Table 11 - overload (thermal model) settings – Rockwell Automation 825-P Modular Protection System for Motors User Manual User Manual
Page 71
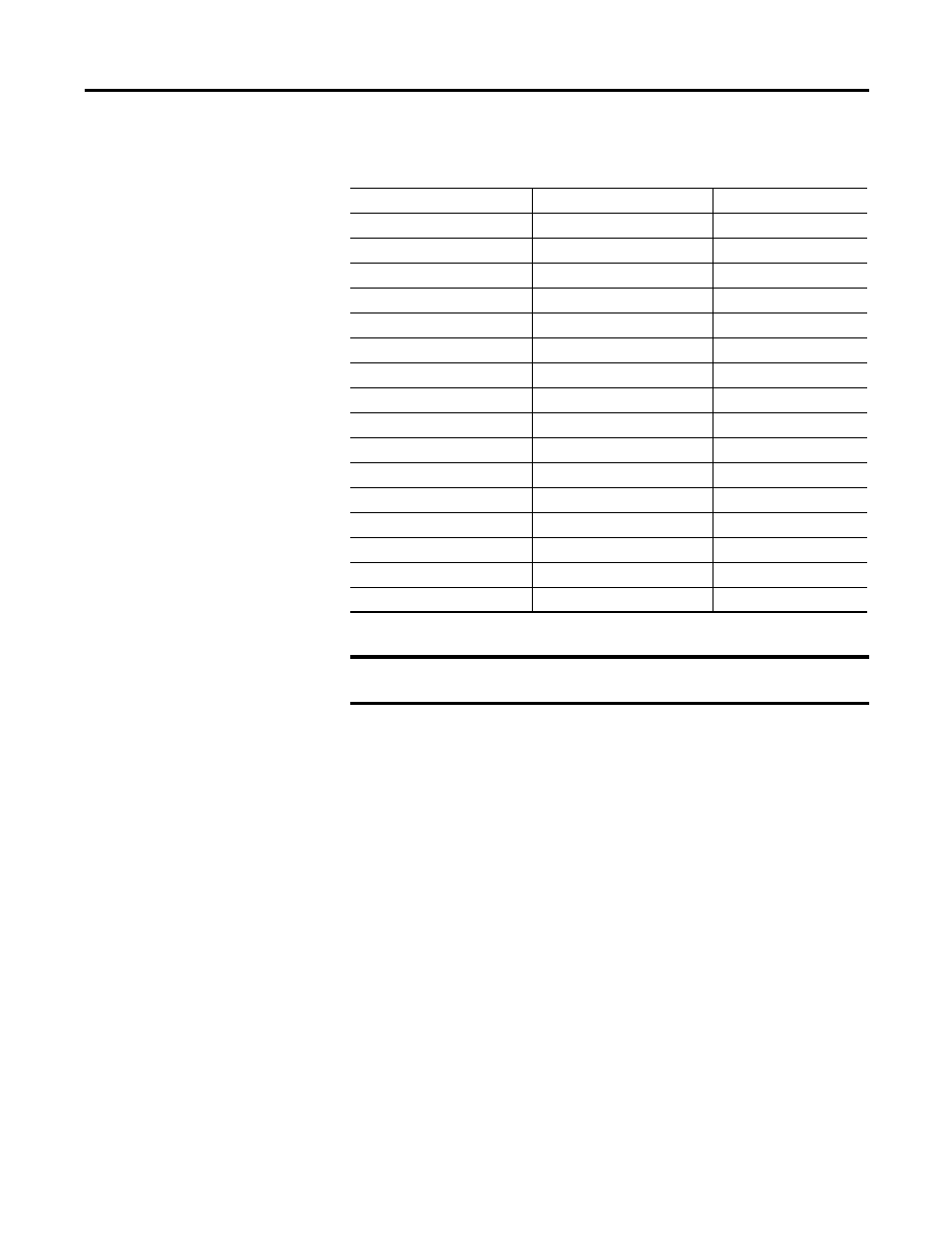
Rockwell Automation Publication 825-UM004D-EN-P - November 2012
71
Configuring Protection & Logic Functions Chapter 6
When you enable overload protection, the relay requests information about the
protected motor capabilities. Obtain the requested information (except the
acceleration factor) from the motor specifications.
The 825-P thermal element always operates in one of two modes: starting or
running. In starting mode, the thermal element trips in Locked Rotor Time
at Locked Rotor Current whether the motor is at ambient or at normal operating
temperature. In running mode, the thermal element provides overload protection
by limiting the motor heat energy estimate to a value represented by the overload
settings.
The locked rotor time setting is for a hot motor condition. If only one locked
rotor time is specified for a particular motor, unless the specification states
otherwise, assume the time is the cold locked rotor time. Multiply the cold locked
rotor time by 0.833 to determine a hot locked rotor time which is acceptable
for most motors.
Table 11 - Overload (Thermal Model) Settings
Setting Prompt
Setting Range
Factory Default
OVERLOAD ENABLE
Y, N
Y
OL RESET MODE
Man, Auto
Man
OL RESET LEVEL
10…99%TCU
75
SERVICE FACTOR
1.01…1.50
1.01
MOTOR LRC
2.5…12.0 x
I
e
6.0
LOCKD ROTOR TIME
1.0…600.0 s
10.0
ACCEL FACTOR
0.10…1.50
1.00
RUN STATE TIME K
Auto, 1…2000 min
Auto
MOTOR LRC–2nd
2.5…12.0 x
I
e
6.0
MOTOR LRT–2nd
1.0…600.0 s
10.0
ACCEL FACT–2nd
0.10…1.50
1.00
RUN ST TC–2nd
Auto, 1…2000 min
Auto
OL WARN LEVEL
Off, 50…99%TCU
85
START INH. LEVEL
Off, 1…99%TCU
Off
STOP COOL TIME
1…2200 min
18
OL RTD BIASING
Y, N
N
IMPORTANT
For compliance to IEC standards regarding thermal overload protection, set the
SERVICE FACTOR to a value: 1.05…1.20.
NOTE:
When Two Speed Enable = Y and a Speed 2 control input is specified, the relay uses the
“2nd” FLA-related settings for the overload thermal model