Delta Electronics Program Transfer Module DVP-PCC01 User Manual
Dvp-pcc01, Instruction sheet
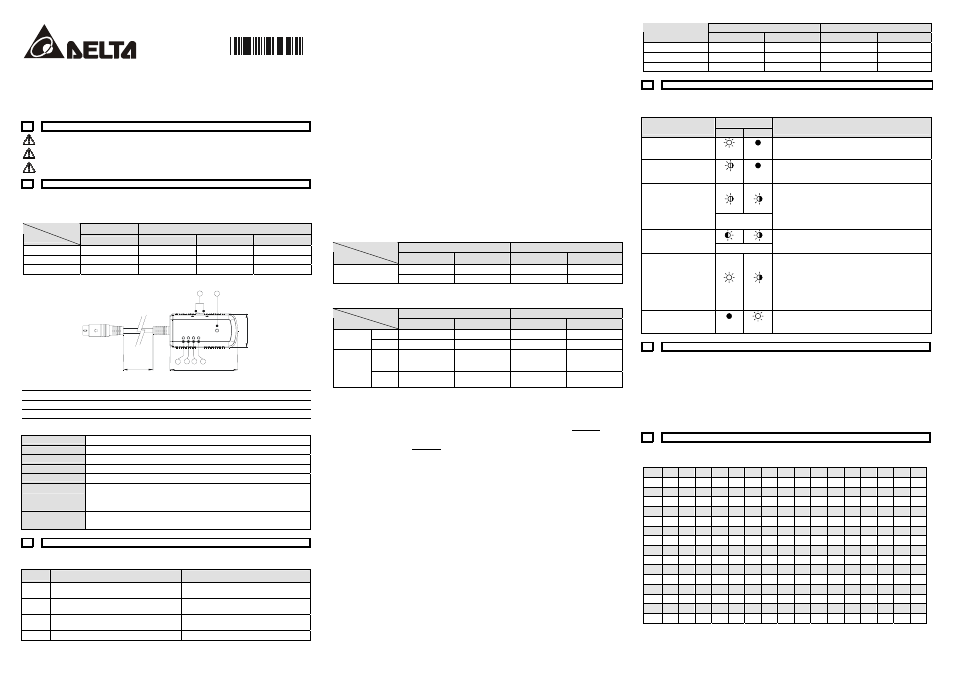
http://www.delta.com.tw/industrialautomation/
5011641001-PCE1
2006-03-10
DVP-PCC01
Program Transfer Module
Instruction Sheet
1
Warning
Please set the RD/WR switch before operating the .
Do not disconnect PCC01 before Transmission ends; otherwise, it may cause data loss in the PCC01
Do not change the RD/WR switch during PCC01 operation.
2
Introduction
PCC01 can read or write PLC programs, devices (coils and registers) and passwords to all series of PLC via
COM. It provides rapidly and safely data transmission to PLC.
Applicable Models and Read/Write Device Types:
Program area
PLC device area
Device type
Models
Program (Steps)
D register
M device
File register
DVP-ES/EX/EC/SS 4K
D0~D599 M0~M1279
N/A
DVP-SA/SX/SC 8K D0~D4999
M0~M4095
1600
DVP-EH/SV 16K
D0~D9999
M0~M4095
10000
Product Profile
PO
WE
R
OK
CO
M
ER
A
S
E
D
VP-
PC
C
0
1
ER
R
5
6
33
66.3
300
1
2 3
4
WR
RD
Unit: mm
1. Power LED
4. Error LED
2. Communication Indicator LED
5. Operation mode: read/write functional switch
3. Operation completed LED
6. PCC01 Data Erase button
Specification
Data Retention
10 years
Write Cycles
At Least 10,000 times
Transmission speed
9600 /19200 bps (PB: 9600 bps only)
Storage
-25℃~70℃ (Temperature), 5~95% (Humidity)
Operation
0℃~55℃ (Temperature), 50~95% (Humidity), Pollution degree 2
Noise Immunity
ESD: ±4KV Air Discharge
EFT: Power Line: 2KV
RS: 0.15MHz~80MHz, 10V/m
Surge : ±1KV
Vibration / Shock
Resistance
International Standard: IEC1131-2, IEC 68-2-6(TEST Fc)
IEC1131-2 & IEC 68-2-27 (TEST Ea)
3
Operation and Function Description
3.1 Read/Write Operation Sequence:
Step
(PLC→PCC01) RD (Read)
(PLC←PCC01) WR (Write)
1
Set RD/WR switch to “RD” mode
Set RD/WR switch to “WR” mode and confirm PLC
is STOP status
2
Connect PCC01 to PLC COM1.Reading will start
after 5sec. waiting.
