Rockwell Automation 999 IMC S Class Compact Motion Controller (Cat. No. 4100-999-122) User Manual
Page 123
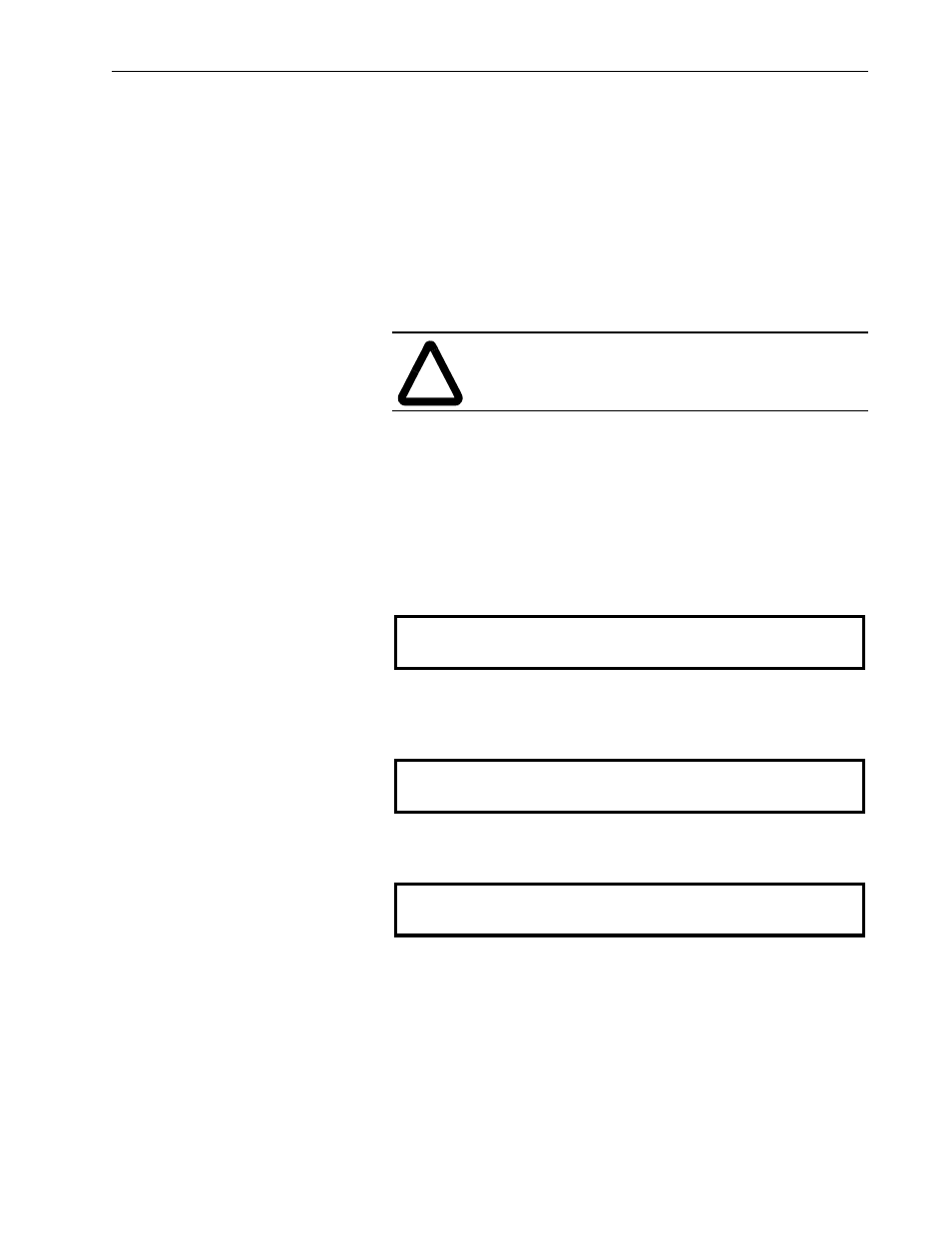
Understanding IMC-S/23x Setups
5-43
Publication 999-122 - January 1997
is displayed and you must select another axis. Since the imaginary axis
has no physical connections, the hookup diagnostics are not available
for it.
Checking Motors and
Encoders
The Motor/Encoder Test is used with physical
SERVO
axes to check
for proper electrical connection of the servo drive and encoder or other
feedback device and also to establish the correct rotational direction of
the servo drive and encoder. Establishing these motor and encoder
polarities ensures that the axis will not run away when the feedback
loop is closed.
Enter a value for the test increment in the position units of this axis.
The test increment is the maximum distance that the axis will move
during the motor/encoder test assuming that the encoder is functioning
properly. Usually, this value can be quite small, but it must be large
enough so that the motor and encoder produce some measurable
motion.
First, for velocity loop servo amplifiers, any offset in the amplifier is
compensated. The message
is displayed while the IMC-S/23x attempts to make the motor stand
still. For torque loop servo amplifiers, both the offset and the deadband
are compensated and the message
is displayed. If the offset or deadband cannot be compensated, the
message
is displayed. Check the connections between the IMC-S/23x and the
servo amplifier and between the servo amplifier and the motor and make
sure that the drive system is working properly. Then re-run the
motor/encoder test.
!
ATTENTION: Press ESC (Escape) to immediately
abort the motor/encoder test.
Test Increment (Position Units) =
Compensating for Drive Offset...
Test Increment (Position Units) =
Compensating for Offset & Deadband...
*** Motor Does NOT Respond!
*** Check Motor Hookup and Retest