INFICON IC/5 Thin Film Deposition Controller User Manual
Page 100
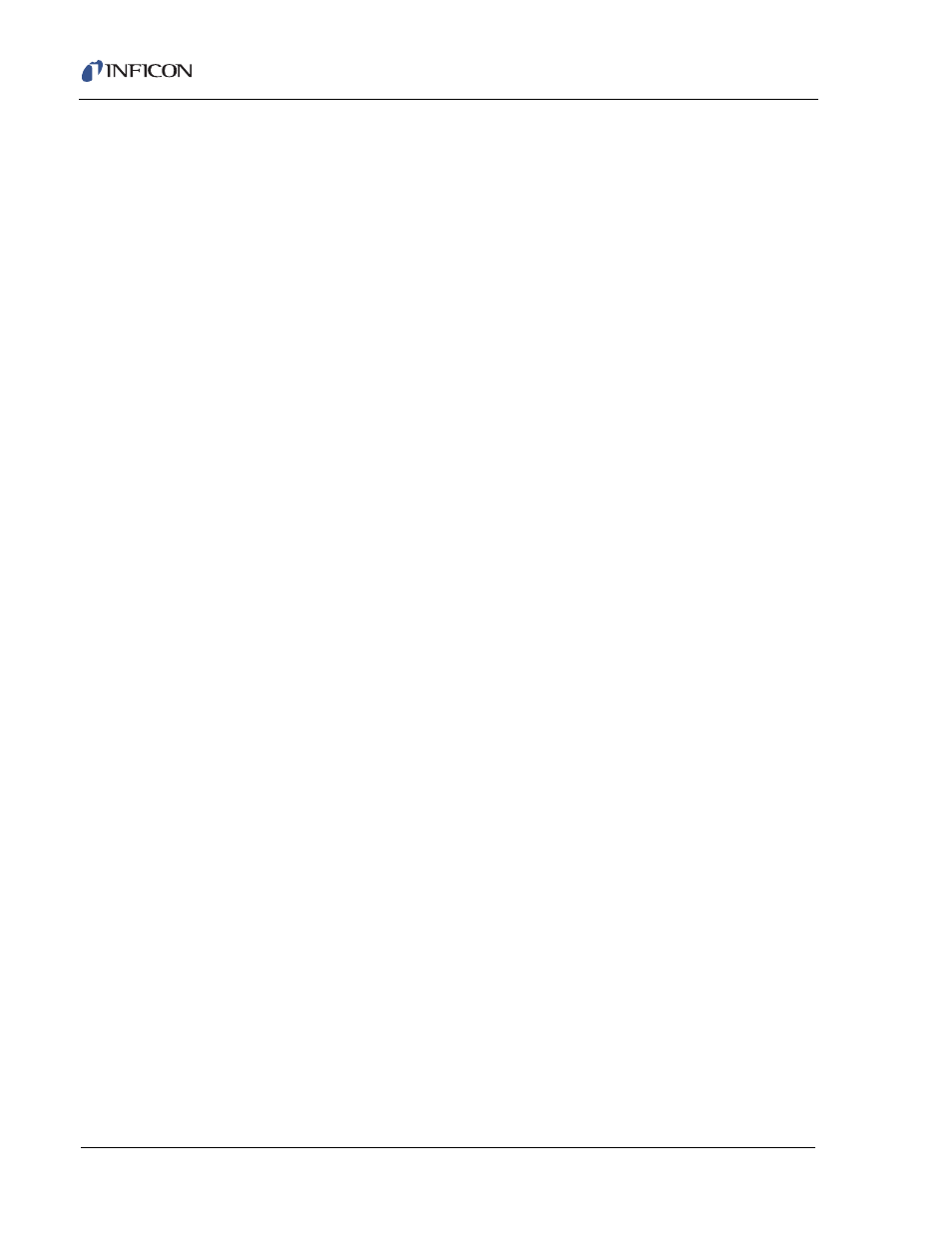
4 - 6
IP
N 07
4-
23
7A
E
IC/5 Operating Manual
PROCESS GAIN . . . . . . . . . . . . . . . 0.01 to 99.999 Å/sec/% pwr
This parameter determines the change in % Power for a given rate deviation
(dRate/dPower). The larger the process gain value, the smaller the change in
power for a given rate error. Values range from 0.01 to 99.999. The default
value is 10.00.
PRIMARY TIME CONSTANT . . . . . 0.010 to 999.999 sec
This is the evaporation source’s time constant. This value is defined as the time
difference between the actual start of a change in rate and the time at which
63% of the rate step is achieved. This value may be measured according to the
above criterion or it may be determined empirically. Values range from 0.010 to
999.999 seconds. The default value is 1. This parameter is disabled if the
CONTROL LOOP option parameter is set to 0.
SYSTEM DEAD TIME . . . . . . . . . . . 0.010 to 999.999 sec
This value is defined as the time difference between a change in % power and
the start of an actual change in rate. Values range from 0.010 to 999.999
seconds. The default value is 1.0. This parameter is disabled if the CONTROL
LOOP option parameter is set to 0.
MASTER TOOLING. . . . . . . . . . . . . 10.0 to 400.0%
This is a correction factor used for correlating the aggregate rate and thickness
accumulation on the crystal with the thickness accumulation on the substrate.
This thickness difference is due to the geometric distribution of material flux
from the source.
The tooling factor is calculated using the equation
[1]
where TF
i
= Initial Tooling Factor, T
m
= Actual Thickness at the Substrate, and
T
x
= Thickness on the Crystal.
Values range from 10.0 to 400.0%. The default value is 100%.
If the MASTER TOOLING parameter is changed, the new MASTER TOOLING
value is used for subsequent calculation of the individual as well as aggregate
rate and thickness. Also, the aggregate thickness and each sensor’s thickness
accumulated thus far will be re-scaled based on the change to the MASTER
TOOLING.
For single sensor applications, this is the recommended parameter to use to
get agreement between sensor and substrate thicknesses. The sensor tooling
should be left at 100%. For multiple sensor applications, the sensor tooling
factors should first be adjusted so all sensors read the same rate. Next, adjust
the MASTER TOOLING to get agreement between the thickness measured by
the IC/5 and the thickness measured at the substrates.
TOOLING
TF
i
T
m
T
x
=