Yokogawa Removable Chassis DX1000N User Manual
Page 108
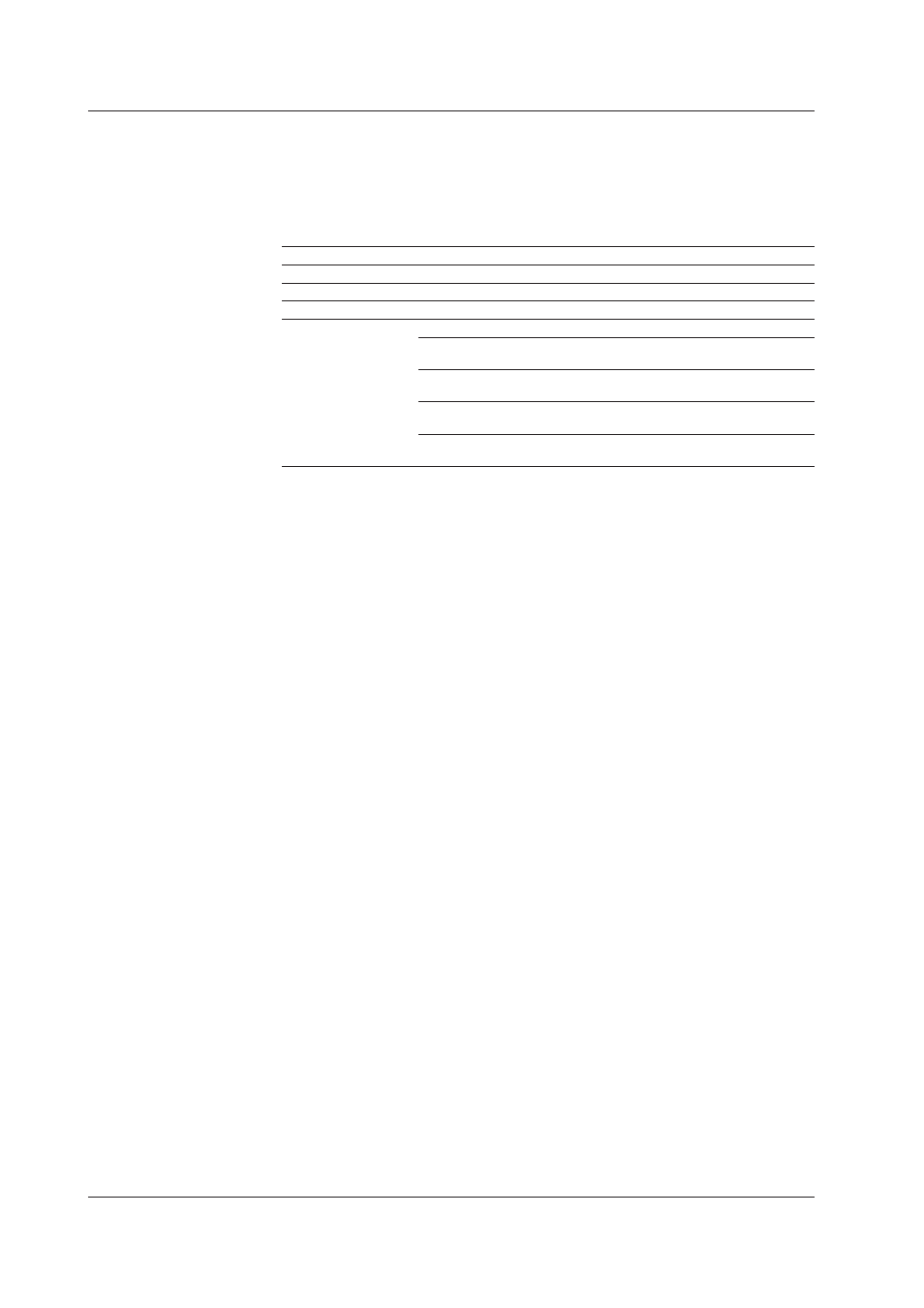
2-14
IM 04L41B01-17E
• Communication conditions
The read cycle, Inter-block delay, Time out, Auto recovery, and Retrials settings are
displayed.
• Communication Status
The communication status is displayed using the status lamp and the detail code.
Status Lamp
Detail Code
Meaning
Green
Good
Communication is operating normally.
Yellow
Command is readying.
Red
Communication is stopped.
Common to yellow
None
No response from the slave device.
and red
Func
The slave device cannot execute the command
from the DX.
Regi
The slave device does not have the specified
register.
Err
The response data from the slave device is broken
(communication error).
(Space)
The detail code is not displayed until the status is
confirmed when communication is started.
Resuming Command Transmission
You can use the front panel keys to resume command transmission to a slave device to
which communication is stopped (red status lamp).
1. Using the up and down arrow keys, select the command corresponding to the slave
device to which transmission will be resumed. The message “Push [right arrow] key to
refresh” appears.
2. Press the right arrow key. The DX starts command transmission to the specified slave.
Data When Communication Is Stopped and during Connection Retrials
For Modbus master, the communication input data and external input channel data are
held at the previous values while the command is being retried.
If the command transmission stops such as due to a connection drop, the status turns
red, and the communication input data and external input channel data are error data. On
communication channels, “+OVER” or –OVER is displayed according to the DX settings.
“*****” is displayed on external input channels.
Data Dropout
Data drop occurs when the commands from 1 to 16 do not complete within the read
cycle (see appendix 1). When a data dropout occurs, the communication input data is
held at the previous value. A message indicating the data dropout is also displayed on
the Modbus status display. If this happens, take measures such as making the read cycle
longer or reducing the number of commands. Confirm that no data dropout occurs on the
modbus status log screen.
2.6 Using the Modbus Master Function