Application examples – Lenze E82xVxxxKxxxxx User Manual
Page 511
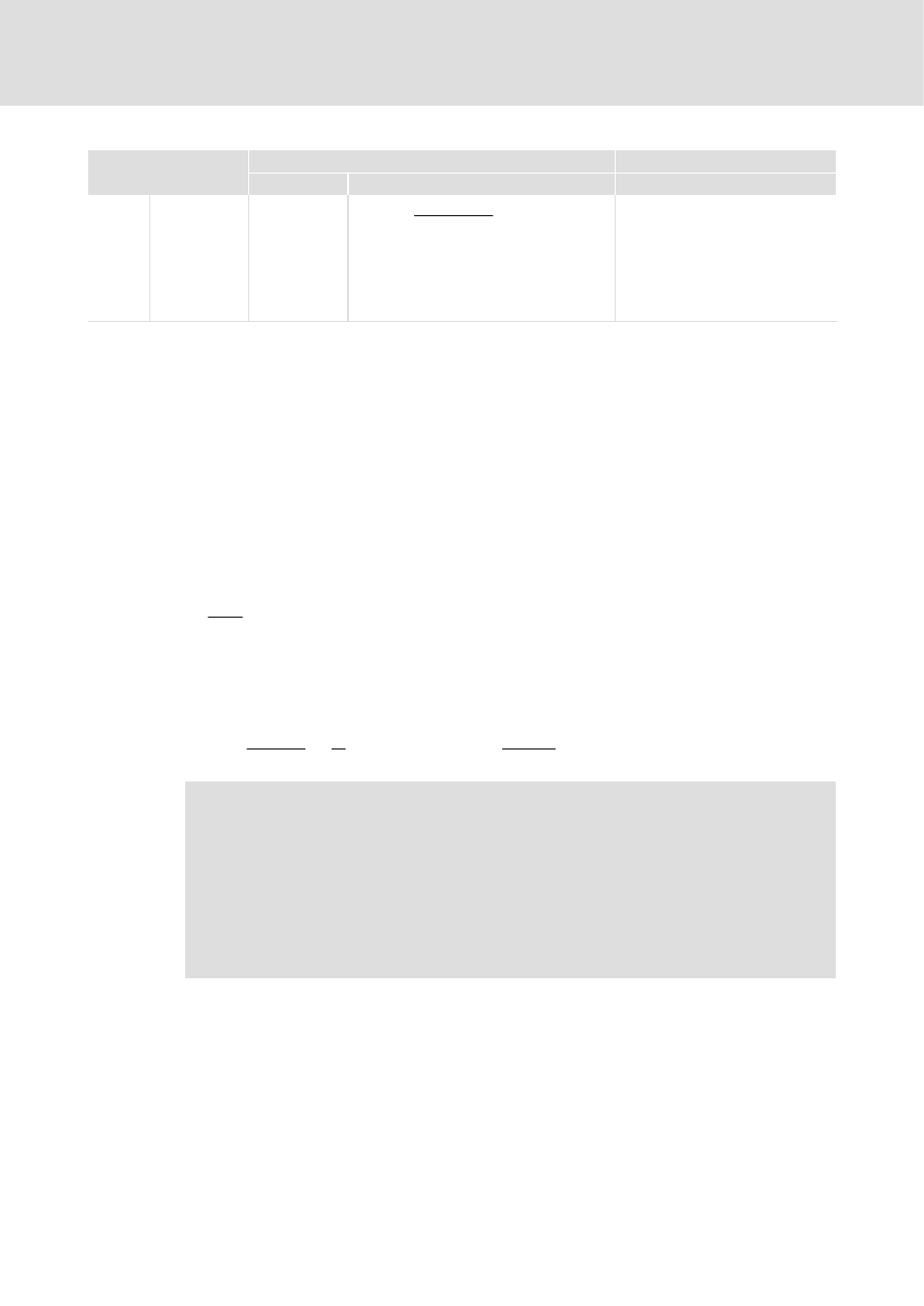
Application examples
Speed control
l
511
EDS82EV903 EN 3.0
IMPORTANT
Settings
Code
Meaning
Value
C0426 Frequency
input gain
X3/E1, X3/E2
(A)
(DFIN1−GAIN)
C0426 +
f
N
@ p
z @ (C0011 * f
s)
@ 100 %
l
f
N
= normalisation frequency from
C0425
l
p = number of motor pole pairs
l
z = number of encoder increments
l
C0011 = maximum output
frequency (corresponds to
maximum process motor speed)
l
f
s
= slip frequency
Adjustment (see example in Fig. 15−3)
Basic conditions
ƒ
A 4−pole motor is to be operated up to n
max
= 1500 rpm. The motor has the
following data:
– Rated speed n
r
= 1390 rpm
– Rated frequency f
rated
= 50 Hz
– Slip s
rated
= 7.3 %
– Slip frequency f
s
= 3.7 Hz
ƒ
The pulse encoder supplies 6 increments/revolution (inc/rev).
– Thus, the maximum frequency at X3/E1 with maximum speed amounts to:
1500
60 s @
6 + 150 Hz
ƒ
Set process controller influence (C0074) to 200% rated slip:
– C0074 = 14.6 %
ƒ
Calculate maximum output frequency (C0011):
ǒ
1 )
C0074 [%]
100
Ǔ
@
p
60 @
n
max
[min
*1
] + 1.15 @ 2 @ 1500
60
+ 57.5 Hz
)
Note!
If the number of increments per revolution of the encoder is not known,
determine the gain to be set by experiment:
ƒ
Set C0238 = 0 or 1.
ƒ
Accelerate the drive the maximum desired output frequency. The output
frequency is now only determined via the frequency feedforward control.
ƒ
Set the gain via C0426 so that the actual value (C0051) corresponds to the
setpoint (C0050).