Calibration frequency, Other quality assurance procedures – Teledyne 9110EH - Nitrogen Oxides Analyzer User Manual
Page 153
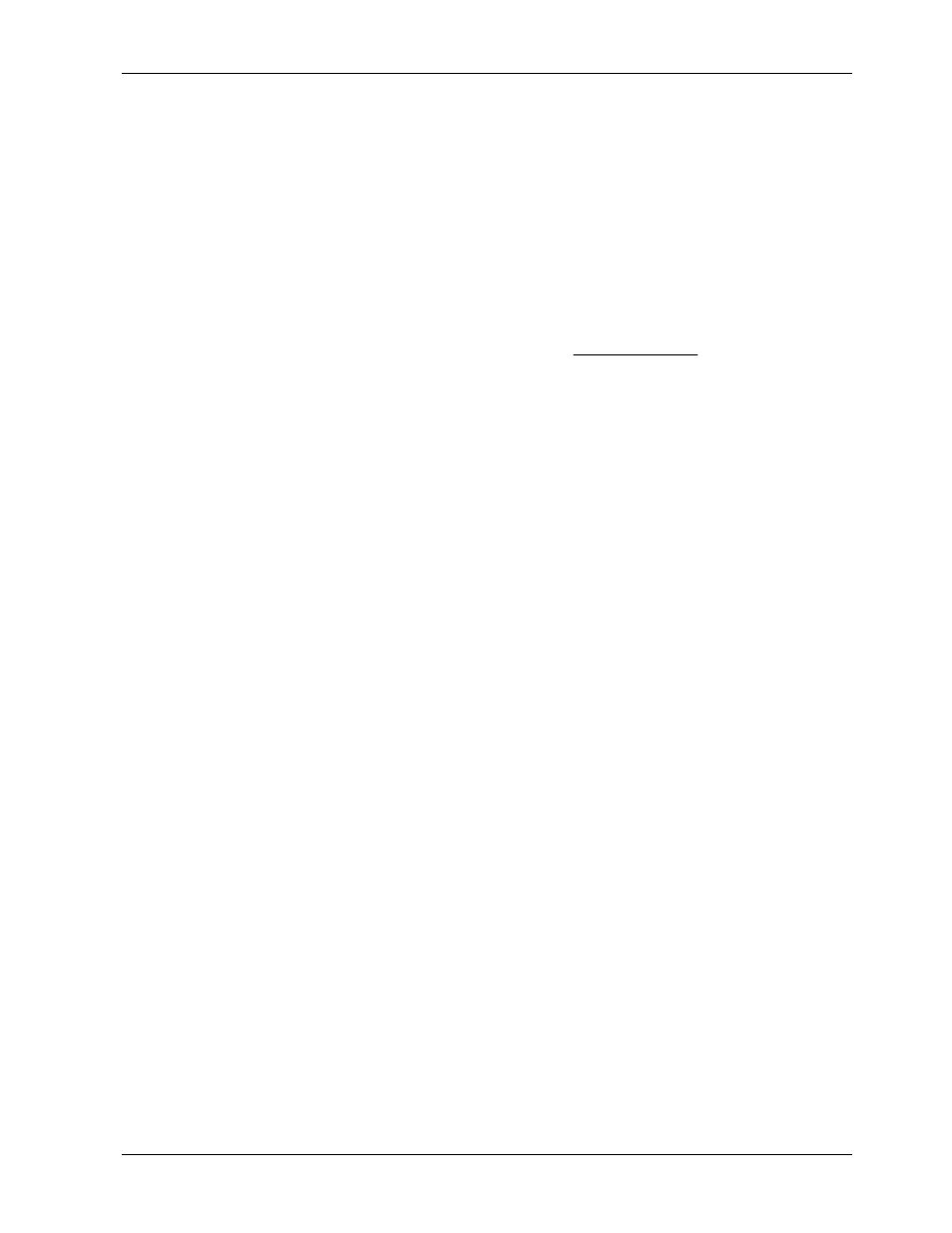
Model 9110EH Instruction Manual EPA Protocol Calibration
NO
2
CONVERTER EFFICIENCY
if the NO
X
reading should drop to less than 96% of its starting value during this step, it
indicates the NO
2
converter is in need of troubleshooting or replacement. See Chapter 11
for further details.
While maintaining all other conditions, adjust the ozone generator to obtain several other
concentrations of NO
2
evenly spaced between the 80% URL point and the zero point.
Record the NO, NO
X
, and NO
2
concentrations for each additional point.
Calculate the resulting NO
2
concentrations as follows:
F
]
NO
[
*
F
+
]
[NO
-
]
[NO
=
]
NO
[
T
IMP
2
NO
REM
ORIG
OUT
2
Eq 8-9
Where [NO]
ORIG
is the NO concentration before the GPT ozone is turned on, and [NO]
REM
is
the NO remaining after GPT.
Plot the NO
2
concentration output by the instrument on the y-axis against the generated
NO
2
[NO
2
]
OUT
on the x-axis. The plot should be a straight line within the ± 2% linearity
criteria given for the NO
x
and NO channels. If the plot is not linear the most likely cause is
that the converter needs replacing. See Section 7.1.7 on NO
2
converter efficiency.
8.4. Calibration Frequency
To ensure accurate measurements of the NO, NO
X
, and NO
2
concentrations, calibrate the
analyzer at the time of installation, and re-calibrate it:
• No later than three months after the most recent calibration or performance audit
which indicated analyzer calibration to be acceptable.
• An interruption of more than a few days in analyzer operation.
• Any repairs which might affect its calibration.
• Physical relocation of the analyzer.
• Any other indication (including excessive zero or span drift) of possible significant
inaccuracy of the analyzer.
Following any of the activities listed above, the zero and span should be checked to
determine if a calibration is necessary. If the analyzer zero and span drifts exceed the
calibration limits in Section 12 of the Q.A. Handbook
6
, a calibration should be performed.
8.5. Other Quality Assurance Procedures
Precision is determined by a one-point check at least once every two weeks. Accuracy is
determined by a three-point audit once each quarter.
Essential to quality assurance are scheduled checks for verifying the operational status of
the monitoring system. The operator should visit the site at least once each week. Every
two weeks a Level 1 zero and span check must be made on the analyzer. Level 2 zero and
span checks should be conducted at a frequency desired by the user. Definitions of these
terms are given in Table 8-3.
M9110EH Rev 0
139