L6: torque detection, Refer to l6: torque detection on, L5-01: number of auto reset attempts – Yaskawa L1000E AC Drive Technical Manual for CIMR-LE Models for Elevator Applications User Manual
Page 222: L5-02: fault output operation during auto reset, L5-06: undervoltage fault reset selection, 8 l: protection functions
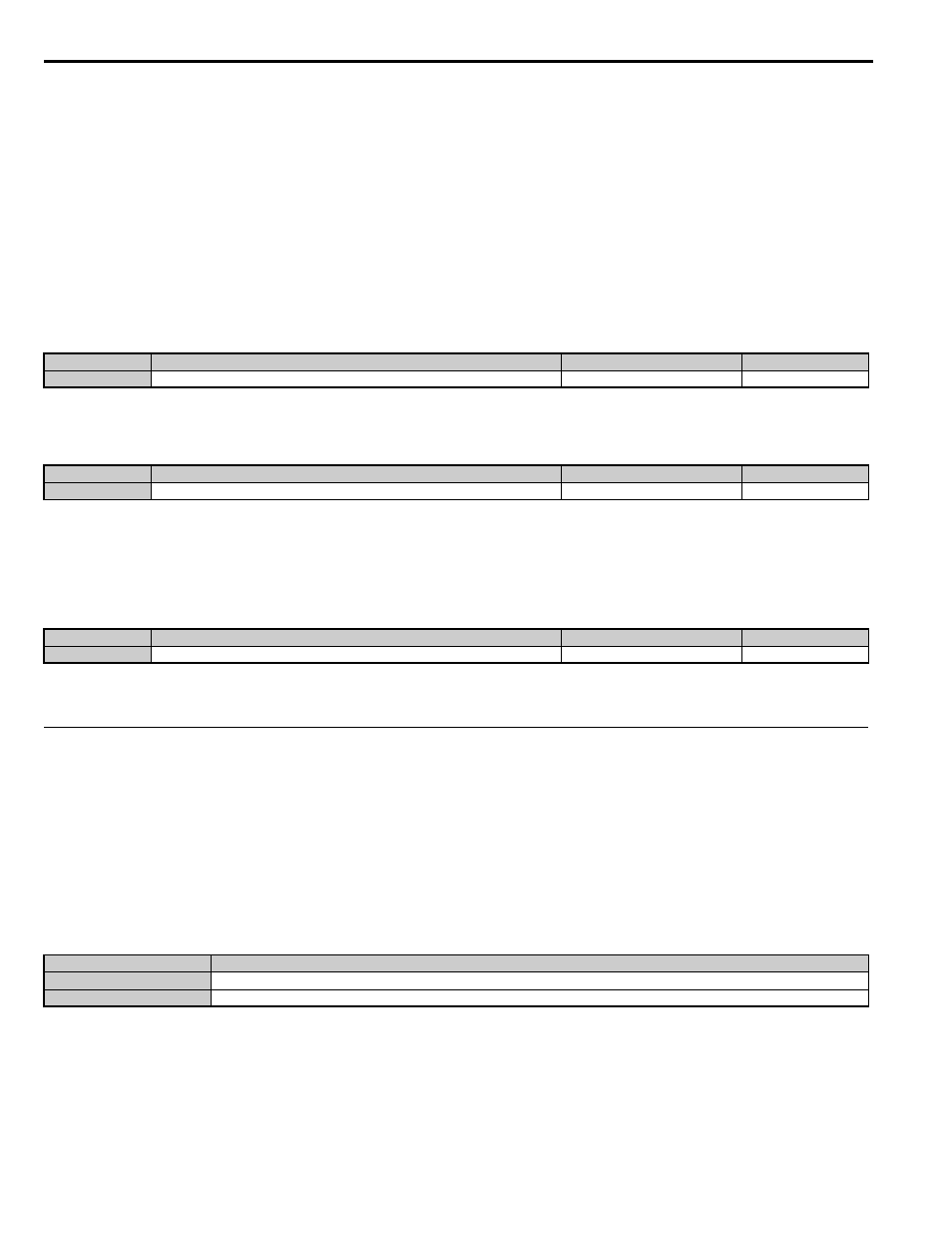
5.8 L: Protection Functions
222
YASKAWA ELECTRIC SIEP YAIL1E 01A YASKAWA AC Drive L1000E Technical Manual
■
L5-01: Number of Auto Reset Attempts
Sets the number of times that the drive may attempt to reset itself.
The drive will continuously attempt to reset. If it resets successfully, the reset counter is increased. This operation is
repeated each time a fault occurs.
When the counter reaches the number set in L5-01, the operation stops and the fault has to be reset manually after
correcting the cause.
The number of fault reset is reset to zero when:
• The drive operates normally for ten minutes following a fault reset.
• A fault is cleared manually after protective functions are triggered.
• The power supply is cycled.
■
L5-02: Fault Output Operation during Auto Reset
Determines if a fault output is triggered (H2- = E) when the drive attempts to reset.
Setting 0: No fault output
Setting 1: Fault output is set
■
L5-06: Undervoltage Fault Reset Selection
Determines whether a limit should be placed on the number of reset attempts after a Uv1 fault.
Setting 0: Restrict auto-reset attempts to L5-01 after Uv1
Setting 1: No limit on auto-reset attempts after Uv1
◆ L6: Torque Detection
The drive provides two independent torque detection functions that trigger an alarm or fault signal when the load is too
heavy (oL), or suddenly drops (UL). These functions are set up using the L6- parameters. Program the digital outputs
as shown below to indicate the underload or overload condition to an external device.
NOTICE: Damage to Equipment. Use the Torque Detection function of the drive to notify the PLC of potential overcurrent or overload
situations at the load prior to a drive overload fault. Failure to comply may cause the drive to fault with a coasting motor and potentially
damage equipment.
Note: When overtorque occurs in the application, the drive may stop due to overcurrent (oC) or overload (oL1). To prevent this, an
overload situation should be indicated to the controller before oC or oL1 occur in the drive. Use the torque detection for this
purpose.
show the function of overtorque and undertorque detection.
No.
Parameter Name
Setting Range
Default
L5-01
Number of Auto Reset Attempts
0 to 10 Times
0 Time
No.
Parameter Name
Setting Range
Default
L5-02
Fault Output Operation during Auto Reset
0 or 1
0
No.
Parameter Name
Setting Range
Default
L5-06
Undervoltage Fault Reset Selection
0 or 1
0
H2-01 through H2-05 Setting
Description
B
Torque detection 1, N.O. (output closes when overload or underload is detected)
18
Torque detection 2, N.O. (output close when overload or underload is detected)