Set RD/WR switch to “WR” mode and place the
PLC RUN/STOP switch in the STOP position.
3
After reading data from PLC, “OK” LED will light
Connect PCC01 to PLC COM1.Writing will start
after 5 sec.
4
Disconnect PCC01 when read process is done.
Disconnect PCC01 when write process is done.
3.2 Password
Function
The PCC01 transfer module can obtain a password from the source PLC along with the program. When the
program is transferred from the ACPGMXFER to the destination PLC it will compare the password and if the
password in the PLC matches or no password was previously set the transfer will complete. This will require
future ACPGMXFER transfers to a password protected PLC to have the same password as the PLC, Also if a
password is set via the transfer module any WPLSOFT users will be required to enter the password before any
program changes can be made.
The password is entered into registers D1086 and D1087 and set on by enabling M1086. These addresses
serve only as an entry point for the password at the source PLC. When the file is ‘Wrote’ to the destination PLC
the unit will be password protected and registers D1086 and D1087 will not be populated with the password. If
M1086 is not set on the passwords will be ignored.
The password is set in the source PLC by using the Batch Monitoring feature of the PLC software or hand held
programmer to enter the password into registers D1086 and D1087. Enter the value in Hexadecimal format, a
password of 1234 would be entered as follows. H3132 into register D1086 followed by H3334 into register
D1087. Refer to the table in section 6 for cross reference of valid ASCII characters. Next set M1086 on to make
this password active.
Connect the transfer module to the source PLC with the switch set to read. This will upload the program and the
password of 1234. The destination PLC will have to be in the stop mode, next connect the transfer module to
the destination PLC with the switch set to the “write” position. The transfer module will download the program
and set the password to 1234.
The password key has four digits. Each digit is 8bits number and form with ASCII in D1086 and D1087.
Example as follows:
D1086
D1087
Password Key
Password setting
High byte
Low byte
High byte
Low byte
Byte 1
Byte 2
Byte 3
Byte 4
ASCII code (HEX)
1 (0x31=H31)
2 (0x32=H32)
3 (0x33=H33)
4 (0x34=H34)
3.3 The conditions when PCC01 will read/write to an PLC:(w/ PW: with password; w/o PW: without password)
Read
Write
PCC01
PLC Status
w/o PW
w/ PW
w/o PW
w/ PW
w/o PW
Able to read
Password verify error
Unable to write
Unable to write
RUN
w/ PW
Unable to read
Unable to read
Unable to write
Unable to write
w/o PW
Able to read
Password verify error
Able to write
Able to write and
write password to
PLC
STOP
w/ PW
Unable to read
Unable to read
Password verify error
Able to write after
verification
3.4 PCC01 force PLC in RUN/STOP status
PCC01 provide Run/Stop function in DVP-ES/EX/EC series MPUs. When PCC01 ERR and OK LEDs are blinking
simultaneously in WR mode and PLC is in RUN status, user can press the ERASE button within 30 seconds to force
PLC in STOP After that, disconnect PCC01 from the PLC and then connect to PLC again. Once data write-in is
completed, push ERASE within 30 seconds while PCC01’s OK LED is ON to switch PLC status from STOP to RUN.
3.5 PCC01 Data Erase function:
Once PCC01 connects to PLC, please press and hold the ERASE button within 5 secs. Continue to hold the button
until the OK LED turns on. Release the button and the ACPGMXFER module can now be removed.
3.6 Data Duplication Function
Besides program transfer, the PCC01 can also read/write register and coil data to/from the PLC. The PCC01
will monitor coil M1085 to see if it should read/write the data. When M1085 is OFF, the PCC01 will read or
write the data depending on the operation selected. If M1085 is ON he PCC01 will not read or write the data.
Data Duplication steps:
1.) Set M1085 On/Off in PLC
2.) Select PCC01 RD/WR switch in reading or writing mode.
