Dual loop control, Dual loop application description, Dual loop control configuration – Rockwell Automation 20G PowerFlex 750-Series AC Drives User Manual
Page 309
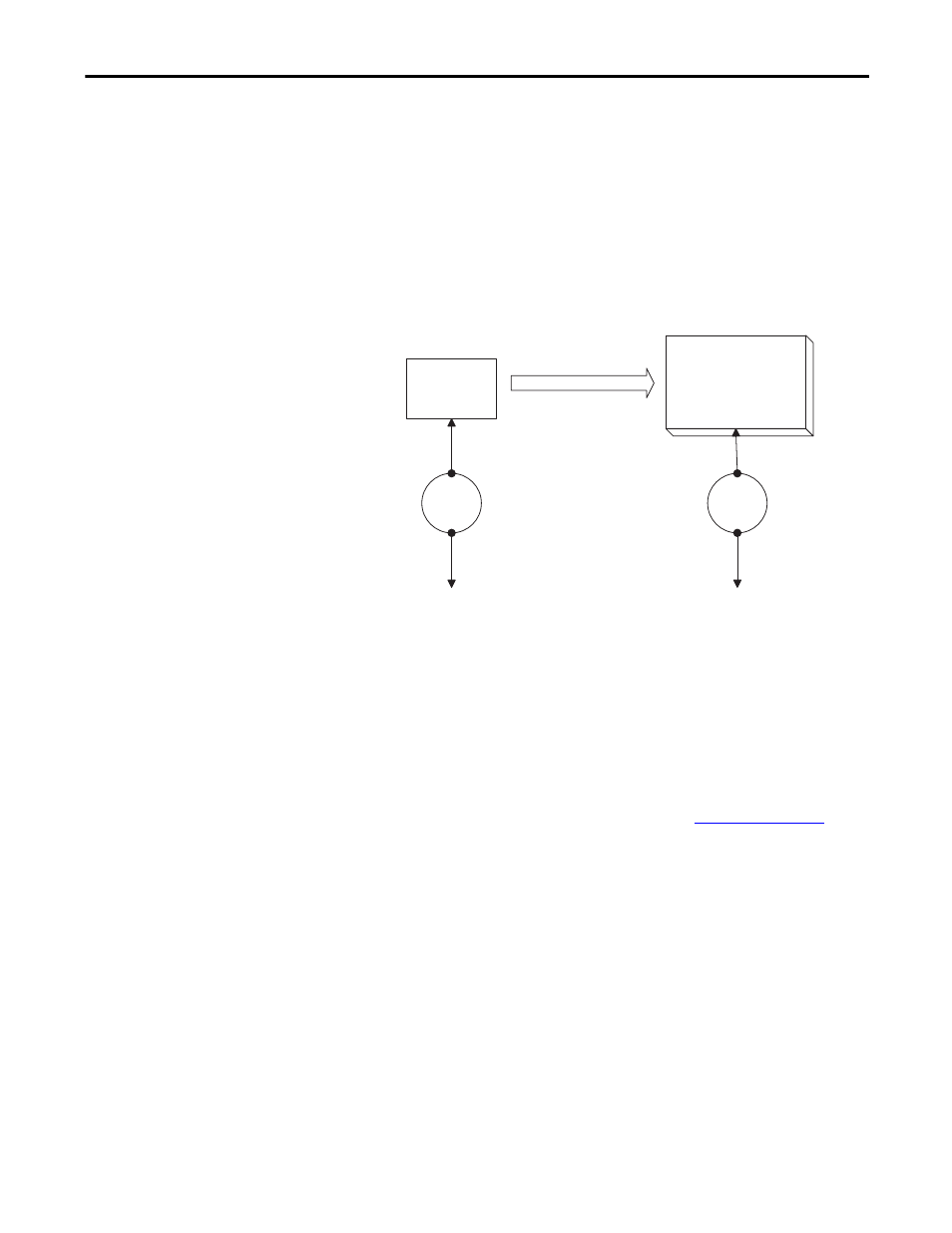
Rockwell Automation Publication 750-RM002B-EN-P - September 2013
309
Integrated Motion on the EtherNet/IP Network Applications for PowerFlex 755 AC Drives
Chapter 6
Dual Loop Control
This section explains how to configure a dual loop feedback application by using
Integrated Motion on the EtherNet/IP Network for a PowerFlex 755 drive.
Dual Loop Application Description
A dual loop control application uses two encoders, one mounted on the motor
(typical), and one mounted on the load (as depicted in this block diagram). The
two encoders are connected to the PowerFlex 755 drive via separate feedback
option modules, one installed in port 5, and another installed in port 4.
Dual Loop Control Configuration
These steps assume that you have created an axis for the PowerFlex 755 drive in
the Motion group and added a new PowerFlex 755 drive module in the Logix
Designer application. See the Integrated Motion on the EtherNet/IP Network
Configuration and Startup User Manual, publication
complete procedures. Follow these steps to configure the dual loop control
(encoder) axis.
1.
Create a feedback axis in the Motion group for the encoders
(Dual_Loop_Axis in this example).
E
E
Motor
Load
Mechanical Transmission
5:1 ratio
(Gearbox and Belt)
Motor/Master Feedback
Device - Port 5, Channel A
(PowerFlex 755 Drive)
Load Feedback Device -
Port 4, Channel A
(PowerFlex 755 Drive)