INFICON STC-2002 Thin Film Deposition Controller Operating Manual User Manual
Page 30
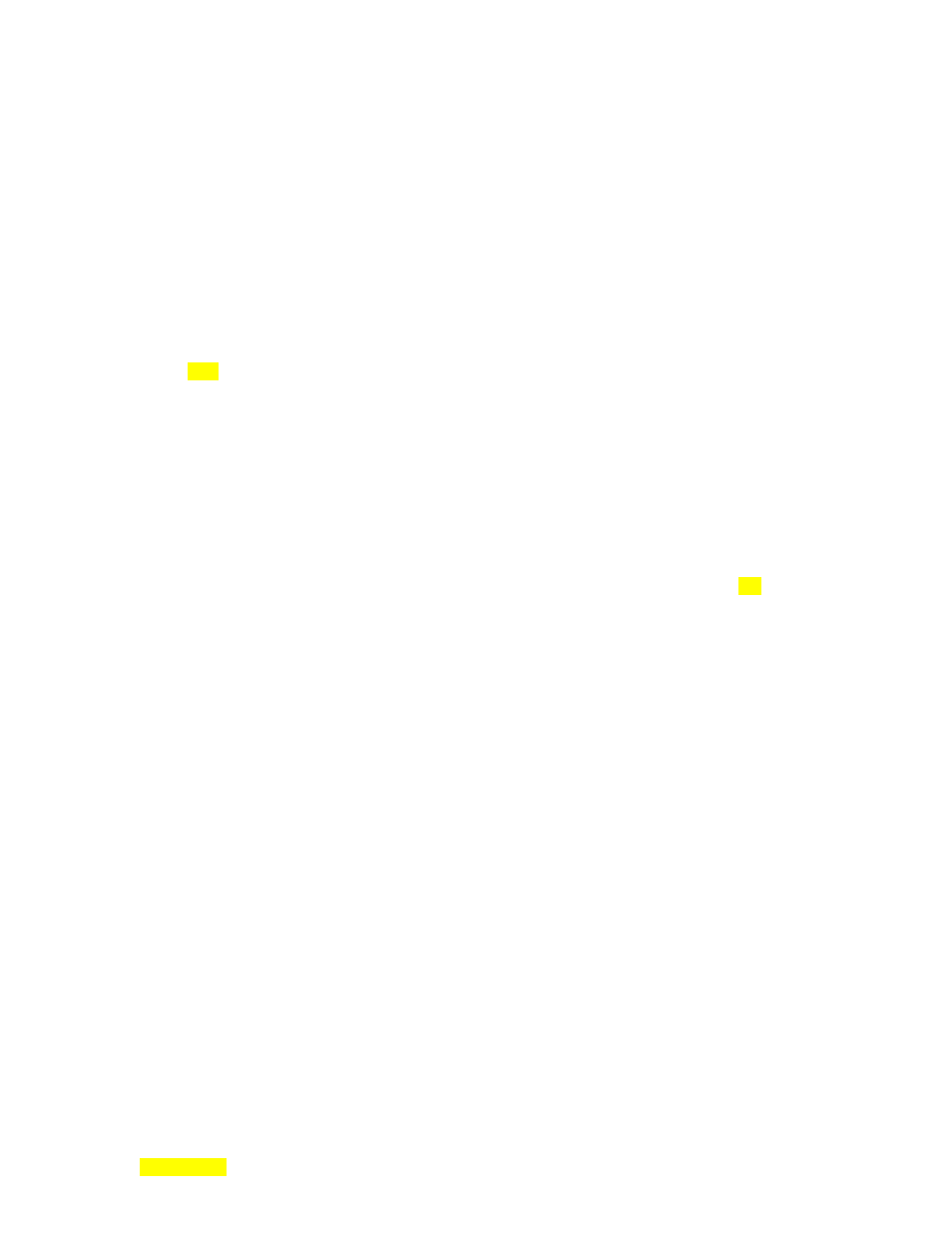
p STC-2002
DEPOSITION CONTROLLER
y
SECTION 2.XX
e page 28 of 276 ^
As the STC-2002 measures the rate of material deposition (in auto deposit mode), it compares this
measured value to a user programmed rate setting. If there is a difference between the actual rate and the
user programmed rate, the control voltage (from the sensor card) is used to generate a feedback to adjust
the deposition source power supply keeping it in compliance with the user programmed rate setpoint value.
