.4 for IA-2000 and IQ-5000 Positioning Drive Modules, IQ-55 User Manual
Page 80
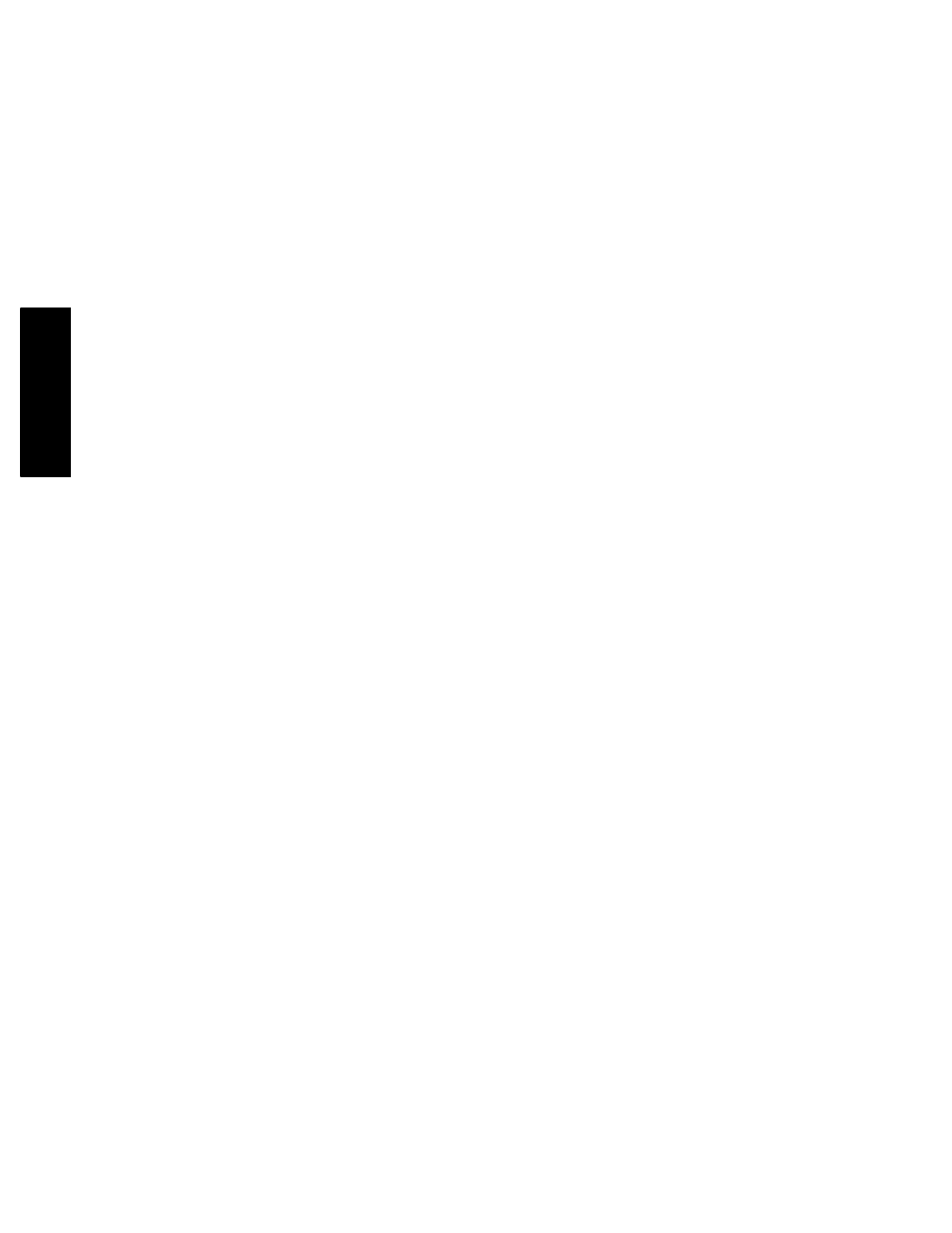
58
Run Menu • Tune
Publication 1398-PM601A-EN-P — October 2000
MENUS
Manual Tune provides a means of tuning the velocity and position control loops independently. The
inner velocity loop must be tuned first, as this tuning will affect the position loop response. This proce-
dure assumes that the system, including the machine the motor is connected to, can tolerate small–sig-
nal step velocity changes.
Auto Tune Velocity and Position Loops
To Tune the System using Auto Tune
1.
Disable the ULTRA Plus or IQ.
2.
Select Tune from the Run menu.
3.
Choose the Auto Tune button (if in the Manual Tune mode).
4.
Select the Application Type. The Application Type and Response settings are used to calculate the
system tuning gains after the system inertia estimation is complete. The Application Type can be
either Point to Point or Contouring. Auto Tune will set the velocity loop IGAIN to zero for Point to
Point. For Contouring, IGAIN is set to a nonzero value that results in about a 15% velocity step
overshoot. Auto Tune calculates values for KP, PGAIN, and for IGAIN if Application is set to Con-
touring. The other tuning parameters are set to: KI = 0, IZONE = 0, KFF = 100%, FGAIN = 0%,
KPZ = 0, PZONE = 0, and FILTER is turned off.
5.
Set the Direction radio button to Bidirectional, Positive, or Negative. The Direction setting deter-
mines the direction of motion during the Auto Tune process. When the direction is Positive or Neg-
ative, Max Distance is not the maximum distance moved from the starting point, but rather the
maximum distance moved during each acceleration and deceleration cycle of the Auto Tune pro-
cess. The positive direction is defined as clockwise rotation of the motor shaft when facing the
motor shaft end.
6.
Choose an appropriate Response radio button (High, Medium, or Low). The Response selection
determines the target bandwidth used to calculate the system gains. The velocity and position loop
bandwidths are:
7.
Adjust Step Current, Max Distance, and Max Velocity if required. Units are user units for Max Dis-
tance and user units per Timebase for Max Velocity. The default values should provide good results
for most systems. Reduce Step Current if the torque will exceed machine specifications.
8.
Choose the Enable button to enable the ULTRA Plus or IQ, then choose the Start button to begin
the Auto Tune process. The motor shaft will oscillate back and forth. The Enable and Start buttons
are toggle buttons–when chosen, the meaning of each button changes–the Enable button will
change to Disable and the Start button will change to Stop. Choosing the button again will toggle it
back to its original meaning.
9.
After about 5 seconds, the motion will cease and the ULTRA Plus or IQ will display the calculated
load inertia to motor inertia ratio, and the new calculated gains.
Under certain conditions, an incorrect value can be computed for the system inertia that will result in
Note: Auto Tune is not recommended if too much compliance or backlash exists in the mechanical
load. If this is the case, then manual tune is recommended.
Note: KFF at 100% will induce overshoot in some point to point applications. KFF at 100% is rec-
ommended in gearing applications.
Response
High
Medium
Low
Velocity Loop BW
30 Hz
15 Hz
7 Hz
Position Loop BW
10 Hz
5 Hz
2 Hz
Choose Medium if you are not sure which Response will suit your application.