2) warning display and troubleshooting, 19 (2) warning display and troubleshooting – Yaskawa SGDS Sigma III Servo Amplifier User Manual
Page 308
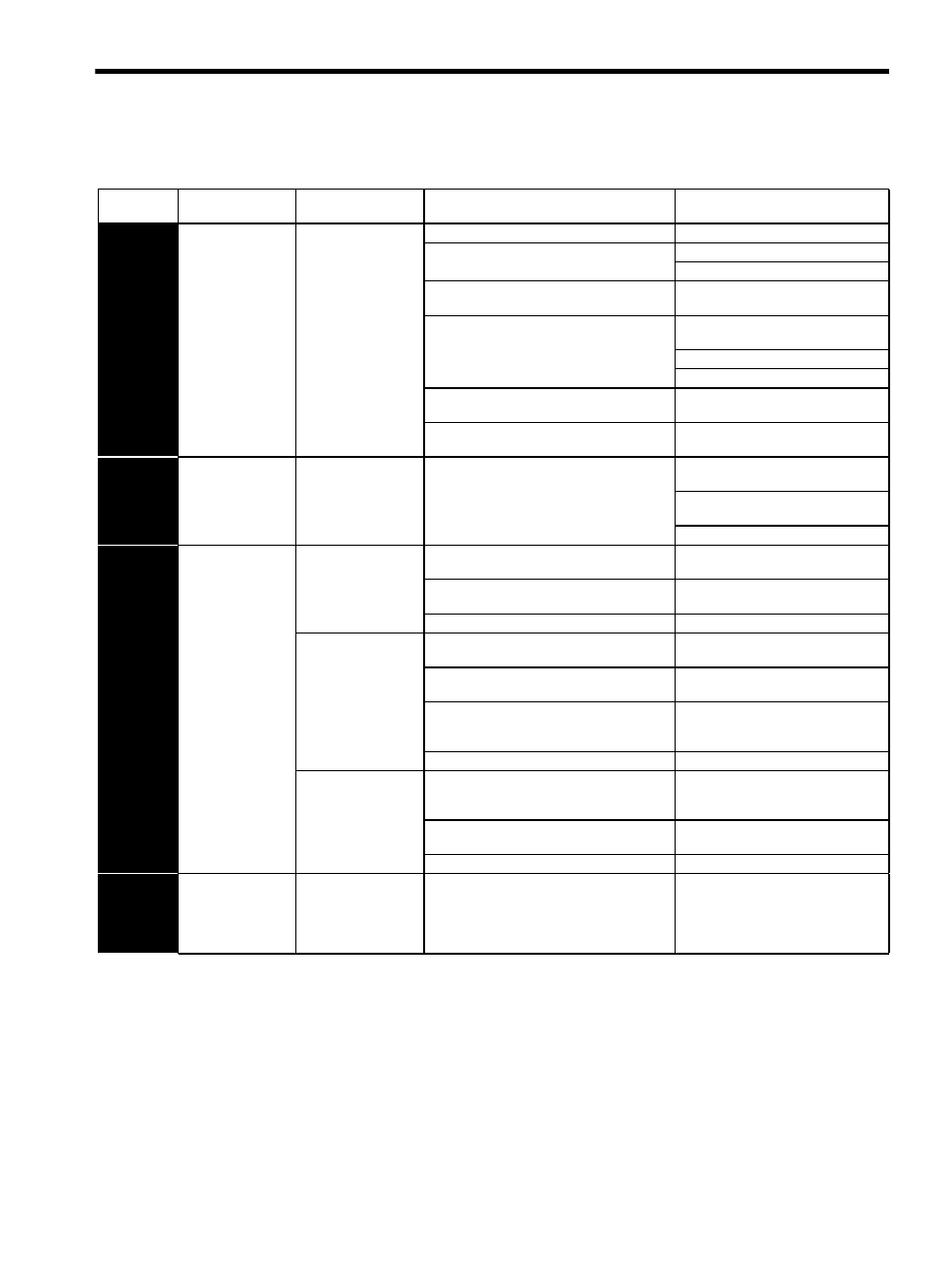
10.1 Troubleshooting
10-19
(2) Warning Display and Troubleshooting
Table 10.4 Warning Display and Troubleshooting
Warning
Display
Warning Name
Situation at Warning
Occurrence
Cause
Corrective Actions
A.900
Position Error
Pulse Overflow
Occurred during
operation.
A SERVOPACK board fault occurred.
Replace the SERVOPACK.
Wiring is incorrect or the contact of servomotor
U, V, and W is faulty.
Correct the servomotor wiring.
Correct the encoder wiring.
The SERVOPACK gain adjustment is improper.
Increase the speed loop gain (Pn100) and
position loop gain (Pn102).
The position reference pulse frequency is too
high.
Decrease slowly the position reference
pulse frequency.
Apply the smoothing function.
Adjust the electronic gear ratio.
Setting of the parameter Pn520 (Position Error
Pulse Alarm Level) is improper.
Set the parameter Pn520 to a value other
than “0”.
The servomotor specifications do not meet the
load conditions (torque, moment of inertia).
Reconsider and correct the load and
servomotor capacity.
A.901
Position Error
Pulse Overflow at
Servo ON
Occurs when the servo
was ON.
• Errors accumulated excessively in servo OFF
status
• With the setting not to clear the errors while the
servo is OFF, the servomotor was running.
Do not run the servomotor in servo OFF
status.
Make the setting so that the errors are
cleared in servo OFF status.
Adjust the detection level.
A.910
Overload:
Warning for the
alarms A710 and
A720
Occurs when the servo
was ON.
Wiring is incorrect and the contact in servomotor
wiring is faulty.
Correct the servomotor wiring.
Wiring is incorrect and the contact in encoder
wiring is faulty.
Correct the encoder wiring.
A SERVOPACK fault occurred.
Replace the SERVOPACK.
The servomotor did not
run with a reference
input.
Servomotor wiring is incorrect and the contact is
faulty.
Correct the servomotor wiring.
Encoder wiring is incorrect and the contact is
faulty.
Correct the encoder wiring.
The starting torque exceeds the maximum torque.
Reconsider the load and operation
conditions. Or, check the servomotor
capacity.
A SERVOPACK fault occurred.
Replace the SERVOPACK.
Occurred during
operation.
The effective torque exceeds the rated torque.
Reconsider the load and operation
conditions. Or, check the servomotor
capacity.
Temperature in the SERVOPACK panel is high.
Reduce the in-panel temperature to 55
°C
or less.
A SERVOPACK fault occurred.
Replace the SERVOPACK.
A.911
Vibration
Occurred during
normal operation.
Servo Amplifier gain is improper.
To adjust the gain, decrease the speed
loop gain (Pn100) and position loop gain
(Pn101), and increase the filter time
constants such as torque reference filter
(Pn401).