This method of STC-2002 control has automatic compensation for changing source conditions.
Since there are many different types of deposition power supplies and sources in use today, the deposition
control voltage provided by the STC-2002 has been made user configurable: can be wired positive isolated
or negative isolated and menu scaled for 2.5, 5 or 10 volts full scale. The sense of the control loop can also
be set for either deposition or etching applications by menu programming.
To accommodate the extremely wide range of control loop responses required for the diverse deposition
sources available today, a P-I-D type of control loop has been implemented. With this type of control loop
available to the user, it should be possible to achieve very good control of any deposition source (see
section X3X).
All the control loop parameters interact to some degree in the overall response of the control loop resulting
in many combinations of settings that will give equally satisfactory results. Also, the control loop that is
optimized for steady state control will have quite different settings from one requiring fast control
acquisition with minimal overshoot. By supplying real time rate, rate deviation, or control power to the
graph on the STC-2002 RunTime display, determination of control loop settings and performance can be
made. By introducing a change into the control system and observing the graphical display responses, it is
quite easy to "tune" the control loop. Source response is another contributing control consideration.
Sources can be categorized as fast responding (electron beam), medium responding (resistive type boats,
baskets, or filaments), or slow responding (Knudsen or induction heated types). User programmable
shutter delay can also be used to achieve good deposition rate control before exposing substrates to the
evaporant stream. Refer to the I/O programming information later in this section and in section x5x of this
manual for a guide on selecting or implementing the logic used to control the substrate and/or sensor
shutter[s].
There are several phases during a deposition layer of the STC-2002 related to the source and deposition
rate control. There are three main parts to a deposition layer: pre-deposition, deposition control, and
post-deposition. The pre-deposition parameters control the source and material conditioning prior to the
film deposition. The STC-2002 can control a variety of different types of deposition sources. The typical
run cycle phases (rise/soak/rise/soak/shutter delay/deposit/rate ramp/deposit/idle ramp/idle) are for an
electron-beam, resistive element or other thermal source. There are also several film parameters (such as
DENSITY and Z FACTOR) and associated map parameters (TOOLING, WEIGHT) which relate to the
deposition material and sensor calibration. All of these issues will be described in greater detail later in this
manual.
.
<< co-dep 3-31 >>
.
Co-deposition is the running of 2 process layers simultaneously (2 materials, 2 evaporants, 1 or more
crystals for each of the 2 co-deposition processes). One of the 2 co-deposition processes will be designated
as the one with a final thickness parameter that will terminate the entire co-deposition process. The co-
deposition process without the final thickness parameter designation will have a parameter specifying its
percentage of the thickness rate of the other process. Another parameter unique to co-deposition is co-
deposition interaction which specifies quantitatively [by] how much each process contributes (is seen by) to
the other process (the other crystal sensor). Multiple material co-deposition is possible with additional
hardware (2
nd
set of LED/LCD displays) and different software that is described in a different manual.
.
<< multi-sensor dep >>
.
In addition to the typical configuration of 1 crystal sensor, 1 oscillator, 1 control voltage output, the STC-
2002 can utilize (by means of the 2
nd
sensor channel and optional sensor cards) multiple sensors to acquire
evaporant stream data at various locations, insuring greater repeatability of process control as well as better
process control (compensating for the vicissitudes of the evaporant stream in location and in time). A
number of user programmable parameters effect multiple sensor depositions. Review Source Sensor Map