Rockwell Automation 999 IMC S Class Compact Motion Controller (Cat. No. 4100-999-122) User Manual
Page 19
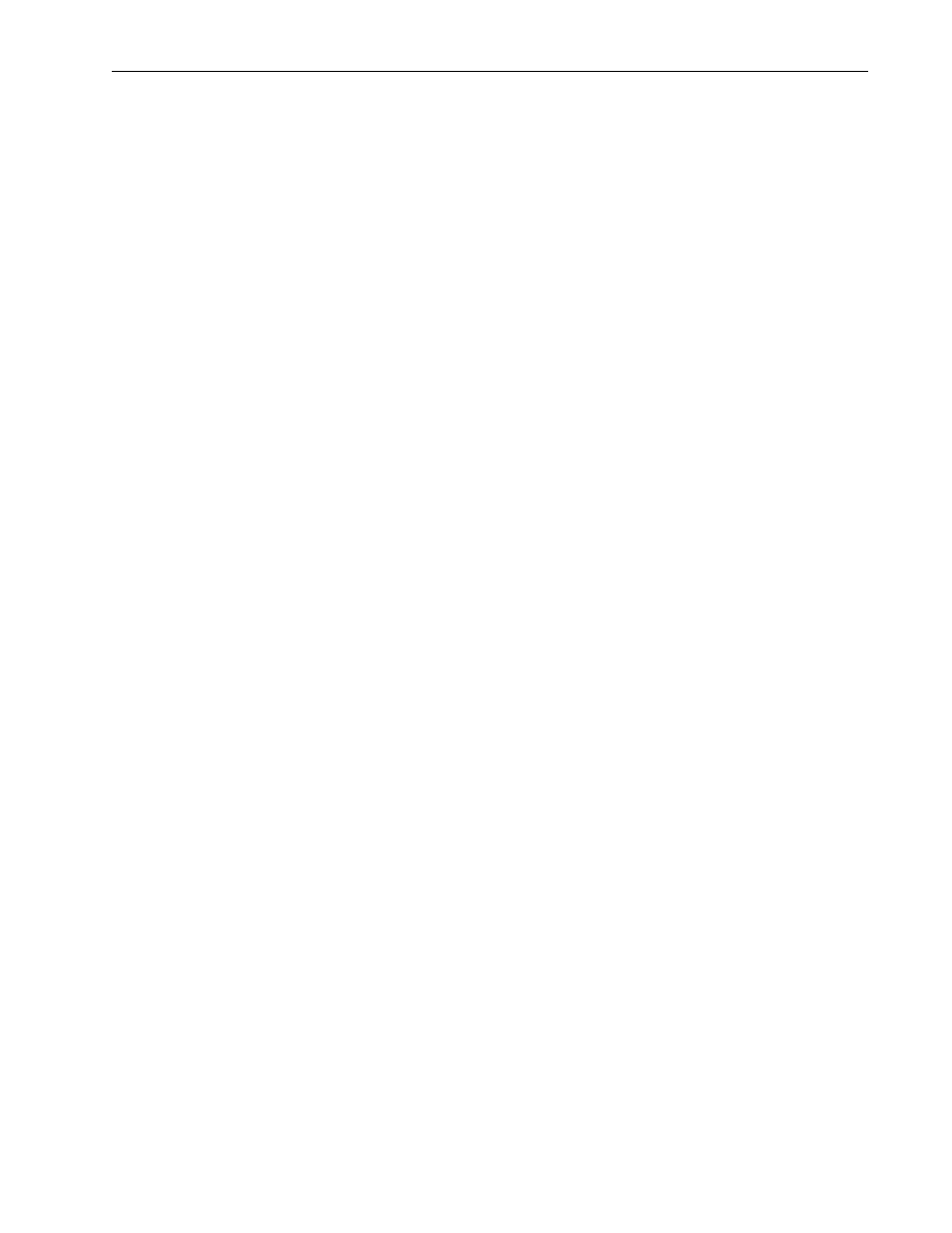
Introduction
2-3
Publication 999-122 - January 1997
•
Wide position, speed, acceleration, and deceleration ranges for
precise control.
•
Separately programmable acceleration and deceleration rates for
maximum versatility.
•
Trapezoidal, parabolic, and S-curve velocity profiles.
•
Rotary mode with electronic unwind allows unlimited position
range for rotary axes.
•
Merge motion function allows seamless transition between all types
of motion.
•
Most motion parameters (including master axis for electronic gears
and cams) can be changed on-the-fly with no delays.
•
Powerful floating-point math capabilities including transcendental
functions (sin, cos, log, etc.).
•
Sophisticated Nested Digital Servo Control Loop with automatic
servo setup for quick and easy servo tuning.
•
Isolation of all external connections from the microprocessor logic
for reliable performance.
•
4 MHz maximum feedback count rate allows high speed operation
without sacrificing resolution.
•
Encoder loss detection protects operators and machinery from
damage in the event of encoder feedback failure.
•
Isolated 16-bit DACs for smooth motion. Software offset correction
eliminates drift with analog servo drives.
•
Field-configurable servo outputs allow independent selection of
±10V or ±150
µΑ
signal format for each axis.
•
Programmable position lock and position error tolerances for servo
fault protection.
•
Programmable directional software travel limits for enhanced
overtravel protection.
•
Velocity Feedforward to reduce following error.
•
Four optically isolated limit switch inputs for a home switch,
positive and negative overtravel switches, and a drive fault signal
for each axis.
•
Relay-contact drive enable output for each axis.
•
Optically isolated high-speed position registration input for each
axis for position synchronization and registration applications.
•
CPU Watchdog with front-panel LED indicator for fail-safe
protection.