Pd & ethernet/ip – Watlow Series PD User Manual
Page 154
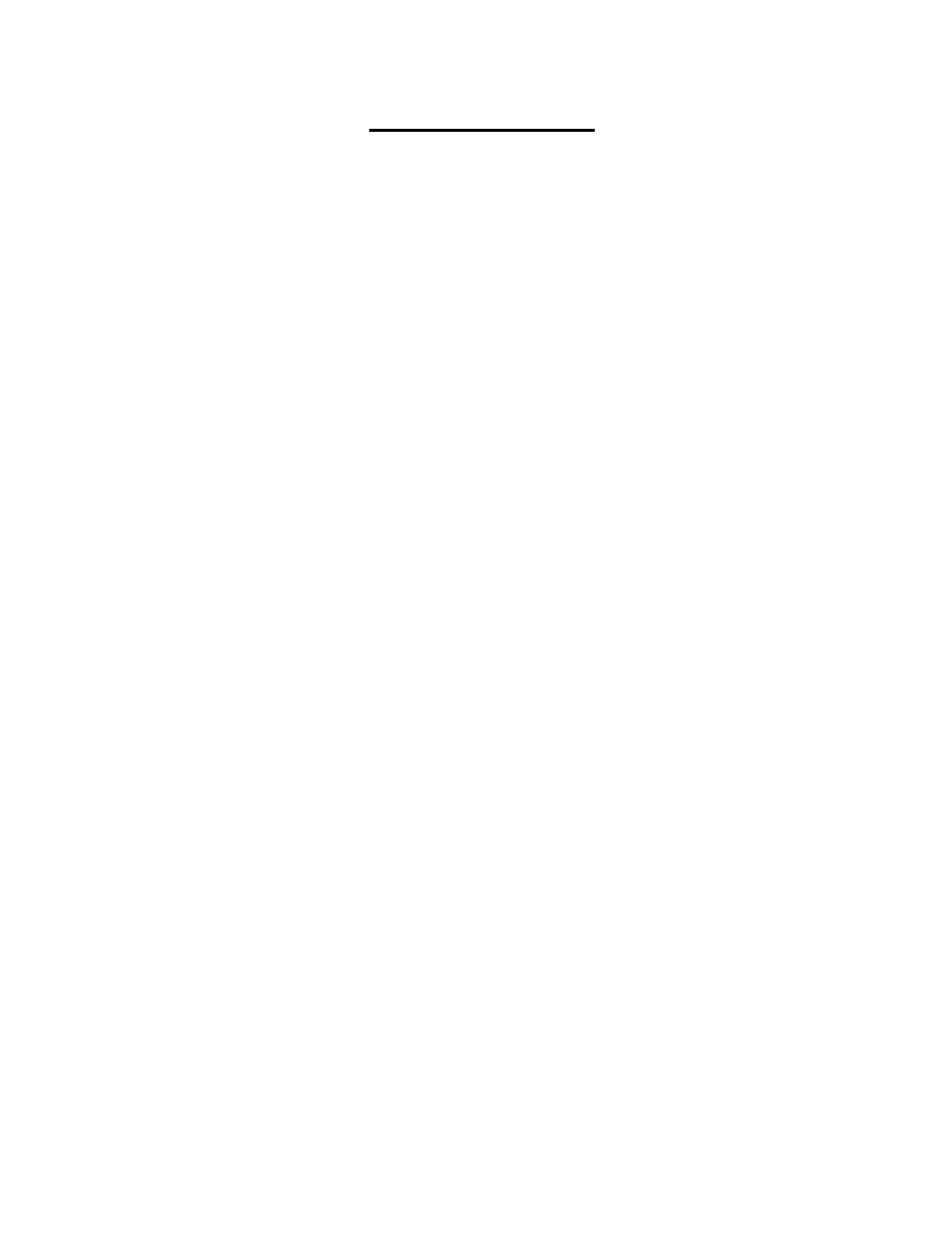
PD & EtherNet/IP
1.0 Introduction to EtherNet/IP
With the introduction of the first Programmable Logic Controllers (PLC’s) in the early to
mid 1970’s it quickly became apparent that there was a need to communicate from one PLC
to another, and then on a wider scale, from PLC to other computers within the company
infrastructure. Some of those needs involved applications with interlinking processes, such
as batch processes or assembly lines utilizing multiple controls where better synchronization
and control was required.
As time evolved the scope of the requirements for industrial communications broadened
and became better defined with specific needs being addressed as they related to industrial
communications. Most notably, those requirements and specifications revolved around the
collection of data, configuration of the control and controlled devices, and the control of the
process. Over the years, there have been many industrial protocols developed, some being
proprietary and some open where few if any met all three of these requirements. Today, with
the introduction of EtherNet/IP (Industrial Protocol) it can be said that a user can collect,
configure, and control using one protocol. Ethernet/IP is a network communication standard
capable of handling large amounts of data at speeds of 10 Mbps or 100 Mbps, and at up to
1500 bytes per packet. The specification uses an open protocol at the application layer.
EtherNet/IP makes use of the standard off-the-shelf Ethernet chip sets and the currently
installed physical media (hardware connections) and incorporates what is known today as the
Common Industrial Protocol (CIP); an open protocol at the application layer fully managed by
Open DeviceNet Vendors Association (ODVA, http://www.odva.org). CIP is the critical
component providing the ability to collect, configure, and control utilizing both implicit
messaging (real-time I/O messaging), and explicit messaging (information/configuration
messaging), with full support for peer-to- peer and multi-master configurations.
2.0 PD Connectivity over EtherNet/IP
Prior to establishing communications with the PLC the PD must be connected into the
network and either assume or be given an IP address. There are several ways that an IP
address can be established, i.e., DHCP, Auto IP, or fixed IP address. For more detail on how
to do this please refer to the section entitled “Network Services” found in Chapter 4 on page
21. Make note of the IP address once established for it will be needed when configuring the
module.
2.1 I/O Configuration using an Allen-Bradley ControlLogix Processor
Depending on the controller used the actual setup steps defined below may vary.
The specific control used in the examples given is a ControlLogix 1756-L1. Follow the
steps below to add and configure the PD as a generic Ethernet module.
1. After configuring the 1756-ENBT/A EtherNet/IP scanner right click on it and add a
new
module.
152