3.) Connect PCC01 to PLC COM1 communication port
4.) After operation is completed, “OK” LED will turn on.
5.) Disconnect PCC01 from the PLC.
3.7 Estimation of Read/Write Operating Timing
M1085=OFF
M1085=ON
Model
Read
Write
Read
Write
DVP-ES/EX/SS
35 sec.
45 sec.
30 sec.
35 sec.
DVP-SA/SX/SC
1 min. 10 sec.
1 min. 15 sec.
1 min. 5 sec.
1 min. 10 sec.
DVP-EH/SV
2 min. 50 sec.
3 min.
1 min. 10 sec.
1 min. 20 sec.
4 Error
Indication
PCC01 will show an error or warning status with the ERR and OK LEDs.
Below is the summary:
Indicator
Error Message
ERR
OK
Recommend
PCC01 Internal memory
error
On Off
PCC01 hardware may be damaged, please replace it.
Incompatible model
Blinking Off
Make sure PCC01 model record is compatible with PLC
model.
Operation error – unable
to write
Synchronous blinking
PCC01 doesn’t contain a valid program for “WR” mode.
PCC01 in “WR” mode, and PLC is in RUN mode. Please
place PLC in STOP mode.
Communication protocol error! Please confirm the PLC is in
STOP mode and reboot the PLC.
Check PLC program syntax.
Operation error – unable
to read
Cross blinking
PLC protect with password.
Communication protocol error! Please confirm PLC in STOP
mode and remove/apply power to.
Password verify error
On Blinking
PCC01 is in “RD” mode, and is protected by password.
Please push erase button when PCC01 connect to the PLC.
For more detailed operation of erasure, please reference to
section 3.4.
PCC01 is in “WR” mode, and PLC is protected by password.
Please disable the password in PLC, or set the same PLC’s
password in the PCC01. For more detailed operation , please
reference to section 3.2.
ERASE completed
Off On
Please refer to section 3.5.
5 Troubleshooting
If ERR LED is always ON or blinking. Please refer to section 4.
Disconnecting the PCC01 or powering down the PLC when the operation in progress will cause unexpected
results:
PCC01 in “RD” mode:
PCC01 data will be invalid. Please reboot the PLC again or re-connect PCC01 to PLC.
PCC01 in “WR” mode:
PLC program will be invalid. Please reboot PLC again or re-connect the PCC01 to PLC.
6 Appendix:
ASCII
Table
The password composed of 4 bytes. Each byte is an ASCII character of ‘0’~’9’, ‘A’~’Z’. ‘a’ ~’z’. The password is case
sensitive. Below is ASCII table.
HEX
0
1
2
3
4
5
6
7
8
9
A
B
C
D
E
F
ASCII
⌧
⌧
⌧
⌧
⌧
⌧
⌧
⌧
⌧
⌧
⌧
⌧
⌧
⌧
⌧
⌧
HEX
10
11
12
13
14
15
16
17
18
19
1A
1B
1C
1D
1E
1F
ASCII
⌧
⌧
⌧
⌧
⌧
⌧
⌧
⌧
⌧
⌧
⌧
⌧
⌧
⌧
⌧
⌧
HEX
20
21
22
23
24
25
26
27
28
29
2A
2B
2C
2D
2E
2F
ASCII
SP
! " # $ % & ' ( ) * + , - . /
HEX
30
31
32
33
34
35
36
37
38
39
3A
3B
3C
3D
3E
3F
ASCII
0 1 2 3 4 5 6 7 8 9 : ; < = > ?
HEX
40
41
42
43
44
45
46
47
48
49
4A
4B
4C
4D
4E
4F
ASCII
@
A B C D E F G
H
I J K
L M
N
O
HEX
50
51
52
53
54
55
56
57
58
59
5A
5B
5C
5D
5E
5F
ASCII
P
Q R S T U V W
X
Y
Z ⌧
⌧
⌧
⌧
⌧
HEX
60
61
62
63
64
65
66
67
68
69
6A
6B
6C
6D
6E
6F
ASCII
` a b C d e f g h i j k l M
n o
HEX
70
71
72
73
74
75
76
77
78
79
7A
7B
7C
7D
7E
7F
ASCII
p q r s t u v w x y z { | } ~ ⌧
Note: ‘⌧’:Denotes invalid ASCII character, do not use.