Rockwell Automation 999 IMC S Class Compact Motion Controller (Cat. No. 4100-999-122) User Manual
Page 95
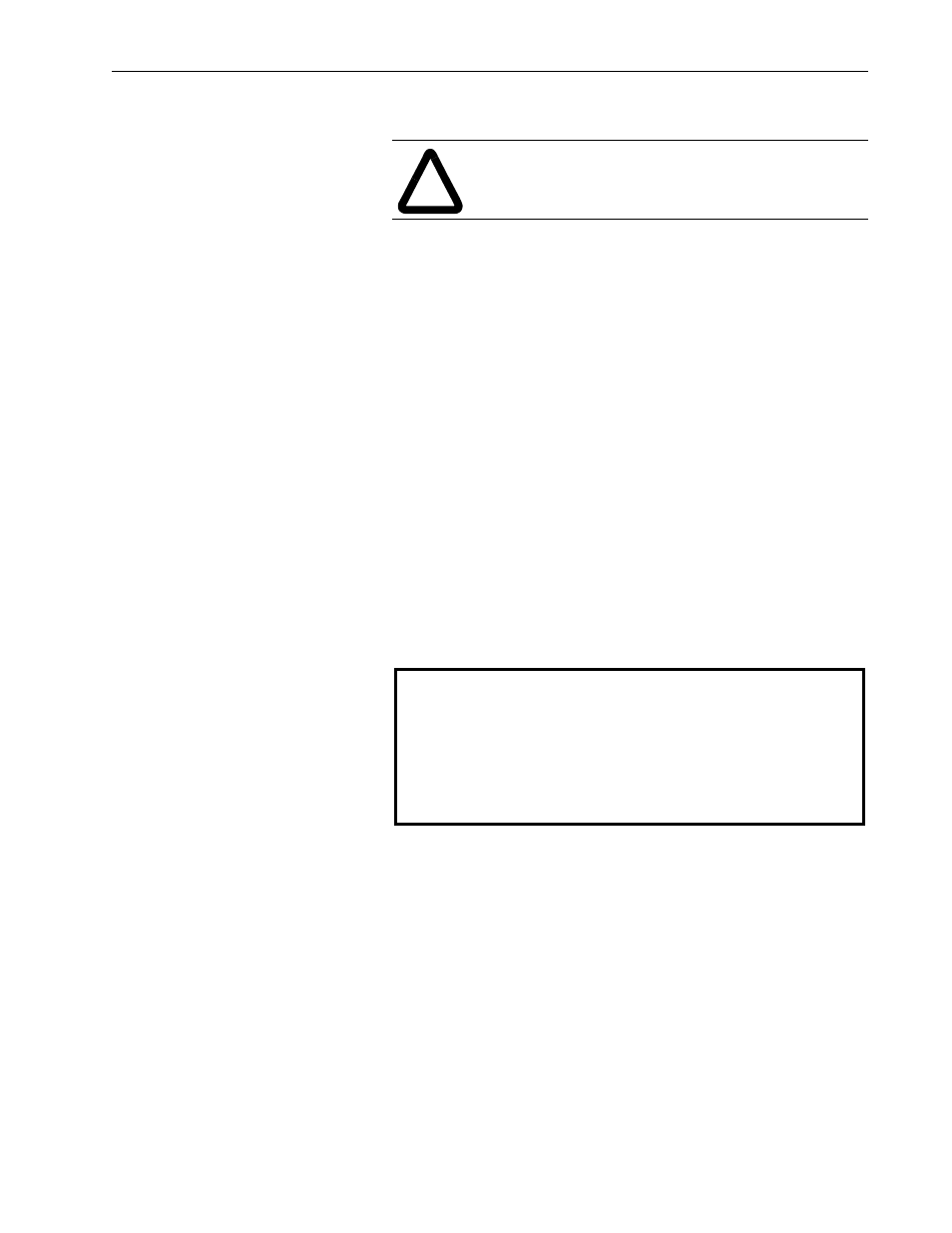
Understanding IMC-S/23x Setups
5-15
Publication 999-122 - January 1997
is displayed and you must select another axis.
Each
SERVO
axis of the IMC-S/23x can be configured to respond to
the various motion faults in different ways. If a fault action is set to
STOP MOTION
, then when the fault occurs, the axis immediately
decelerates to a stop without disabling feedback or the drive enable
output. A fault action of
STOP MOTION
is the gentlest reaction to a
fault. It is usually used for less severe faults, since it is relatively easy
to recover from a
STOP MOTION
fault action.
If
KILL DRIVE
is selected, when the fault occurs, axis feedback is
immediately disabled, the servo amplifier output is zeroed, and the
appropriate drive enable output is deactivated.
KILL DRIVE
is the
most severe reaction to a fault and it is usually used for faults which
could endanger the machine or the operator if power is not removed as
quickly as possible.
If a fault action is set to
STATUS ONLY
, motion faults must be handled
by the application program. In general, this setting should only be used
in applications where neither the standard
STOP MOTION
nor
KILL
DRIVE
actions are appropriate.
The recommended setting of the fault action configuration parameters–
suitable for most applications–is shown below:
!
ATTENTION: Danger of axis runaway exists if
KILL DRIVE
is not selected as the fault action.
Hard Overtravel Action? KILL DRIVE
Soft Overtravel Action? STOP MOTION
Pos Error Fault Action? KILL DRIVE
Drive Fault Action? KILL DRIVE
Encoder Noise Fault Action? STATUS ONLY
Encoder Loss Fault Action? KILL DRIVE