3 step 3, 3 step 3 -9 – Delta Electronics Elevator Drive VFD-VL User Manual
Page 48
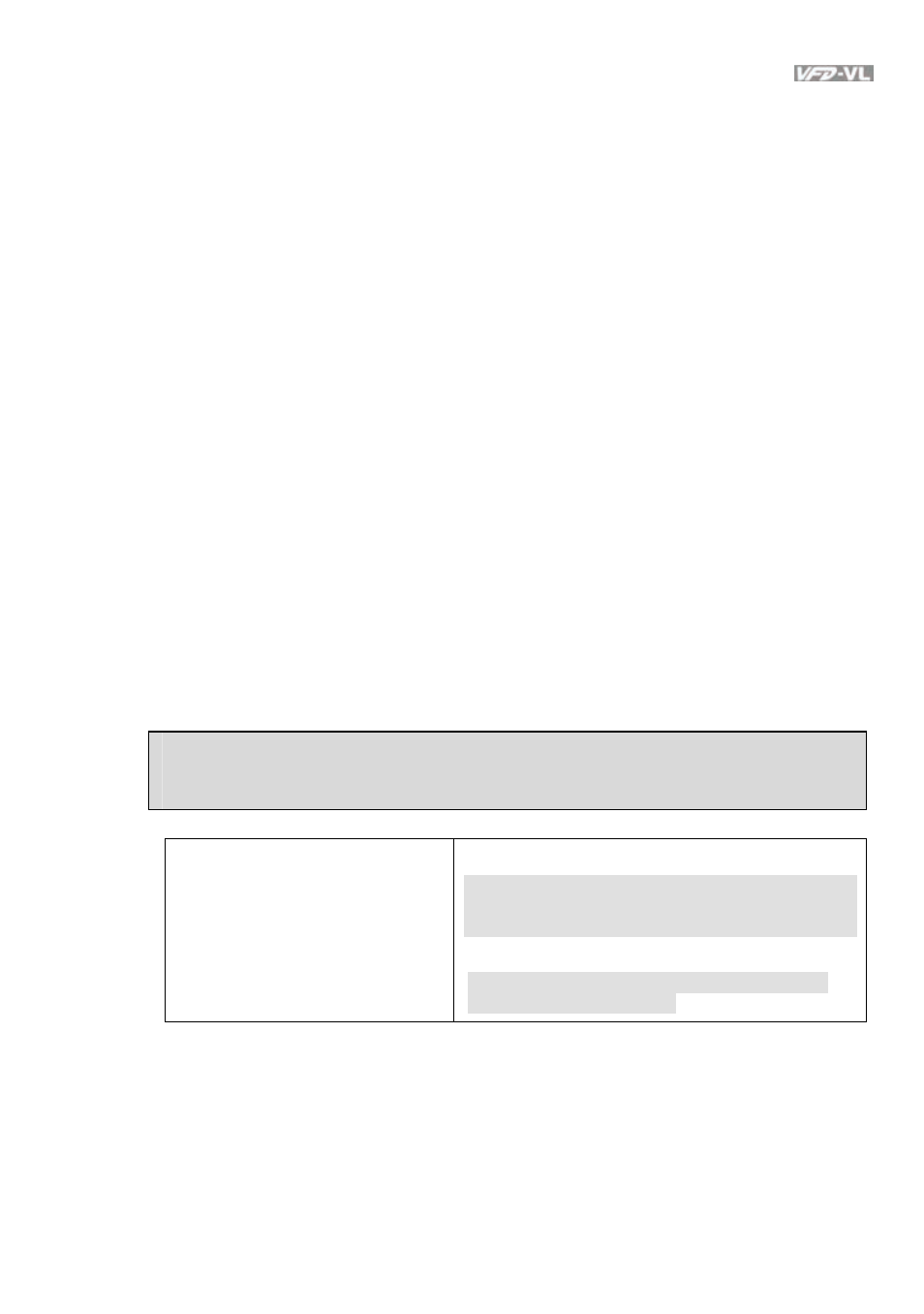
Chapter 3 Operation and Start Up|
Revision Nov. 2008, VLE1, SW V1.03 3-9
NOTE 1: It doesn’t need to release the brake in this auto tuning operation. Please make
sure that the electromagnetic valve is ON when it is used between the AC motor drive and
motor. The warning message “Auto tuning” will be displayed on the digital keypad during
tuning until it is finished. Then, the measure result will be saved into Pr.08-05 and Pr.08-07.
(Pr.08-05 is Rs of Motor and Pr.08-07 is Lq of Motor)
NOTE 2: The auto tuning of the IM motor can also be dynamic measure.
NOTE 3: It doesn’t need to release the brake for the static measure.
3.3.2.3 Step 3
Encoder settings
Selection of speed feedback cards
Please refer to appendix B.8 for details. Delta provides 4 PG cards for user to select by
their application, including EMVL-PGABL, EMVL-PGABO, EMVL-PGH01 and EMVL-
PGS01.
PM motor
It can execute “RUN” by keypad or digital terminals:
Using digital keypad: setting Pr.08-00=1 and press RUN to execute “auto measure the
angle between magnetic field and PG origin”.
Please notice that if the electromagnetic valve and brake is not controlled by the AC
motor drive, please release it by manual.
Using external terminals: Pr.00-14=3, Pr.00-15=1 (refer to step 1). Please use
“inspection” function to execute “auto measure the angle between magnetic field and PG
origin”.
For the IM motor, it doesn’t need to detect the position of the electromagnetic pole, this
function (auto measure the Angle between magnetic field and PG origin) doesn’t have
to be executed.
Measure the angle between magnetic field and PG origin: Pr.08-00=1 or 3
Pr.08-00
Motor Auto tuning
0: No function
1: Only for the unloaded motor, auto measure
the Angle between magnetic field and PG origin
(08-09)
2: For PM motor parameters
3: Auto measure the Angle between magnetic
field and PG origin (08-09)
NOTE 1: It is recommended to set Pr.08-00 to 1 (unloaded motor) for the accurate
calculation. If it needs to execute this function with loaded motor, please balance the
carriage before execution.
NOTE 2: if it doesn’t allow balancing the carriage in the measured environment, it can set
Pr.08-00=3 for executing this function. It can execute this function with loaded motor by
setting Pr.08-00=3. It will have a difference of 15~30
o
by the different encoder type.
NOTE3: It will display the warning message “Auto tuning” on the digital keypad during
measuring until the measure is finished. Then, the result will be saved into Pr.08-09.