Yaskawa DR2 Sigma Servo User Manual
Page 449
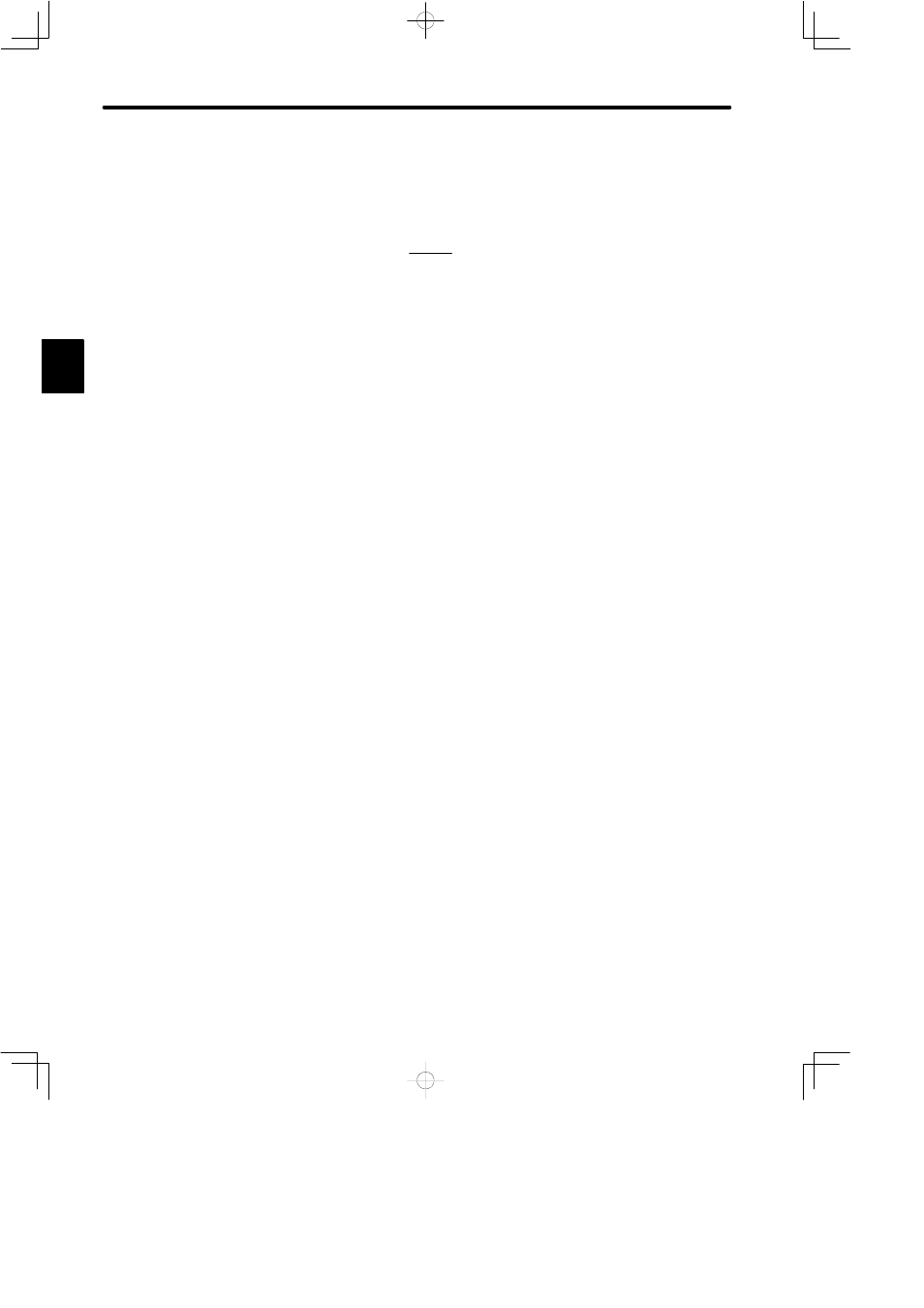
SERVO ADJUSTMENT
B.3.2 Manual Adjustment cont.
438
This integration element can produce a delay in the servo system, and the positioning
setting time increases and response becomes slower as the time constant increases.
However, the integration time constant must be increased to prevent machine vibra-
tion if the load inertia is large or the mechanical system includes a vibration elements.
The following formula calculates a guideline value.
Ti: Integration Time Constant (sec)
Kv: Speed Loop Gain (Hz) (calculated above)
Ti ≥ 2.3 ×
1
2π × Kv
c) Torque Reference Filter Time Constant (Cn-17)
When a ball screw is used, torsional resonance may occur which increases the pitch
of the vibration noise.
These vibrations can sometimes be overcome by increasing the torque reference fil-
ter time constant.
However, this filter can produce a delay in the servo system, as is the integration time
constant, and its value should not be increased more than necessary.
d) Position Loop Gain
The position loop gain user constant sets the servo system response.
The higher the position loop gain is set, the better the response and shorter the posi-
tioning times.
To enable a high setting of the position loop gain, increase the machine rigidity and
raise the machine characteristic frequency.
Increasing the position loop gain only to improve the response can result in oscillating
response of the overall servo system, that is, the speed references output from the
position loop oscillate. Therefore, also increase the speed loop gain while observing
the response.
2) Adjustment Procedure
a) Set the position loop gain to a low value and increase the speed loop gain (Cn-04)
within the range that no abnormal noise or oscillation occurs.
b) Slightly reduce the speed loop gain from the value at step 1, and increase the position
loop gain in the range that no overshooting or vibration occurs.
c) Determine the speed loop integration time constant (Cn-05), by observing the posi-
tioning set time and vibrations in the mechanical system.
The positioning set time may become excessive if the speed loop integration time
constant (Cn-05) is too large.
d) It is not necessary to change the torque reference time constant (Cn-17) unless tor-
sional resonance occurs in the machine shafts.
Torsional resonance may be indicated by a high vibration noise. Adjust the torque ref-
erence filter time constant to reduce the vibration noise.
e) Finally, fine adjustment of the position gain, speed gain, and integration time constant
is required to determine the optimum point for step response, etc.
B