Control methods, Digital inputs, Output configuration – Watlow Series PD User Manual
Page 134: Auto-manual control, Auto (closed loop) and manual (open loop) control
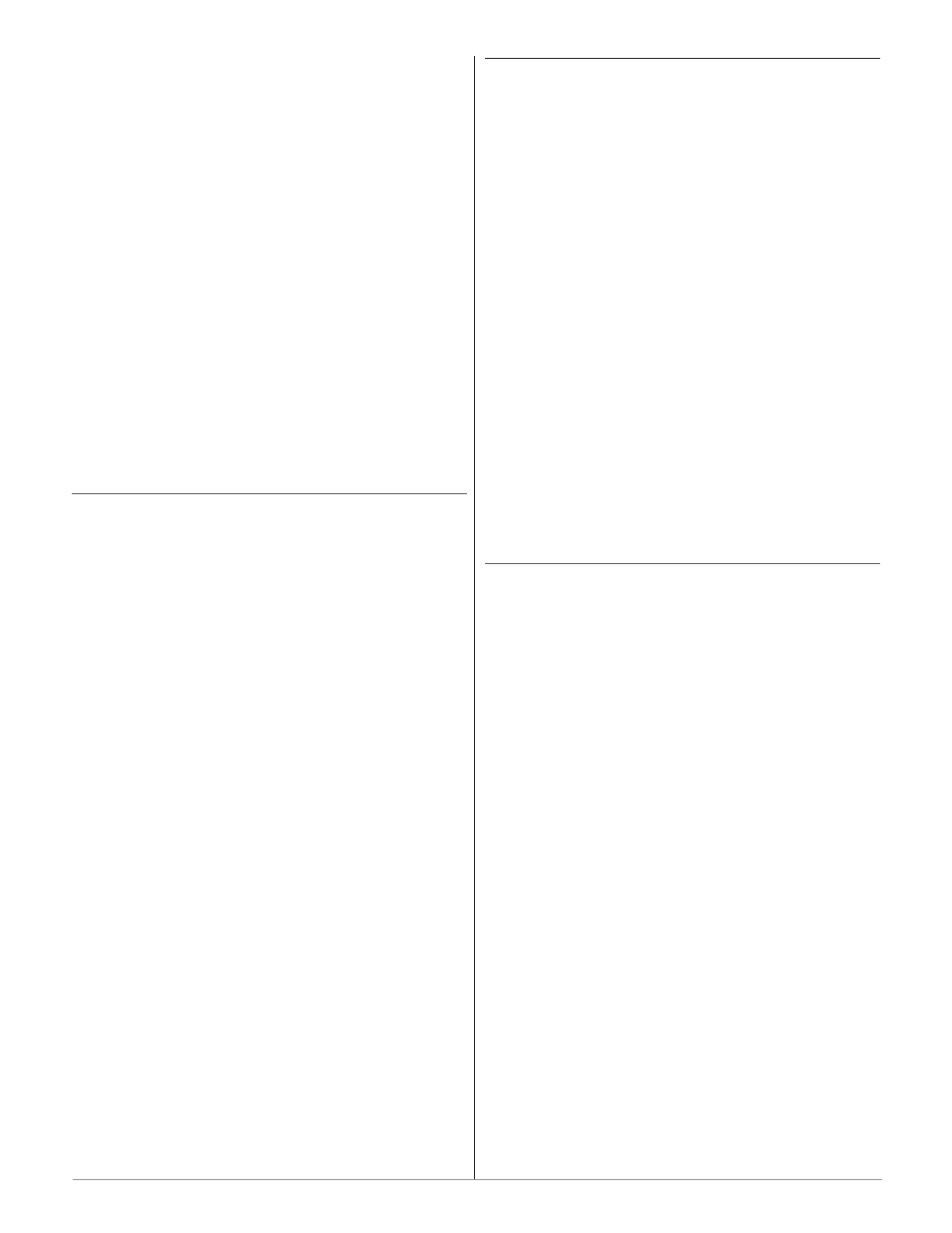
W a t l o w S e r i e s P D
■
1 3 2
■
C h a p t e r 1 0 F e a t u r e s
There are limitations when using CT inputs:
• To obtain a valid load current reading, the output
on-time must be a minimum of 0.4 seconds. To cal-
culate output on-time, multiply the percent output
times the cycle time setting. For example, with 30%
output and a 2 second cycle time, the on-time would
be 0.30 x 2 = 0.6 seconds. This on-time is greater
than the 0.4 second minimum and would result in a
valid load current reading. In this example, any out-
put power levels below 20% output, would result in
on-times that are less than 0.4 seconds. If the on-
time is too short to allow a valid current reading,
the last valid reading is used.
