Pid output fault, Sound from motor, Unstable motor speed when using pm – Yaskawa Z1000U User Manual
Page 226
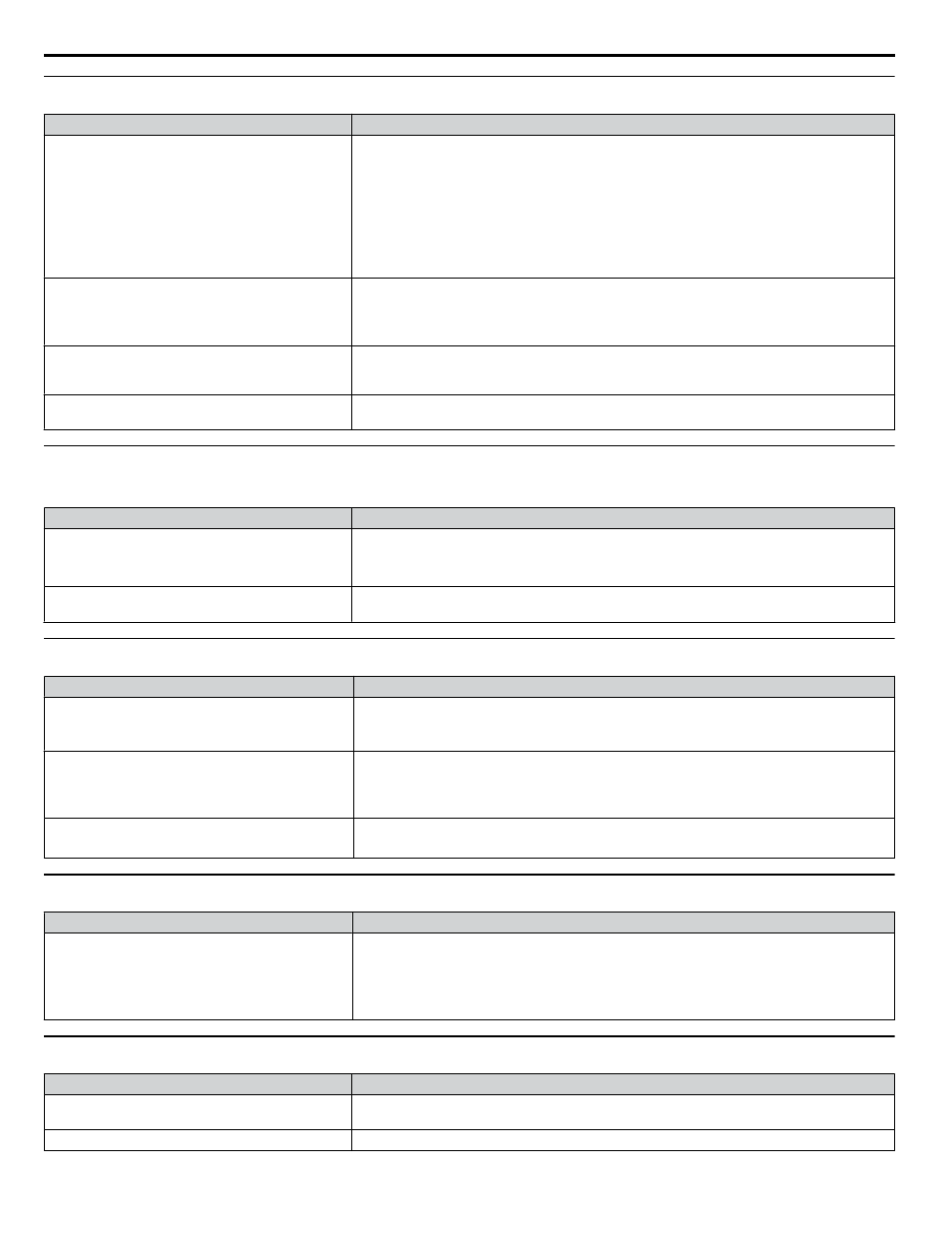
u
PID Output Fault
Cause
Possible Solutions
No PID feedback input.
• Check the multi-function analog input terminal settings.
• Set multi-function analog input terminal A1, A2, or A3 for PID feedback (H3-02, H3-10, or
H3-06 = B).
• A signal input to the terminal selection for PID feedback is needed.
• Check the connection of the feedback signal.
• Check the various PID-related parameter settings.
• No PID feedback input to the terminal causes the value detected to be 0, causing a PID fault
and the drive to operate at max frequency.
The level of detection and the target value do not
correspond with each other.
• PID control keeps the difference between target and detection values at 0. Set the input level
for the values relative to one another.
• Use analog input gains H3-03, H3-07, and H3-11 to adjust PID target and feedback signal
scaling.
Reverse drive output frequency and speed detection.
When output frequency rises, the sensor detects a
speed decrease.
Set PID output for reverse characteristics (b5-09 = 1).
Adjustment made to PID parameter settings are
insufficient.
Refer to b5: PID Control on page 259
for details.
u
Motor Rotates after the Drive Output is Shut Off (Motor Rotates During DC Injection
Braking)
Cause
Possible Solutions
DC Injection Braking is set too low and the drive
cannot decelerate properly.
• Adjust the DC Injection braking settings.
• Increase the current level for DC Injection Braking Current (b2-02).
• Increase the DC Injection Braking time at stop (b2-04).
The stopping method is set so that the drive coasts to
stop.
Set b1-03 (Stopping Method Selection) to 0 or 2.
u
Output Frequency is Not as High as Frequency Reference
Cause
Possible Solutions
Frequency reference is set within the range of the Jump
frequency.
• Adjust the parameters used for the Jump frequency function (d3-01, d3-02, d3-03).
• Enabling the Jump frequency prevents the drive from outputting the frequencies specified in
the Jump range.
Upper limit for the frequency reference has been
exceeded.
• Set the maximum output frequency and the upper limit for the frequency reference to more
appropriate values (E1-04, d2-01).
• The following calculation yields the upper value for the output frequency:
E1-04 x d2-01 / 100
Large load triggered Stall Prevention function during
acceleration.
• Reduce the load.
• Adjust the Stall Prevention level during acceleration (L3-02).
u
Sound from Motor
Cause
Possible Solutions
Exceeded 110% of the rated output current of the drive
while operating at low speeds.
• If the output current rises too high at low speeds, the carrier frequency is automatically reduced
and causes a whining or buzzing sound.
• If the sound is coming from the motor, disable carrier frequency derating (L8-38 = 0).
• Disabling the automatic carrier frequency derating increases the chances of an overload fault
(oL2). Switch to a larger capacity motor if oL2 faults occur too frequently.
u
Unstable Motor Speed when Using PM
Cause
Possible Solutions
Drive is attempting to operate the motor beyond the
speed control range listed in the specifications.
Check the speed control range and adjust the speed accordingly.
Motor hunting occurs.
Refer to Motor Performance Fine-Tuning on page 186
for details.
5.10 Troubleshooting without Fault Display
226
YASKAWA ELECTRIC TOEP C710636 10B Z1000U HVAC MATRIX Drive User Manual