INFICON STC-2002 Thin Film Deposition Controller Operating Manual User Manual
Page 39
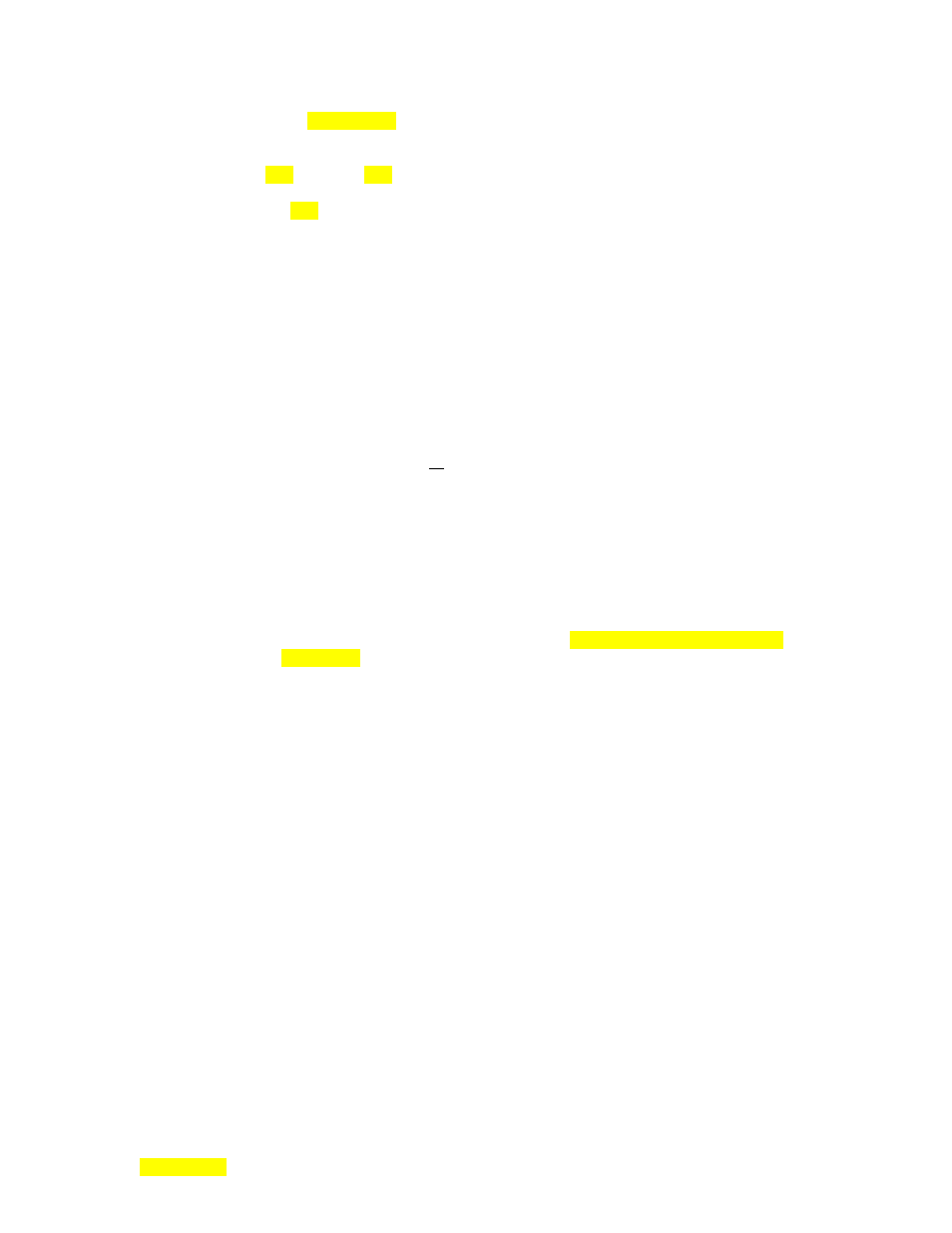
p STC-2002
DEPOSITION CONTROLLER
y
SECTION 2.XX
e page 37 of 276 ^
parameter of interest to be accessible and appropriately set.
Dependencies are also listed later in this
section.
