Application examples – Lenze E82xVxxxKxxxxx User Manual
Page 506
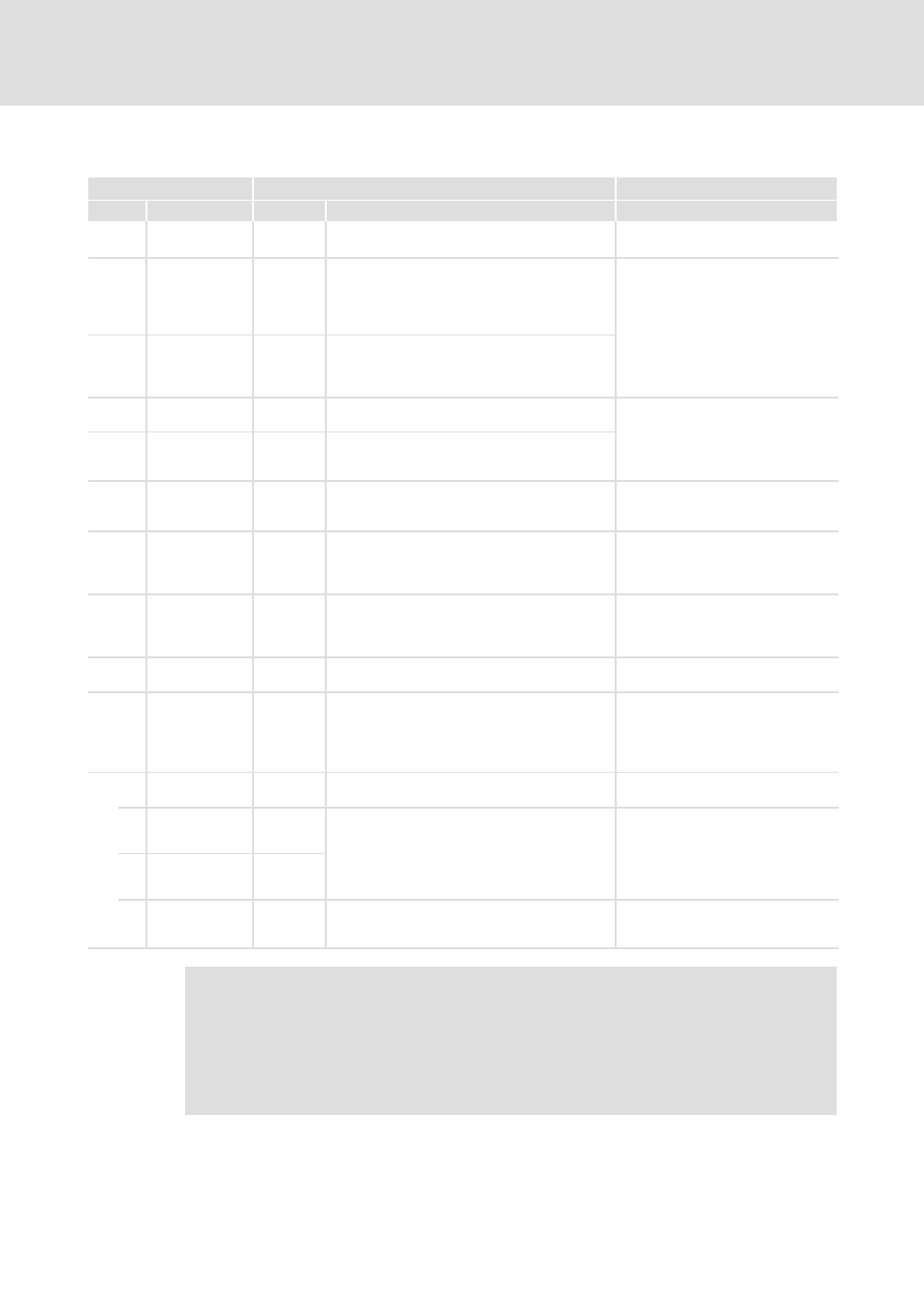
Application examples
Pressure control
Example 2: Simple pressure control with changeable setpoint selection
l
506
EDS82EV903 EN 3.0
Application−specific configuration
Code
Settings
IMPORTANT
No.
Name
Value
Meaning
C0014 Operating mode
3
V/f characteristic control V
~f
2
square−law characteristic with
constant V
min
boost
C0019 Operating
threshold −
automatic DC
injection brake
(auto DCB)
0
Automatic DC injection brake is deactivated
If the lower frequency limitation is
activated (C0239) or if C0181 is used
as controller setpoint (C0145), the
automatic DC injection brake must
be deactivated!
C0106 Hold time −
automatic DC
injection brake
(auto DCB)
0
Automatic DC injection brake is deactivated
C0070 Process
controller gain
1.00
Lenze default
setting
Adapt to process, if required.
à
Further information:
^ 318 ff.
C0071 Process
controller reset
time
100
Lenze default
setting
C0074 Influence of the
process
controller
100.0
0.0
{0.1 %}
100.0
C0145 Source of
process
controller
setpoint
0
Overall setpoint (PCTRL1−SET3)
Setpoint = NSET1−NOUT +
PCTRL1−NADD
(Main setpoint + additional setpoint)
C0181 Process
controller
setpoint 2
(PCTRL1−SET2)
−650.00
{0.02
Hz}
650.0
C0238 Frequency
precontrol
0
No feedforward control (only process controller)
Process controller has full influence.
C0239 Lower frequency
limitation
³ 0
Prevent reversed rotation
The value does not fall below the
limit independently of the setpoint.
Automatic DC injection brake (auto
DCB) must be deactivated with
C0019 = 0 or C0106 = 0
C0412
Linking analog signal sources to internal analog
signals
1 Setpoint 1
(NSET1-N1)
255
fixed free (disconnect from analog input)
The analog input of the standard I/O
(AIN1) is linked factory−set to the
speed feedforward control. This
connection must be separated so
that the input can be used for the
analog actual value (C0412/5).
2 Setpoint 2
(NSET1-N2)
255
5 Actual process
controller value
(PCTRL1−ACT)
1
Analog input X3/8 of the standard I/O
Actual pressure value
)
Note!
ƒ
The motor potentiometer in connection with the standard I/O may only be
linked with the signals NSET1−N1, NSET1−N2 or PCTRL1−NADD. The linkage
with other signals would cause a setpoint step−change.
ƒ
When selecting the setpoint via the motor potentiometer, we recommend
the acceleration and deceleration times
³ 5s (C0220, C0221).