• CT inputs will only function with time propor-
tioned outputs (output options C, E, K or J) and the
output must be configured for fixed time base opera-
tion.
• CT inputs cannot be assigned to process outputs
(output option F).
The CT input can accept up to 50mAÅ(ac) maxi-
mum. An interstage transformer may be used for larger
loads. See Chapter 2.
Digital Inputs
Inputs 3 and 4 can be ordered as digital inputs. Digi-
tal inputs allow an operator to perform certain functions
by opening or closing a switch or applying a dc logic sig-
nal to the Series PD. This feature can add convenience,
safety or security to a system.
The digital inputs can be assigned to:
• Switch to another set point for Loop 1 or Loop 2
• Acknowledge latched alarms
• Switch to manual mode operation
• Switch a control loop off
• Pause datalogging.
All of these functions are level triggered except
acknowledge latched alarms, which is edge triggered.
For level triggered, a low or high state will trigger an
event for as long as that state exists. For edge triggered,
a rising or falling edge will trigger an event.
To enable a digital input, go to Device Configura-
tion > Inputs > Digital Input 3 or 4 > Function, and
select the the action to take based upon the digital in-
put status.
To configure the CT input, go to Device Configura-
tion > Inputs > Digital Input 3 or 4. Select configura-
tion parameters to match your application require-
ments.
To monitor Digital Input Status, go to Monitor De-
vice > Input Status > Input 3 or 4 Value and Sta-
tus. This indicates if the event is active and what digi-
tal input function is selected.
Control Methods
Output Configuration
Each controller output can be assigned to a Control
Loop and configured as a heat output, a cool output, an
event/alarm output or off (disabled). No dependency lim-
itations have been placed on the available combinations.
The outputs can be configured in any combination. For
instance, all outputs could be set to cool.
Analog outputs can be scaled for any desired current
range between 0 and 20 mA or voltage range between 0
to 10V. The ranges can be reversed to high-to-low for re-
verse acting devices.
Heat and cool outputs use the Control Loop Set
Point and Control Loop page parameters to determine
the output value. All heat and cool outputs for each loop
use the same set point value. Heat and cool each have
their own set of control parameters. All heat outputs for
each loop use the same set of heat control parameters
and all cool outputs for each loop use the same set of
cool output parameters.
Each alarm output has its own set of configuration
parameters and set points. An event/alarm can be as-
signed to any active analog input, allowing independent
operation.
Auto (closed loop) and Manual (open loop)
Control
The Series PD has two basic modes of operation, auto
mode and manual mode. Auto mode allows the controller
to decide whether to perform closed loop control or to fol-
low the settings of the Input Failure Parameter setting.
The manual mode only allows open loop control. The Se-
ries PD controller is normally used in the auto mode.
The manual mode is usually only used for specialty ap-
plications or for troubleshooting.
Manual mode is open loop control that allows the
user to directly set the power level to the controller’s
output load. No adjustments of the output power level
occur based on temperature or auto set point in this
mode.
In auto mode, the controller monitors the input to
determine if closed loop control is possible. The con-
troller checks to make certain a functioning sensor is
providing a valid input signal. If a valid input signal is
present, the controller will perform closed loop control.
Closed loop control uses a process sensor to determine
the difference between the process value and the auto
set point. Then the controller applies power to a control
output load to reduce that difference.
If a valid input signal is not present, the controller
will indicate an input status error at Monitor Device
> Input Status > Status. The input number will also
be highlighted with a red box.