Certification of working standards, Precision check, Precision check procedure – Teledyne 9110E - Nitrogen Oxides Analyzer User Manual
Page 156
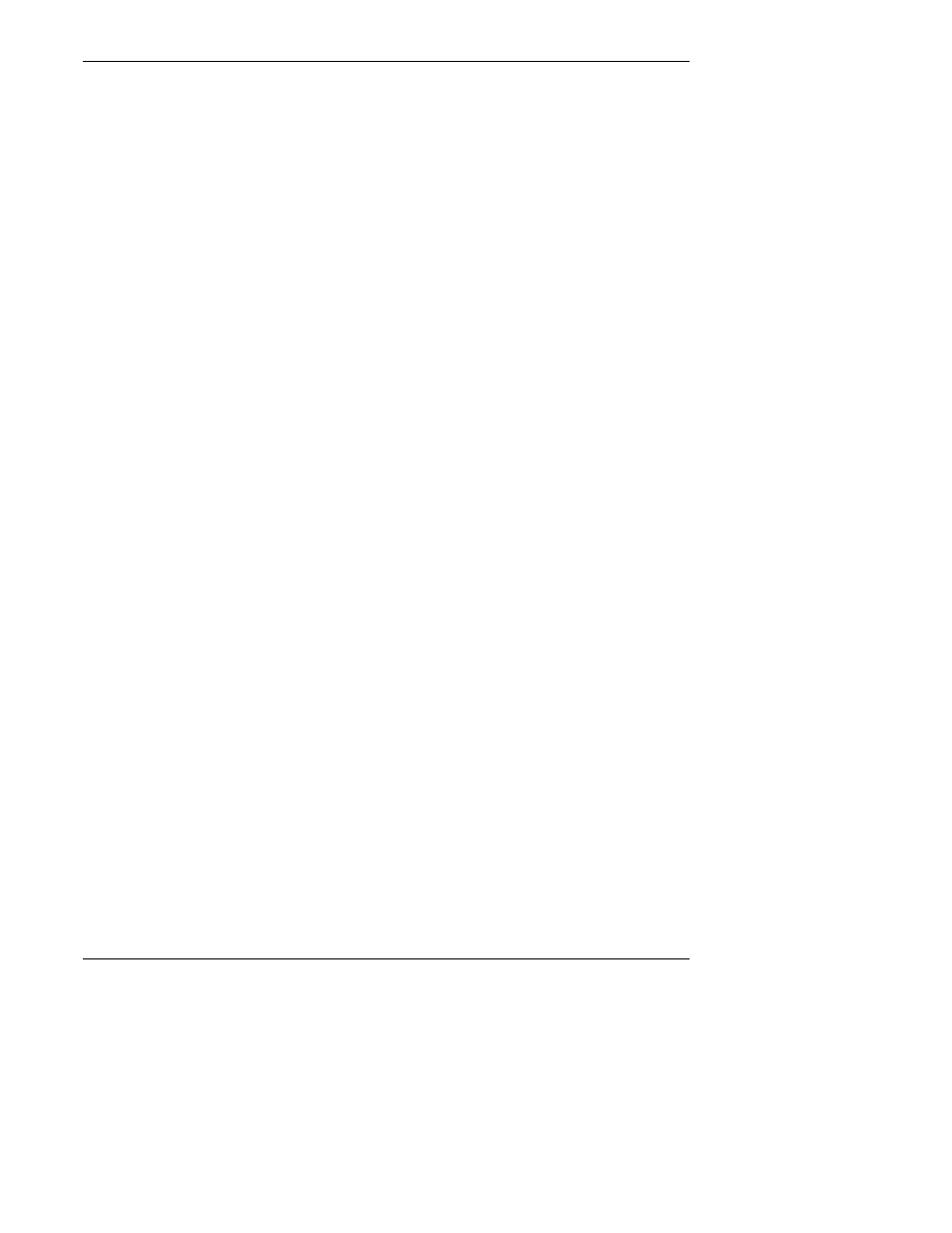
EPA Protocol Calibration
Model 9110E Instruction Manual
142
M9110E Rev B
• Automatic zero/span checks can be performed every night. See Section 7.8 of this
manual for setup and operation procedures.
• Zero/Span checks through remote contact closure can be initiated through remote
contact closures on the rear panel. See Section 7.7.3 of this manual.
• Zero/span checks can also be controlled through the RS-232 port. See Section 6.9 of
this manual for more details on setting up and using the analyzer’s RS-232 port.
8.7.2. Precision Check
A periodic check is used to assess the data for precision. A one-point precision check must
be carried out at least once every 2 weeks on each analyzer at an NO
2
concentration
between 0.08 and 0.10 ppm. The analyzer must be operated in its normal sampling mode,
and the precision test gas must pass through all filters, scrubbers, conditioners, and other
components used during normal ambient sampling. The standards from which precision
check test concentrations are obtained must be traceable to NIST-SRM. Those standards
used for calibration or auditing may be used.
8.7.3. Precision Check Procedure
Connect the analyzer to a precision gas that has an NO
2
concentration between 0.08 and
0.10 ppm. An NO
2
precision gas may be generated by either GPT or a NO
2
permeation tube.
If a precision check is made in conjunction with a zero/span check, it must be made prior to
any zero or span adjustments.
• Allow the analyzer to sample the precision gas until a stable trace is obtained.
• Record this value. NO and NO
X
precision checks should also be made if those data
are being reported. Information from the check procedure is used to assess the
precision of the monitoring data; see in Section 12 of the Q.A. Handbook
6
for
procedures for calculating and reporting precision.
8.8. Certification of Working Standards
The NO content of the NO working standard must be periodically assayed against NIST-
traceable NO or NO
2
standards. Any NO
2
impurity in the cylinder must also be assayed.
Certification of the NO working standard should be made on a quarterly basis or more
frequently, as required. Procedures are outlined below for certification against NO traceable
standard which is the simplest and most straightforward procedure.
To assure data of desired quality, two considerations are essential:
• The measurement process must be in statistical control at the time of the
measurement and;
• Any systematic errors, when combined with the random variation in the measure-
ment process, must result in a suitably small uncertainty.
Evidence of good quality data includes documentation of the quality control checks and the
independent audits of the measurement process by recording data on specific forms or on a
quality control chart and by using materials, instruments, and measurement procedures
that can be traced to appropriate standards of reference.