There are some basic parameters that need to be setup. The Density and Z-Factor can be
obtained from table x4.1, in section x4.3 [Review Films menu]. Tooling [Review S
ource
S
ensor
Map
menu] for crystals can be determined empirically by running a trial deposition and using the equation (this
will be found in section x4.2):
Tooling = 100 X (Substrate Thickness / Displayed Thickness).
Generally, Tooling is greater than 100% when the sensor sees less deposited material than the substrate
(e.g. the sensor is further from the evaporant source than the crystal sensor). Generally, Tooling is less than
100% when the sensor sees more deposited material than the substrate (e.g. the sensor is closer to the
evaporant source than the crystal sensor). If 2 crystal sensors are used (assuming a single sensor card is
installed), Start Xtal (crystal) must match the hardware and positioning used. Obviously, the two crystal
sensors cannot occupy the same space. Therefore each crystal sensor will have a different tooling factor.
Crystal sensor tooling is coordinated by the sensor map menu that selects the sensor along with other sensor
properties. The channel specific applicable Review SS Map menu parameter is CHx Tooling. There is
also a Master Tooling parameter (Review SS Map Menu) that can be used change the ratio of all the crystal
sensors simultaneously in addition to the individual channel tooling. This can be thought of as a global
offset or multiplier used to alter the tooling of all active crystal sensors. In any case, the Tooling factor is
the attempt to describe the ratio of deposited material between the crystal sensor and the substrate.
Max Power Limit, Deposit Rate, Soak Power Value, Power Ramp Time, Power Soak Time,
Setpoint thickness and time limits need to be described. With these parameters entered, the Test mode
could be utilized to check the process behavior. The Max Power indicators show when the Max Power
parameter has been exceeded (LED blinks, LCD alternates with MAX!). To reiterate, the TEST mode only
effects the crystal sensor information being processed, it does not effect anything else (this includes the
control output voltages). This is not the point at which to begin experiments with a live system. This
section is meant to provide a discussion of the issues to familiarize the user with functional themes. Please
read further.
[
OK. Try these parameters while in the Test mode and with no external connections especially the
control output voltage unconnected: Max Power Limit:75%, Deposit Rate:3.7, Soak 1 Power Value:50%,
Power Ramp 1 Time:1:00, Power Soak 1 Time:1:00, Setpoint thickness limit:9.999 and time limit:1:11,
Data Plot Type:Power. With the above entered, and still in the Test mode, press the fixed front panel Start
key + touch key Reset / Start Proc in sequence three times. The assumption is made that factory defaults
are in effect. The Test mode is entered through the MENU, SERVICE, TEST OFF, ACCEPT keys. Film
parameter entry: fixed front panel Menu key + touch key Review Film.
]
.
informational only, no connections except power (see fig. 3.6, read or copy 3.1,3.2)
alternates: boat, srt-400, e-beam
.
When the STC-2002 sensor card control voltage output is connected to the evaporant power supply,
Review S
ource
S
ensor
Map parameters need to be selected for a proper interface (
SOURCE OUT CH
a
N
ne
L,
SOURCE FULL P
o
W
e
R, SOURCE MAX P
o
W
e
R
) and the Map itself needs to be selected by a Film parameter
(SS MAP SELECT). Following this, other power supply related parameters must also be contemplated.
Some thermal excitation alternatives include: electron beam: wire fed electron beam source, high vacuum
e-beam w/ small (~2cc) crucible, fixed pocket (large and small), rotary pocket indexers; resistive heater
sources: metal filament boats, coils, oxide crucibles (all for organic material deposition).
Crucible
capacities can range from a fraction of a cc to over 500cc.
The input control requirements of the high
current (or voltage) power supply should be found in the power supply documentation. Don't assume there
is a standard. With the STC-2002 control voltage output controlling the power supply for these thermal
sources (the 2
nd
control output voltage used for power supply control is typically employed for the recorder
function), the film parameters effecting power (processes depend upon films) are:
Soak 1 P
o
w
e
r
level
Value
0.0 to 100.0%
P
o
w
e
r Ramp 1 Time
(to pwr level)
0 to 99:59 MM:SS