Data blocks for system control, Data blocks for controlling ram (screw) position – Rockwell Automation 1771-QDC PLASTIC MOLD.MODULE User Manual
Page 70
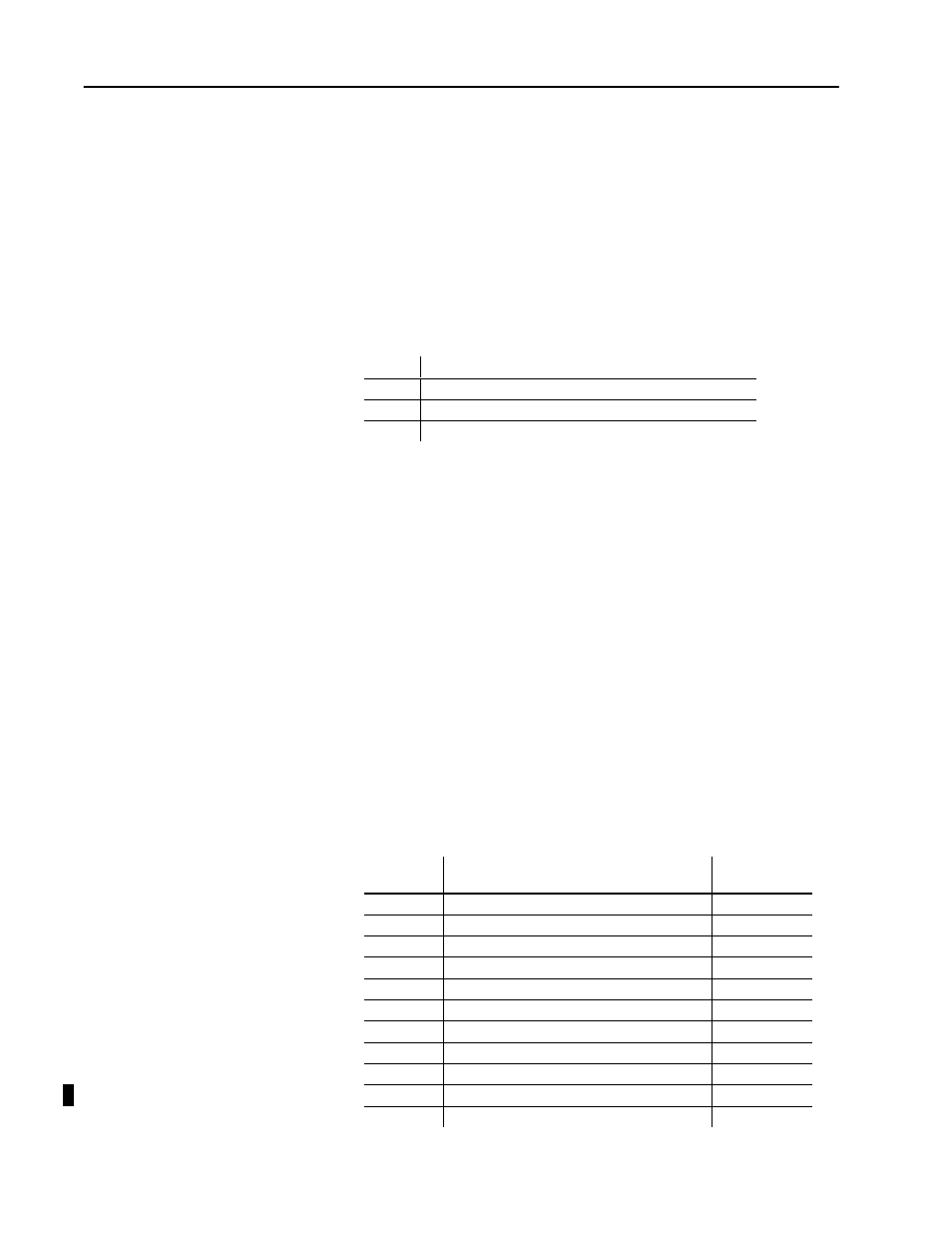
2–4
Command Word/Bit Descriptions
Publication 1771-6.5.88 – July 1997
Notes: 1. For [ ] engineering units, see page 3.
2. When using the Inject/Clamp/Eject mode, all pressure readings are system pressure at input 2, except where noted.
If you omit any of these three requirements, the QDC module rejects
some of the defined command blocks and inhibits some of the defined
status blocks because the module cannot use or generate block
parameters without data from a critical input which may have been
excluded during configuration. If you attempt to download an unusable
command block from the host processor, the QDC module treats it as
unrecognizable and discards the data. It does so in the same manner as
if it had received a command block containing an undefined Block ID.
Command Blocks for system level control are:
Block
Description
MCC
Module Configuration Command Block
JGC
Jog Configuration Command Block
DYC
Dynamic Command Block
You must establish the QDC module’s I/O configuration before it can
decide which command blocks to support. Although the module always
accepts the Module Configuration Command Block (MCC), the module
considers all other command blocks unrecognizable until it has received,
processed, and successfully error checked an MCC download from the
host processor. After you configure the QDC module with a valid MCC,
the module always accepts and processes (considers them recognizable)
either of the two basic command blocks JGC and DYC when received.
The module reports system status in the system status block (SYS). The
module can always return the System Status Block to the host processor.
It returns this block after each block transfer read (BTR) request from the
PLC processor unless the previous block transfer write (BTW) to the
module was a valid dynamic command block (DYC) containing a request
for some other status block.
The host processor can write any of these command blocks to the
QDC module to control ram (screw) position:
Command
Block
Description
Corresponding
Status Block
INC
Injection Configuration Block
–
IPC
Injection Profile Block
IPS
PKC
Pack Configuration Block
–
HDC
Hold Configuration Block
–
HPC
Pack/Hold Profile Block
HPS
PRC
Pre-decompression Configuration Block
–
PLC
Plastication Configuration Block
–
PPC
Plastication Profile Block
PPS
PSC
Post-decompression Configuration Block
–
PTC
Process Trace Configuration Block
PTS
RLC
Inject ERC Values Block
RLS
Data Blocks for System
Control
Data Blocks for
Controlling Ram (Screw)
Position