Rockwell Automation 7000A PowerFlex Medium Voltage Drive (A-Frame) - Classic Control User Manual
Page 447
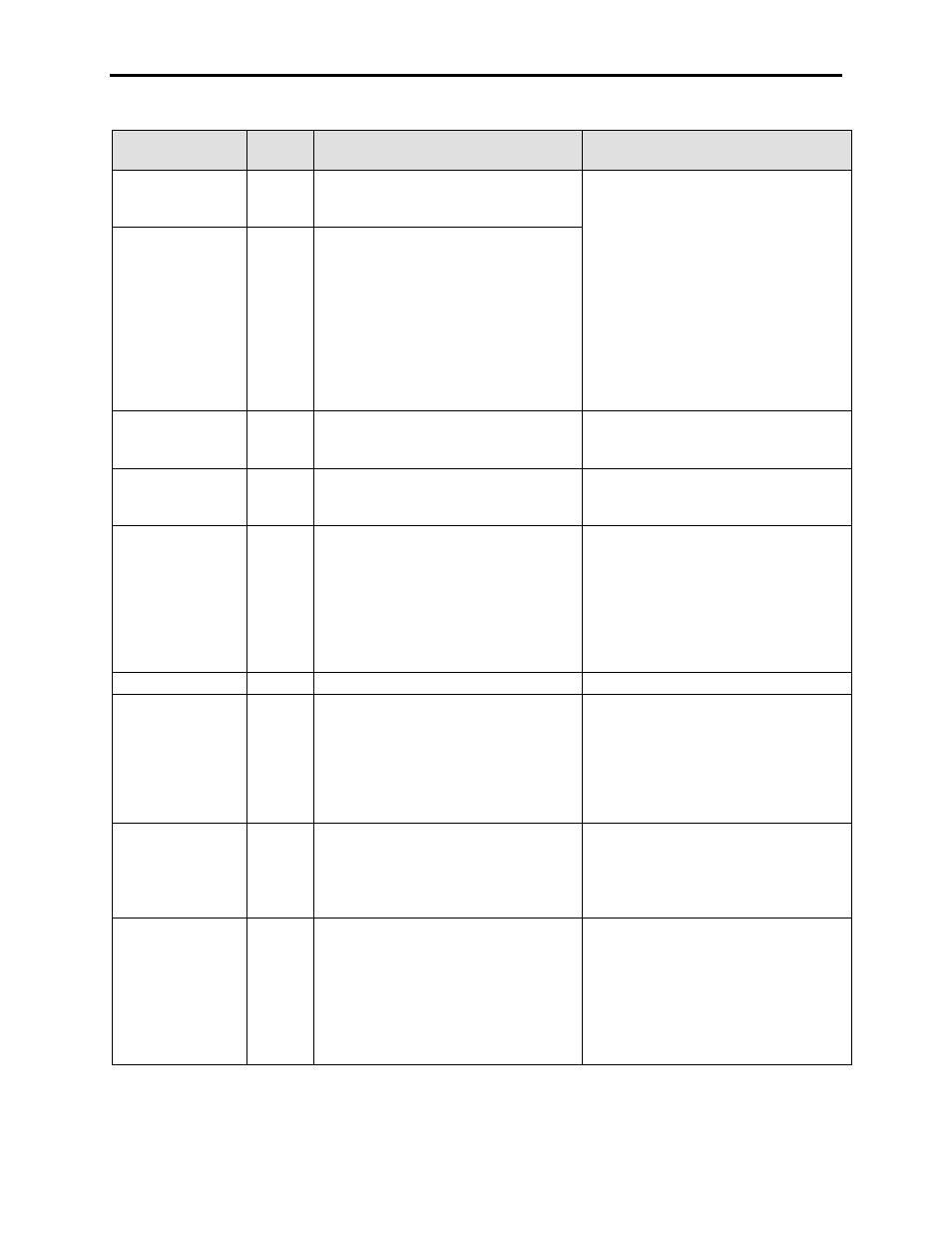
Troubleshooting
7-9
7000 “A” Frame
7000A-UM150F-EN-P – June 2013
FAULT
MESSAGE
FAULT
CODE
DESCRIPTION
RECOMMENDED ACTIONS
DI Iso Switch
29
The Drive Input Isolation Switch is in the
opposite state than expected, or the state
has changed during operation.
– Depending on the mode of operation
(Normal, System Test, Open-Circuit
Test, DC Current Test, or Open-Loop),
there are specific states for all the
possible system isolation switches (Refer
to the description of the Parameter 192 –
IsolSw/Ctctr Cfg in the parameters
manual)
– Ensure the isolation switches are in the
proper position
– Verify wiring feedback
– Verify isolation switch mechanical
auxiliary setup
DO Iso Switch
30
The Drive Output Isolation Switch is in the
opposite state than expected, or the state
has changed during operation.
OP Iso Switch
32
The System Output Isolation Switch is in the
opposite state than expected, or the state
has changed during operation.
BP Iso Switch
31
The Bypass Isolation Switch is in the
opposite state than expected, or the state
has changed during operation.
Drive OL
191
A Drive Overload condition has been
detected, where the overload condition is
calculated using DC Current Feedback
(P322) and an algorithm based on Drive
Overload Trip (P163) as the absolute trip
level, Drive Overload Delay (P164) as the
base trip delay, and Drive Overload Min
(P269) as initial detection level.
– Transient Loading – Check torque limit
and overload settings and compare
loading to torque settings and trip
settings
– Open Burden Resistor – Check Current
feedback and check the burden resistors
Dvc AK/Snubb
195
Device Anode-Cathode or Snubber fault
– NOT USED IN 5.xxxx
External 1-16
1-16
These are the optional additional External
Faults available when there is an additional
XIO board installed. This is configured with
XIO Ext Faults (P593), and this message
will appear if the specific input (1-16) is
configured in Fault Config as a Class 1 or
Class 2 fault.
– Review XIO Board Drawing:
– Identify source of Input from External
Fault XIO Board print and investigate the
cause of the fault
– Verify voltage signals from external
sources
Ext Cooling Loss
(C-Frame only)
224
The drive has detected the loss of the ability
to provide cooling for the drive. This is
detected through feedback from the Heat
Exchanger Cooling fans contactors and
overloads.
– Review the inputs to the drive Liquid
Cooling XIO and determine the source of
the missing signals
– Investigate the Heat Exchanger fans and
control for a cause
Field Loss
35
This fault indicates that the field current is
either missing or insufficient. This is done
through an indirect method by checking if
the drive is in Flux Regulator limit for the
delay set in Field Loss Delay (P559). This
means your exciter reference I Field
Command (P314) is at 100% for the time of
the delay.
– Verify the field current from the exciter is
present
– Verify the analog output from the drive is
reaching the field exciter control circuit