Pid algorithm, Pid algorithm -2 – Sensaphone SCADA 3000 Users manual User Manual
Page 210
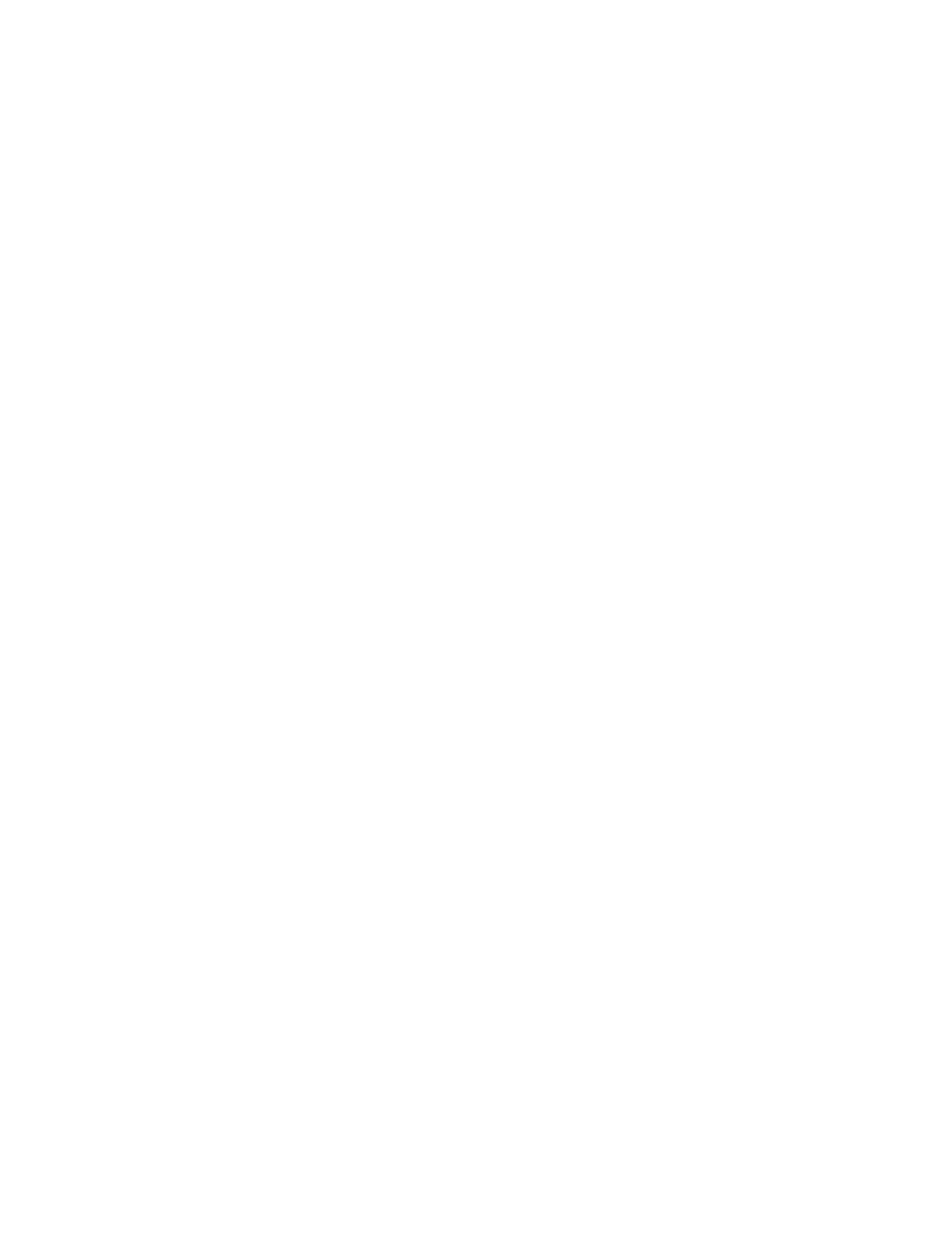
17-2
SCADA 3000 User’s Manual
• Dead Zone: This is the amount of variation that can be tolerated around the
Target Set Point. For example, if the you were trying to maintain a pressure
of 75 PSI +/- 10, you would enter a value of 10 for the Dead Zone. This will
permit the pressure to vary between 65 and 85 PSI without effecting any correc-
tion. Note that entering a value of 0 for the Dead Zone will cause the output to
change frequently, which may be undesirable with certain types of equipment.
Note: The PID Tuning factors below—Kp, Ki, Kd—must all be either constants
or UAF locations, and never a mix of the two.
• Kp factor: This is the proportional tuning factor used in the PID algorithm. It
may be either a constant or a UAF value.
• Ki factor: This is the integral tuning factor used in the PID algorithm. It may
be either a constant or a UAF value.
• Kd factor: This is the derivative tuning factor used in the PID algorithm. It may
be either a constant or a UAF value.
• Use Output Limits: Clicking this box will prevent the control output from
exceeding the programmed Min and Max parameters.
• Min: The minimum output level that will be computed if output limiting is
enabled.
• Max: The maximum output level that will be computed if output limiting is
enabled.
Output Limiting can be used to restrict the SCADA 3000’s ability to drive the process to its
extremes. The SCADA 3000 PID algorithm also includes Integral term limiting to prevent the
Integral from getting too large when the output reaches its limits. When Output Limiting is
enabled and the output reaches the Min or Max value, the algorithm stops calculating the inte-
gral sum until the output comes back in range. Similarly, when Output Limiting is not enabled,
the SCADA 3000 uses the output Table Low and Table High values to determine when to stop
calculating the integral sum. This method of limiting the integral term is sometimes referred to
as anti-reset windup.
Note that the Control Switch must be Enabled in order for the PID algorithms to run. In addi-
tion, the control switch can be programmed to turn all outputs OFF (including analog outputs)
when the switch is placed in the Disable position. See the section “Running and Stopping Ladder
Execution” in Chapter 15 for information on setting this option.
PID Algorithm
The most important and difficult part of programming a PID control process is setting the
PID tuning factors. These factors will determine when to adjust the output, how much to
adjust it by, and for how long. There are numerous articles and texts available that provide
detailed analysis on how to set these parameters. If you are new to setting up a PID control
process you may want to research this topic further. For our purposes we will cover the basic
concepts of PID tuning.
The PID algorithm is made up of three terms that are added together to produce an output.
The three terms are the proportional, integral and derivative terms.
Controller Output = Proportional + Integral + Derivative
Term
Term Term
The proportional term is computed by taking the difference between the current input value
and the set point (commonly referred to as the error) and multiplying it by the Proportional