Rockwell Automation 20G PowerFlex 750-Series AC Drives User Manual
Page 206
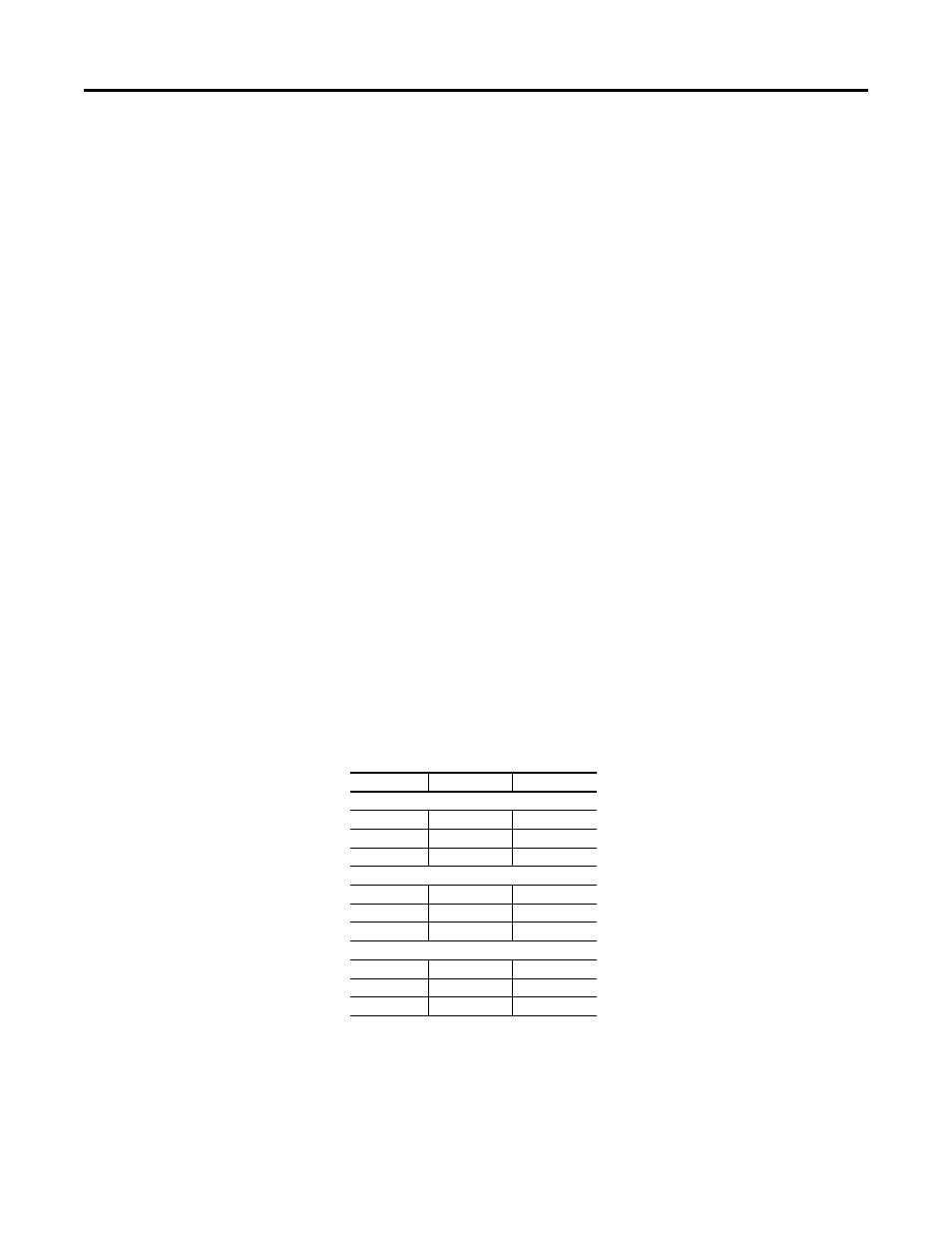
206
Rockwell Automation Publication 750-RM002B-EN-P - September 2013
Chapter 4
Motor Control
t
3
- t
2
= total time of deceleration from rated speed to 0 speed, in seconds
P
b
= peak braking power, watts (1.0 HP = 746 Watts)
Compare the peak braking power to that of the rated motor power, if the peak
braking power is greater that 1.5 times that of the motor, the deceleration time,
(t
3
- t
2
), needs to be increased so that the drive does not go into current limit. Use
1.5 times because the drive can handle 150% current maximum for 3 seconds.
Peak power can be reduced by the losses of the motor and inverter.
Step 3 – Calculating the Maximum Dynamic Brake Resistance Value
V
d
= The value of DC bus voltage that the chopper module regulates at and is
equal to 375V DC, 750V DC, or 937.5V DC
P
b
= The peak braking power calculated in Step 2
R
db1
= The maximum allowable value for the dynamic brake resistor
Choose a Dynamic Brake resistance value that is less than the value calculated in
Step 3. If the value is greater than the calculated value, the drive can trip on DC
bus overvoltage. Remember to account for resistor tolerances.
Step 4 – Choosing the correct Dynamic Brake Module
In the table above, choose the correct Dynamic Brake Module based upon the
resistance value being less than the maximum value of resistance calculated in
Step 3. If the Dynamic Brake Resistor value of one Dynamic Brake Module is not
sufficiently low, consider using up to three Dynamic Brake Modules in parallel,
such that the parallel Dynamic Brake resistance is less than Rdb1 calculated in
Cat. No.
Resistance
Wattage
240 Volt
KA005
28 ohms
666 watts
KA010
13.2 ohms
1650 watts
KA050
N/A
N/A
460 Volt
KB005
108 ohms
1500 watts
KB010
52.7 ohms
2063 watts
KB050
10.5 ohms
7000 watts
600 Volt
KC005
108 ohms
1500 watts
KC010
52.7 ohms
2063 watts
KC050
15.8 ohms
8000 watts
R
db1
V
2
d
P
b
-------
=